AC Servo Motor vs DC Servo Motor: Understanding the Differences
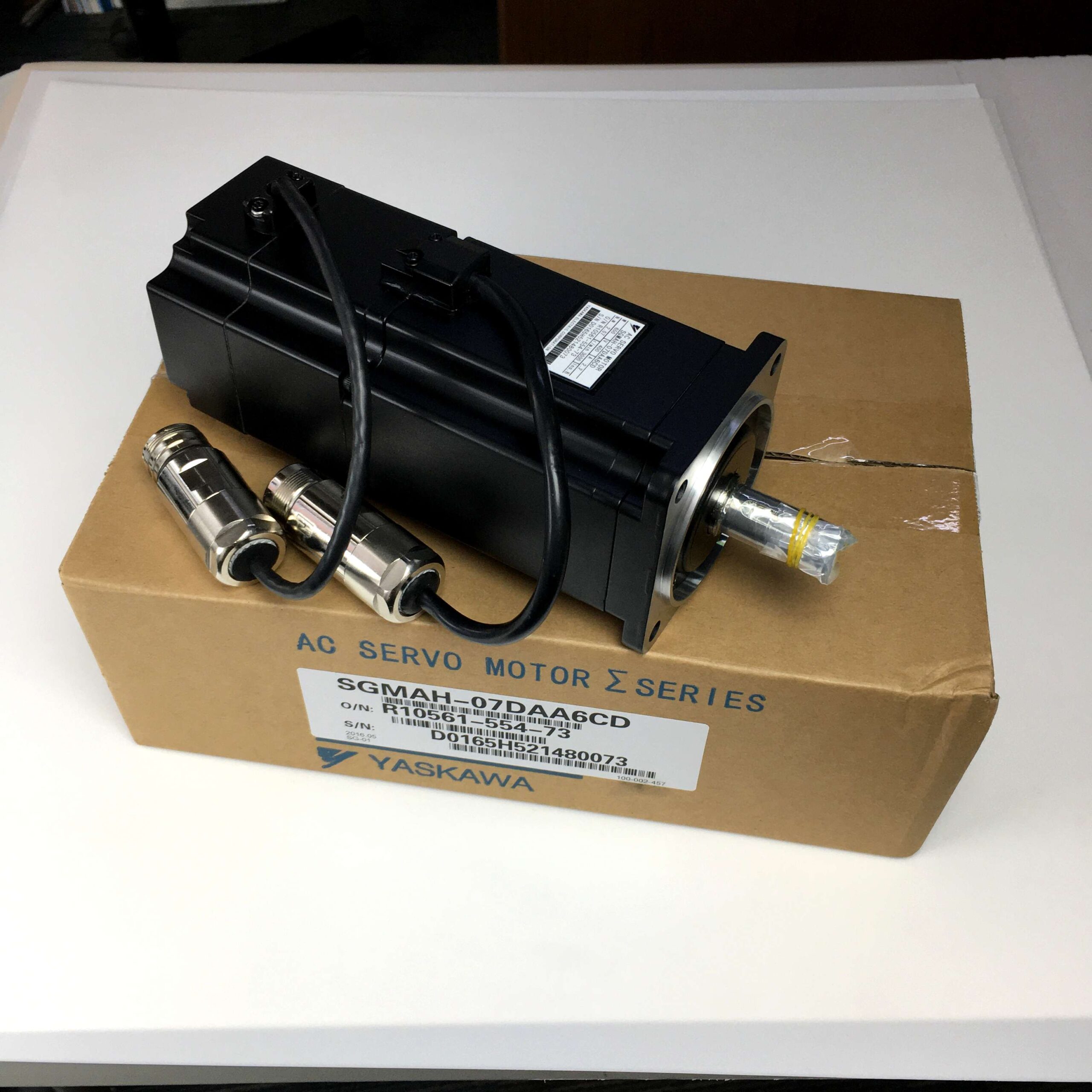
This article explores the fundamental differences between AC and DC servo motors, two vital components in the realm of motion control and automation. We’ll delve into their unique characteristics, advantages, and disadvantages, providing you with a comprehensive understanding of each type. Whether you’re a seasoned engineer or a student just beginning to explore the world of servo systems, this article will provide valuable insights, making it well worth your time.
