Can a Servo Motor be Wired in Reverse?
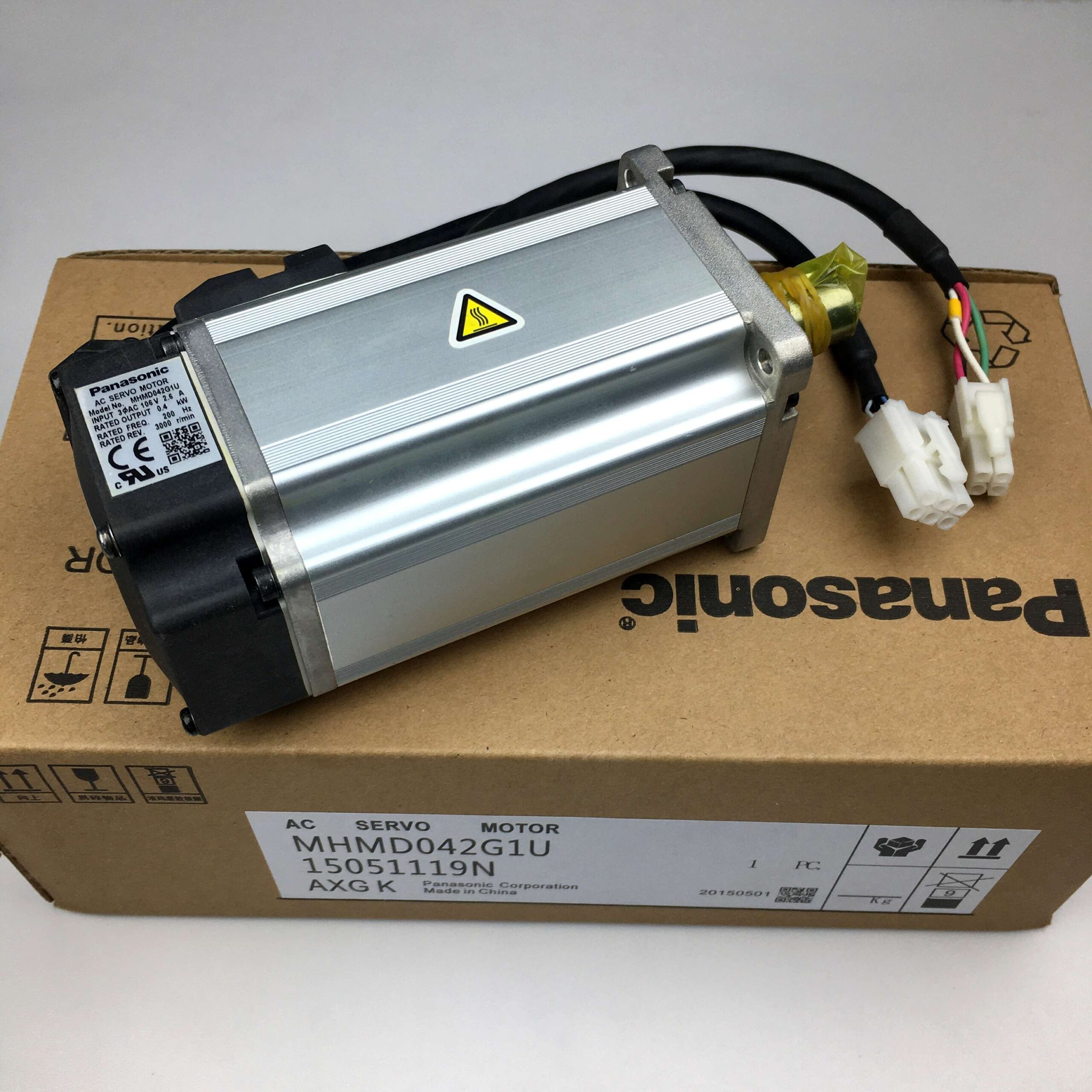
When it comes to servo motors, understanding their wiring configuration is essential to ensure that they operate correctly and safely. A common question many people have is: can a servo motor be wired in reverse? The answer is yes, but there are important considerations and risks involved. Wiring a servo motor incorrectly can lead to operational issues, reduced lifespan, or even irreversible damage. In this article, we will explore what happens when you wire a servo motor in reverse and how to handle it safely.
Servo motors are an integral part of many CNC machines, robotics, and automation systems due to their precise control over position, speed, and torque. Incorrect wiring can easily undermine the reliability that makes servo motors so popular. Let’s dive into the details of wiring, the consequences of reversing it, and safe practices.
What Happens When You Wire a Servo Motor in Reverse?
Effects on Motor Operation
When a servo motor is wired in reverse, the most immediate effect is that the motor will rotate in the opposite direction from what you intended. However, the consequences of wiring a servo in reverse go beyond just changing the direction of rotation. Here are some key issues to consider:
- Reverse Current Flow: Reversing the wiring can lead to improper current flow through the motor windings, causing overheating or potential damage.
- Loss of Control Feedback: Many servo systems rely on feedback from sensors like encoders. Incorrect wiring can disrupt this feedback, making it impossible for the motor to accurately follow commands.
- Potential Damage to Electronics: Servo drives and other electronic components that control the motor may be damaged by incorrect polarity or reversed current flow.
For those working on servo systems for their CNC machines, a Yaskawa Single Axis Servo Driver can help mitigate risks associated with reversed wiring.
Reversing Servo Motor Signal Wires
In addition to power wiring, signal wires may also be inadvertently reversed. Servo motors typically use signals from a controller to determine their speed, position, and torque. Reversing the signal wires can lead to:
- Erratic Motor Behavior: The motor might rotate at unexpected speeds or move to incorrect positions.
