Can AC Servo Motor Driver Work Without Hall Sensors?
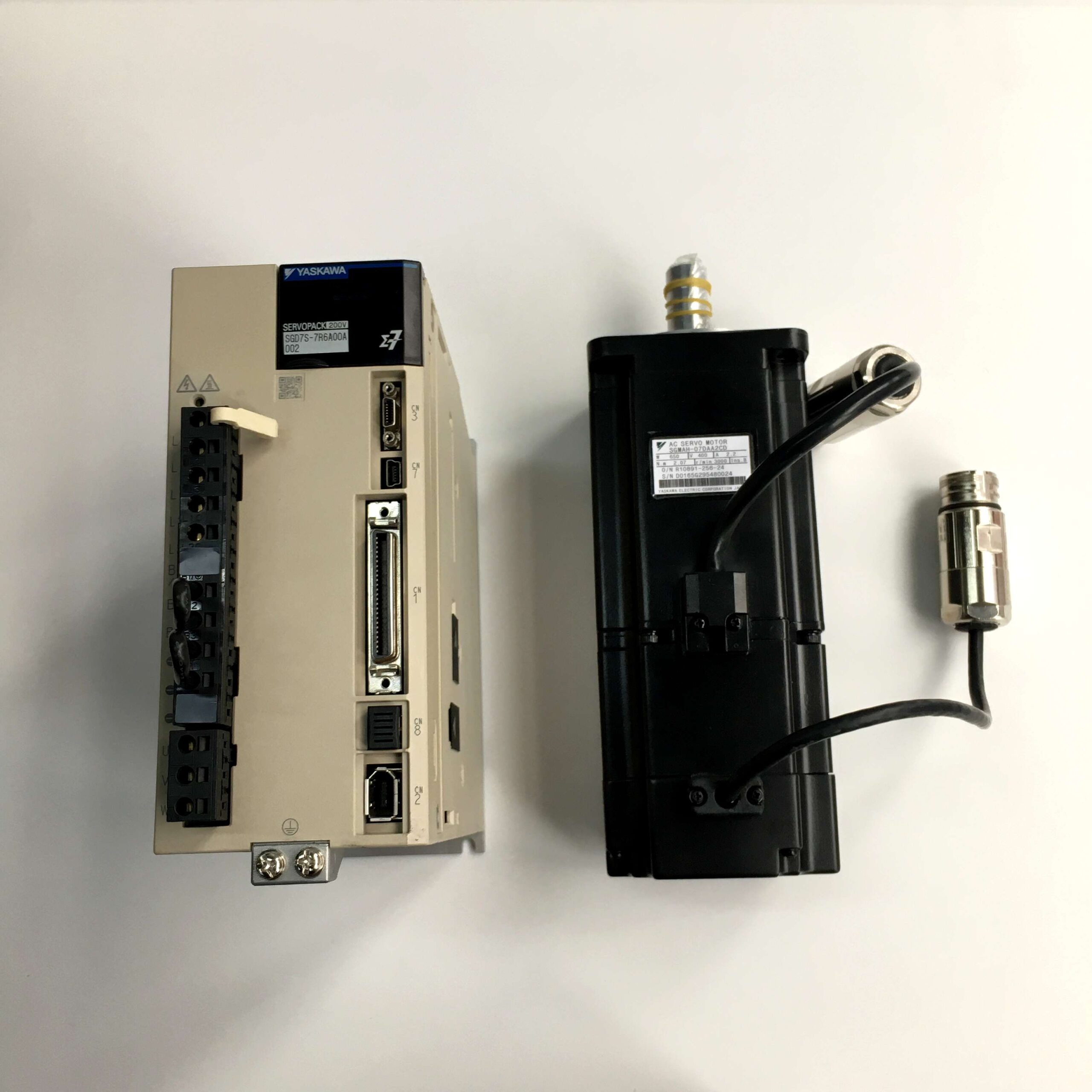
AC servo motors are pivotal in countless applications, providing the essential precision and control required in industries like robotics, CNC machining, and automated manufacturing. In many cases, hall sensors are integrated to ensure optimal performance. But, can an AC servo motor driver work without hall sensors? This comprehensive guide aims to explore this topic in depth, analyzing scenarios where hall sensors may or may not be necessary. We will cover the basics of servo motor functionality, discuss the role of hall sensors, and examine alternative control methods to help you make an informed decision.
Understanding Hall Sensors in AC Servo Motors
What Are Hall Sensors?
Hall sensors are magnetic sensors used to determine the position of the rotor in AC motors. By providing the motor controller with real-time data about the rotor’s position, they help achieve precise control over speed, torque, and direction. They detect changes in the magnetic field generated by the motor’s permanent magnets and send signals back to the motor controller.