What is an AC Servo Motor?
An AC servo motor is a type of electric motor that utilizes alternating current (AC) to generate motion. These motors are known for their high torque output, precise speed control, and ability to handle high currents. There are two main categories of AC servo motors: synchronous and induction. Synchronous AC servo motors use permanent magnets in their rotor design, allowing them to rotate in sync with the frequency of the supplied AC power. Induction or asynchronous motor types, on the other hand, rely on electromagnetic induction to induce current in the rotor, creating a magnetic field that interacts with the stator’s field, producing rotation. The design of AC servo motors allows for high efficiency and durability, making them suitable for demanding industrial applications.
An AC servo motor is a type of synchronous motor that’s commonly used in industrial servo applications. Unlike induction motors, which rely on slip to produce torque, synchronous AC servo motors maintain a fixed relationship between the rotor speed and the frequency of the applied alternating current (AC). This allows for precise motor control and position control. These motors are powered by AC servo drives, such as the SGD7S-120A00A Original Yaskawa Single axis servo driver, which regulate the voltage and frequency of the AC power supplied to the motor, allowing for accurate control over speed and position. AC servo motors are typically brushless, which means they don’t have brushes or a commutator, reducing maintenance and increasing lifespan. The armature of the motor is located in the stator, and the rotor usually contains permanent magnets.
What is a DC Servo Motor?
A DC servo motor is another type of servo motor that operates on direct current (DC). These motors are often favored for their simplicity, ease of control, and linear torque-speed characteristics. DC servo motors can be either brushed or brushless. Brushed DC motors use a commutator and brushes to switch the current in the rotor windings, while brushless DC motors use electronic commutation to achieve the same result. DC servo motors are commonly used in applications where cost and simplicity are prioritized over the high performance of AC servo motors. DC servo motor is a type of motor that provides precise position control and speed control by utilizing a closed-loop control system. The motor is powered by direct current (DC power). A sensor, such as an encoder, provides feedback to the control system regarding the motor position. The control system then adjusts the current to the motor to maintain the desired position or speed.
DC servo motors can be either brushed or brushless. Brushed DC servo motors use brushes to deliver current to the rotor windings, while brushless DC servo motors utilize electronic commutation. DC servo motors are typically used in applications where cost and simplicity are major considerations, such as in robotics and small automation systems. For a deeper understanding of specific models, explore the Original Panasonic Servo Motor MINAS A6 3KW MHMF302L1G6M. Although DC servo motors are often considered less powerful than their AC counterparts, advancements in brushless DC (BLDC) technology have narrowed this performance gap.
What are the Key Differences Between AC and DC Servo Motors?
The primary differences between AC and DC servo motors lie in their power source, construction, and control methods. Here’s a table summarizing the key distinctions:
Feature | AC Servo Motor | DC Servo Motor |
---|---|---|
Power Source | Alternating Current (AC) | Direct Current (DC) |
Construction | Typically brushless, rotor with magnets | Brushed or brushless, rotor with windings |
Commutation | Electronic | Mechanical (brushes) or Electronic |
Torque | High torque at high speeds | High torque at low speeds |
Speed Control | Precise speed control via servo drive | Simple speed control via voltage regulation |
Efficiency | Generally higher efficiency | Lower efficiency, especially in brushed types |
Maintenance | Low maintenance due to brushless design | Higher maintenance for brushed types |
Cost | Higher initial cost | Lower initial cost |
Applications | Industrial automation, robotics, CNC machines | Robotics, small automation, consumer electronics |
Motor Control | Complex motor control using variable frequency drive or servo drive. | Simple motor control using DC drives. |
AC servo motors are usually brushless, offering higher efficiency, lower maintenance, and higher torque at high speeds. DC servo motors, on the other hand, can be brushed or brushless, with brushed types being simpler and less expensive but requiring more maintenance due to brush wear. AC servo motors also tend to offer more precise control over speed and position, thanks to sophisticated servo drive systems. DC servo motors offer a wider range of sizes and are still used in many applications, especially where the motor is small and cost is a primary factor. While DC servo motors were historically more common, AC servo motors have become increasingly prevalent in industrial settings due to their superior performance. AC servo motors can handle higher current surges, making them suitable for applications requiring rapid acceleration and deceleration. They often use servo motors use permanent magnets in their rotor design.