- Feedback Errors: Encoders and other feedback devices will provide incorrect information to the controller, further compounding the issue.
- Faults and Alarms: Modern servo systems often come with safety features that trigger alarms when a fault is detected. Reversing wires will likely cause such alarms to activate, halting operations.
Example Table: Summary of Potential Effects
Component | Effect of Reversed Wiring |
---|---|
Power Terminals | Motor spins in opposite direction, overheating risks |
Signal Wires | Feedback errors, erratic behavior |
Control System | Fault alarms, potential damage |
For a detailed understanding of reversing control wiring and potential troubleshooting, refer to our guide on Panasonic servo systems.
Safely Reversing a Servo Motor
Step-by-Step Guidelines
If you need to reverse the rotation of a servo motor, you should take a few specific steps to ensure that the process is performed safely and without causing damage:
- Consult the Manual: Always start by consulting the motor’s user manual to determine the correct procedure for reversing rotation. Different models may have unique requirements.
- Switch Wires in the Controller: Instead of swapping the power terminals, often, changing the control settings in the servo drive or controller is the better approach. This way, the current still flows correctly through the motor.
- Check the Feedback System: After making any changes, confirm that the encoder or other feedback devices are functioning correctly and providing the expected signals to the controller.
- Monitor for Alarms: Pay attention to the servo drive. If an alarm is triggered, switch off power immediately to prevent damage and reassess the wiring.
Importance of Using the Correct Drive
The type of servo drive used with your motor can make a significant difference in how effectively you can reverse the motor’s direction. Servo drives from reliable brands like Yaskawa or Panasonic are typically equipped with robust control systems to make reversing simple and safe.
For projects involving multiple axes, the Yaskawa Dual Axis Servo Drive can provide enhanced control and safety.
Example: Incorrect and Correct Wiring Practices
The wiring for a typical servo motor consists of three main types of connections: power supply, signal wires, and feedback. The following provides a list of common mistakes and correct practices:
Common Mistakes:
- Swapping power supply connections without first de-energizing the system.
- Reversing signal wires while the control system is live.
- Ignoring feedback error alarms when first testing reversed wiring.
Correct Practices:
- Always power down the system before making changes to the wiring.
- Use manufacturer-approved connectors and tools to minimize the risk of incorrect connections.
- Test incrementally: After making changes, test motor rotation slowly to monitor for unusual noises or vibrations.
Can You Reverse Only the Feedback or Power?
Effects of Reversing Power Only
Reversing just the power supply lines of a servo motor will change its direction of rotation. For some applications, this might be acceptable. However, if feedback devices, such as encoders or resolvers, are not properly aligned, the motor will not know its actual position, leading to:
- Control Loss: The system will lose control over position, especially in closed-loop applications where precise control is needed.
- Overcurrent Faults: When there is an imbalance in the torque requirements due to incorrect positioning, overcurrent faults can occur, resulting in safety shutdowns.
Effects of Reversing Feedback Only
The feedback system, like an encoder, provides the motor controller with essential data regarding the motor’s current state. Reversing the connections for feedback will lead to inaccurate signals, resulting in issues like:
- Position Errors: The motor will move to incorrect locations.
- Calibration Failure: Most motors undergo a startup calibration sequence. Incorrect feedback wiring can prevent calibration, stopping the motor from running.
The Panasonic MINAS A5 400W Servo Motor comes with advanced feedback mechanisms that allow for straightforward troubleshooting in such situations.
Tips to Avoid Reversing Wiring
Labeling and Documentation
Proper labeling and maintaining updated documentation of the wiring setup can prevent accidental reversing of wires. Always label each wire with its specific function, such as power, ground, signal, etc.
- Use Colored Tags: Assign different colored tags to each type of connection to quickly distinguish them.
- Update Schematics: Keep schematics near the control panel to refer to during maintenance.
Training and Best Practices
Another effective method to avoid reversing wires is to ensure that all personnel involved in working with servo motors are adequately trained. They should understand:
- Servo Motor Basics: Basic servo motor functioning, including how feedback and power connections interact.
- Wiring Schematics: How to read and interpret wiring diagrams accurately.
- Safety Protocols: Always powering down and locking out/tagging out equipment before making any changes.
FAQs
1. Is it safe to reverse a servo motor by just swapping the power lines?
It depends on the servo motor and its design. Swapping power lines can cause reverse rotation, but it might damage the feedback system or drive if not properly done.
2. What are the signs of incorrect wiring in a servo motor?
Some common signs include unexpected rotation, inconsistent speed, vibration, and feedback errors. The control system may also trigger faults or alarms.
3. Can reversing the feedback wires alone change the motor’s behavior?
Yes, reversing feedback wires can lead to incorrect positioning and calibration failures, which ultimately causes erratic motor operation.
4. How can I safely test if my servo motor is wired correctly?
After making wiring adjustments, test with low speeds and no load. Watch for faults or unexpected behavior, and make incremental adjustments if needed.
5. Are there modern drives that prevent damage from reversed wiring?
Yes, modern drives such as those from Yaskawa and Panasonic often come with protections against reversed wiring, including alarms and safe shutoff mechanisms.
Conclusion
Wiring a servo motor in reverse can have significant consequences, affecting both performance and the health of the motor. While it is possible to reverse the direction of a servo motor, it must be done with caution. Proper training, consultation of the motor’s manual, and incremental testing are all crucial for safe operation. Additionally, using reliable components, such as high-quality servo drives, can help mitigate the risks involved.
For further guidance and to find a selection of quality servo motors and drives, visit the Servo Motor Store. Our extensive range and professional support will help you find the best solutions to keep your systems running smoothly.