Key Functions of Hall Sensors
- Position Sensing: Hall sensors detect the exact position of the rotor, which is critical for timing the motor’s electrical phases.
- Feedback Mechanism: They act as a feedback mechanism, allowing the servo driver to adjust voltage and current as needed for accurate motion control.
- Smooth Operation: Hall sensors help in achieving smoother operation by ensuring that phase commutation is always optimal.
For those looking for detailed specifications and uses of Panasonic Servo Motors, you may refer to our Panasonic Servo Motor MINAS A5 1KW Series.
Why Are Hall Sensors Important in Servo Systems?
Servo systems rely on precise positioning for various complex tasks. The accurate positioning of the rotor is vital in maintaining consistent and smooth operations, and hall sensors play a crucial role here by ensuring correct commutation. This feedback ensures synchronization between the motor’s magnetic field and its physical movement, preventing any lags or glitches that may otherwise occur.
Potential Downsides of Using Hall Sensors
While hall sensors offer a robust method for rotor position sensing, they come with certain drawbacks:
- Complexity: Adding hall sensors to a system increases the overall complexity, making it more challenging to troubleshoot.
- Cost: Including hall sensors raises both the production and maintenance cost of the motor.
This begs the question: is there a way to run an AC servo motor driver effectively without hall sensors?
How Servo Motors Work Without Hall Sensors
Sensorless Control: An Overview
Sensorless control is an alternative method that allows an AC servo motor to operate without hall sensors. In sensorless control, the motor controller uses back electromotive force (EMF) to infer the rotor position. This method is particularly useful in applications where reducing complexity and cost is a priority.
How Back EMF Works
Back EMF is the voltage generated by the movement of the rotor in the stator’s magnetic field. By monitoring back EMF, a servo driver can estimate rotor position and synchronize electrical commutation accordingly.
Advantages of Sensorless Control
- Cost-Efficiency: Eliminates the need for hall sensors, reducing overall cost.
- Simplified Design: Decreases system complexity, leading to easier maintenance and troubleshooting.
However, sensorless control may not be the best fit for applications where extremely precise positioning is necessary, as it tends to be less accurate compared to hall sensor feedback.
For high-quality Yaskawa servo drivers designed to work with sensorless control, check out Yaskawa SGD7S Servo Drivers.
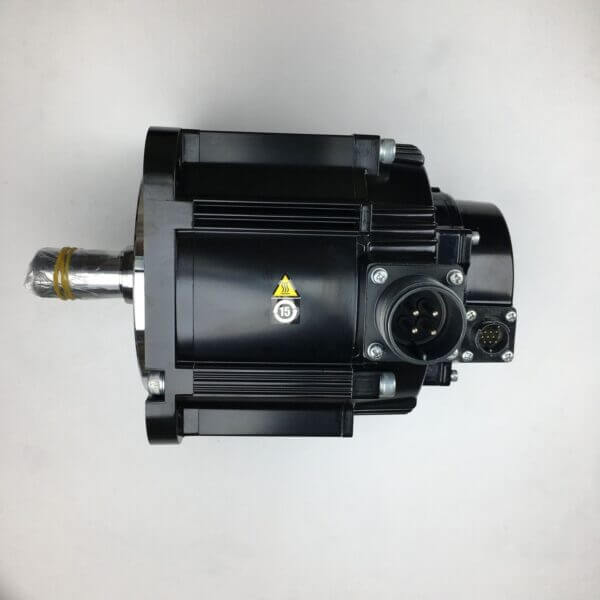
Applications Suitable for Sensorless Control
Sensorless control is typically used in applications where:
- Reduced Complexity is desired
- Lower Cost is essential
- Less Critical Precision is acceptable, such as fans, pumps, and other rotating machinery
In such cases, eliminating hall sensors provides a simplified design that is easier to implement and maintain.
Performance Comparison: Hall Sensors vs. Sensorless Control
Aspect | Hall Sensors | Sensorless Control |
---|---|---|
Precision | High accuracy with real-time data | Moderate, relies on estimation |
Cost | Expensive due to added components | More affordable, fewer parts |
Complexity | High, additional wiring and circuits | Simplified, fewer components |
Applicability | Precision-demanding applications | Non-critical or simple tasks |
The choice between using hall sensors or a sensorless setup depends primarily on your specific application needs, whether that means prioritizing precision or focusing on simplicity and cost-efficiency.
How To Run an AC Servo Motor Without Hall Sensors
Required Equipment
To operate an AC servo motor driver without hall sensors, you will need:
- Servo Driver with Sensorless Capability: Ensure that the driver can interpret back EMF for rotor positioning.
- Oscilloscope: Helpful for diagnosing issues and ensuring proper signal output during startup.
- Multimeter: To verify voltages and continuity in the system.