How do AC and DC Servo Motors Compare in Terms of Performance?
AC servo motor and DC servo motor performance can be compared across several parameters:
- Torque: AC servo motors maintain high torque even at high speeds, thanks to their synchronous operation. DC servo motors generally exhibit higher torque at low speeds but experience a drop-off as speed increases, particularly in brushed types.
- Speed: AC servo motors typically offer a wider speed range and better speed control than DC servo motors. The servo drive allows for precise adjustment of the motor’s rotational speed.
- Efficiency: AC servo motors, especially brushless types, are generally more efficient than DC servo motors. This means less energy is lost as heat, leading to better motor performance and lower operating costs.
- Response: AC servo motors tend to have a faster response time due to their ability to handle high currents and the sophisticated control algorithms implemented in AC servo drives.
- Positioning Accuracy: Both AC and DC servo motors can achieve high positioning accuracy, but AC servo motors often have an edge due to their closed-loop control systems and higher resolution encoders.
While DC servo motors may be suitable for applications where precise positioning and motion control are not critical, AC servo motors are preferred when high performance, speed, and accuracy are paramount.
What are the Advantages and Disadvantages of AC Servo Motors?
Advantages:
- High Torque at High Speeds: AC servo motors maintain high torque output even at high speeds, making them suitable for applications requiring rapid acceleration and deceleration.
- High Efficiency: Brushless AC servo motors are highly efficient, converting a large percentage of electrical energy into mechanical energy, resulting in lower operating costs.
- Precise Control: AC servo motors, coupled with advanced servo drives like the Original Panasonic Servo Motor MINAS A5 1KW MSME102GCHM/MSME102GCH/G1H/GCDM, offer extremely precise speed and position control, essential for applications like CNC machining and robotics.
- Low Maintenance: With no brushes to wear out, brushless AC servo motors require minimal maintenance, reducing downtime and maintenance costs.
- High Reliability: AC servo motors are designed for durability and can withstand harsh industrial environments.
Disadvantages:
- Higher Initial Cost: AC servo motors and their associated control systems are generally more expensive than DC servo motor systems.
- Complexity: AC servo systems are more complex to set up and configure than DC servo systems, requiring specialized knowledge and equipment.
- Larger Size: For a given power output, AC servo motors may be larger and heavier than DC servo motors.
What are the Advantages and Disadvantages of DC Servo Motors?
Advantages:
- Lower Initial Cost: DC servo motors, especially brushed types, are generally less expensive than AC servo motors, making them attractive for cost-sensitive applications.
- Simplicity: DC servo systems are simpler in design and easier to understand and implement than AC servo systems.
- High Starting Torque: DC servo motors exhibit high torque at low speeds, making them well-suited for applications requiring high starting torque.
- Compact Size: DC servo motors can be more compact and lightweight than AC servo motors of comparable power.
Disadvantages:
- Lower Efficiency: DC servo motors, particularly brushed types, are generally less efficient than AC servo motors, leading to higher energy consumption and heat generation.
- Higher Maintenance: Brushed DC servo motors require regular maintenance due to brush wear, increasing downtime and maintenance costs. Brushless DC servo motors require less maintenance but are more expensive than brushed types.
- Limited Speed Range: DC servo motors may have a more limited speed range compared to AC servo motors.
- Torque Drop-off at High Speeds: DC servo motors, especially brushed types, experience a significant drop in torque as speed increases.
DC servo motors are a viable option for applications where cost is a major concern and high performance is not critical. However, they may not be suitable for demanding industrial applications requiring high speed, high torque, and precise control.
Which Type of Servo Motor is Right for My Application: AC or DC?
The choice between an AC servo motor and a DC servo motor depends on the specific requirements of your application. Here’s a guide to help you decide:
Choose an AC Servo Motor if:
- Your application demands high torque at high speeds.
- Precise speed and position control are critical.
- High efficiency and low energy consumption are important.
- Long-term reliability and minimal maintenance are desired.
- Your application involves rapid acceleration and deceleration.
- Your budget allows for a higher initial investment.
Choose a DC Servo Motor if:
- Cost is a primary concern.
- Simplicity and ease of implementation are priorities.
- High starting torque is required, but high-speed performance is less critical.
- Compact size and lightweight are important.
- Your application does not require the high precision and performance offered by AC servo motors.
In many industrial settings, AC servo motors have become the preferred choice due to their superior performance characteristics. However, DC servo motors continue to be used in various applications, particularly where cost and simplicity are major factors. For instance, small robots or hobbyist projects might utilize DC servo motors, while industrial automation systems often rely on AC servo motors for their precision and power. Motors can be used in a wide range of applications, from simple position control to complex motion control systems. Motors are much more efficient than stepper motors. Also, the choice may depend on the scale of the project. For example, a small, battery-powered device might use a DC servo motor because the motor is small and can be powered by a DC source. On the other hand, a large industrial machine would likely use an AC servo motor because the motor is also capable of handling higher power and providing more precise control. Remember that two types of servo motors are available, brushed and brushless DC motors, as well as synchronous AC motors are also available, and each type has its advantages and disadvantages. Always remember to choose the type of motor that best suits your specific needs. If you are unsure, you may want to consult with a servo motor expert or supplier, like those at Servo Motor Store.
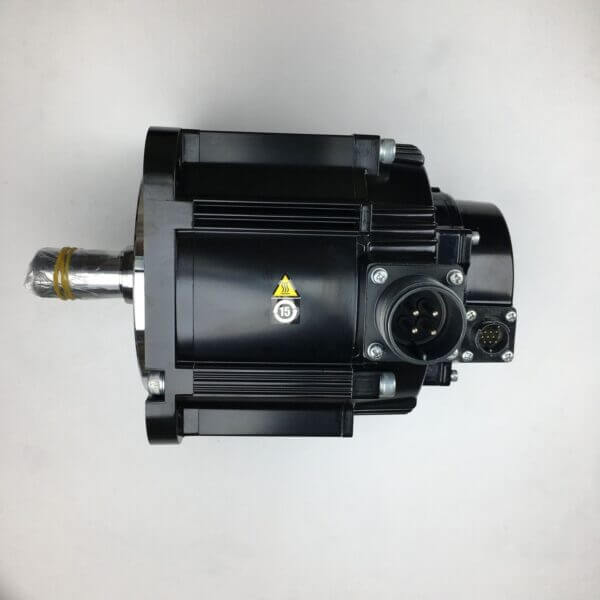
Summary
Here are the key takeaways from this article:
- AC servo motors and DC servo motors are two distinct types of motors used in motion control applications.
- AC servo motors typically offer higher performance, efficiency, and precision than DC servo motors.
- DC servo motors are generally less expensive and simpler to implement than AC servo motors.
- Brushless AC servo motors require minimal maintenance, while brushed DC servo motors require regular brush replacement.
- The choice between an AC servo motor and a DC servo motor depends on the specific requirements of your application, including torque, speed, precision, efficiency, cost, and maintenance considerations.
- AC servo motors are well-suited for demanding industrial applications, while DC servo motors are often used in cost-sensitive applications where high performance is not critical.
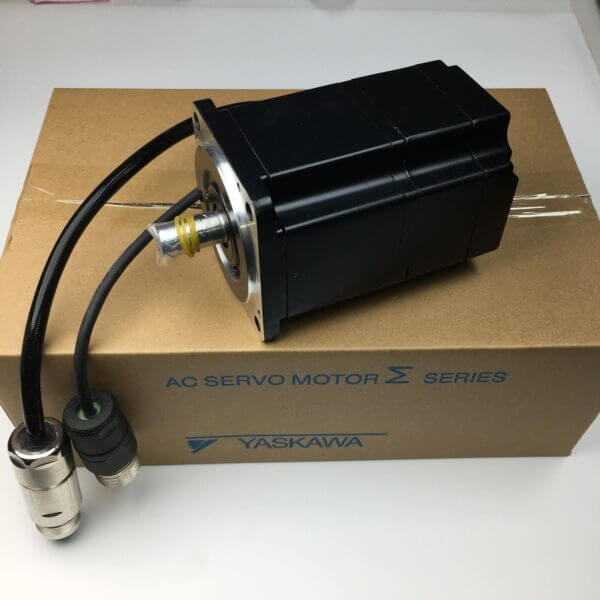