Step-by-Step Guide
- Connect the Servo Motor to the Driver: Ensure proper wiring between the motor and servo driver.
- Enable Sensorless Mode: Configure the driver settings to sensorless mode using the manufacturer’s manual.
- Run Calibration: Most sensorless systems will require an initial calibration to estimate motor constants and back EMF characteristics.
- Monitor Back EMF Signals: Using an oscilloscope, verify that the back EMF is being read properly by the controller.
For a reliable guide on configuring Panasonic servo drivers in sensorless mode, visit the Panasonic Servo Motor Configuration Guide【129†source】.
Advantages and Disadvantages of Running Without Hall Sensors
Advantages
- Cost Savings: Eliminates the cost associated with sensors and their maintenance.
- Simpler Design: Fewer components mean a simpler motor setup, which is easier to maintain.
- Less Susceptibility to Environmental Issues: Since no physical sensors are involved, problems related to sensor exposure to dust or moisture are minimized.
Disadvantages
- Reduced Accuracy: Sensorless control lacks the precision provided by hall sensors.
- Startup Challenges: Without initial position feedback, starting the motor accurately can be challenging, especially under load conditions.
- Limited Application: Not ideal for high-precision applications that require precise motion control, such as robotics and CNC machining.
When to Choose Sensorless Control
Sensorless control should be chosen in applications where cost efficiency and simplicity are more critical than extreme accuracy. For example, in HVAC systems, industrial pumps, or conveyor belts, sensorless AC servo motors are an excellent fit. However, for robotic arms or CNC machines, which need exact positioning, hall sensors or other feedback mechanisms remain irreplaceable.
Conclusion: Can You Run an AC Servo Motor Without Hall Sensors?
The answer is yes, AC servo motor drivers can work without hall sensors by relying on sensorless control methods such as back EMF monitoring. While this approach has its benefits, including reduced cost and simplified design, it does come with the trade-offs of reduced accuracy and a more challenging startup phase.
In high-precision applications where exact positioning is crucial, hall sensors are indispensable. However, for simpler applications where budget constraints are a priority, sensorless control is a viable alternative that still allows for effective motor operation. The key lies in evaluating your application’s specific needs and determining which control method offers the best balance between cost, complexity, and performance.
If you’re looking for high-quality AC servo motors or servo drives that can meet both sensor-based and sensorless requirements, visit the Servo Motor Store. Our wide range of products is designed to cater to all your automation and control needs.
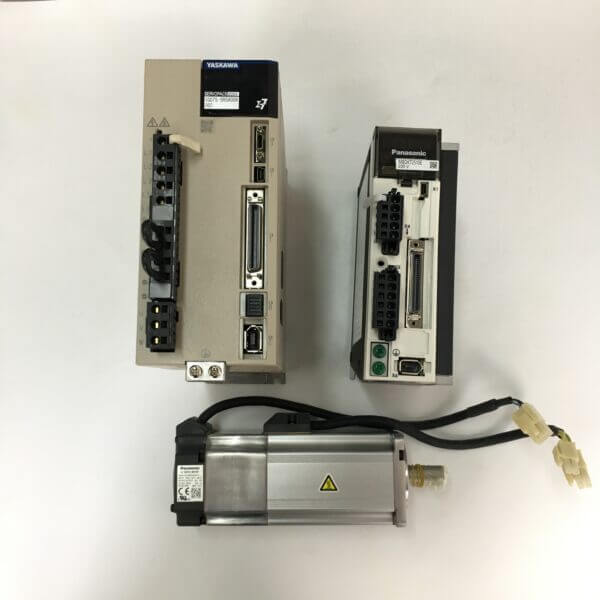
Frequently Asked Questions
1. Can I use an AC servo motor without any feedback mechanism?
It is possible to use an AC servo motor without feedback, but the performance, such as precise speed and position control, may be compromised. Feedback mechanisms, including hall sensors or encoders, are typically used for better control.
2. What is the role of a hall sensor in a servo motor?
Hall sensors provide critical feedback on the rotor’s position, enabling accurate commutation and control over the motor’s movement. This feedback ensures the motor runs smoothly without jerky or erratic movements.
3. Are there alternatives to hall sensors?
Yes, alternatives like incremental encoders or absolute encoders can also provide rotor position feedback. For a less costly approach, sensorless control using back EMF is an option, though with some trade-offs in accuracy.
4. Is sensorless control reliable for all applications?
Sensorless control is reliable for applications that do not require very high precision. It works well in simple systems like fans and pumps, but it may not be suitable for high-precision applications like CNC machinery.
5. How do I choose between hall sensors and sensorless control?
Choose hall sensors if your application requires high precision and consistent torque at low speeds. Opt for sensorless control if your main priorities are reducing complexity and lowering costs, especially if your application can tolerate lower precision.