Can DC Motors Take More Load Than Servos?
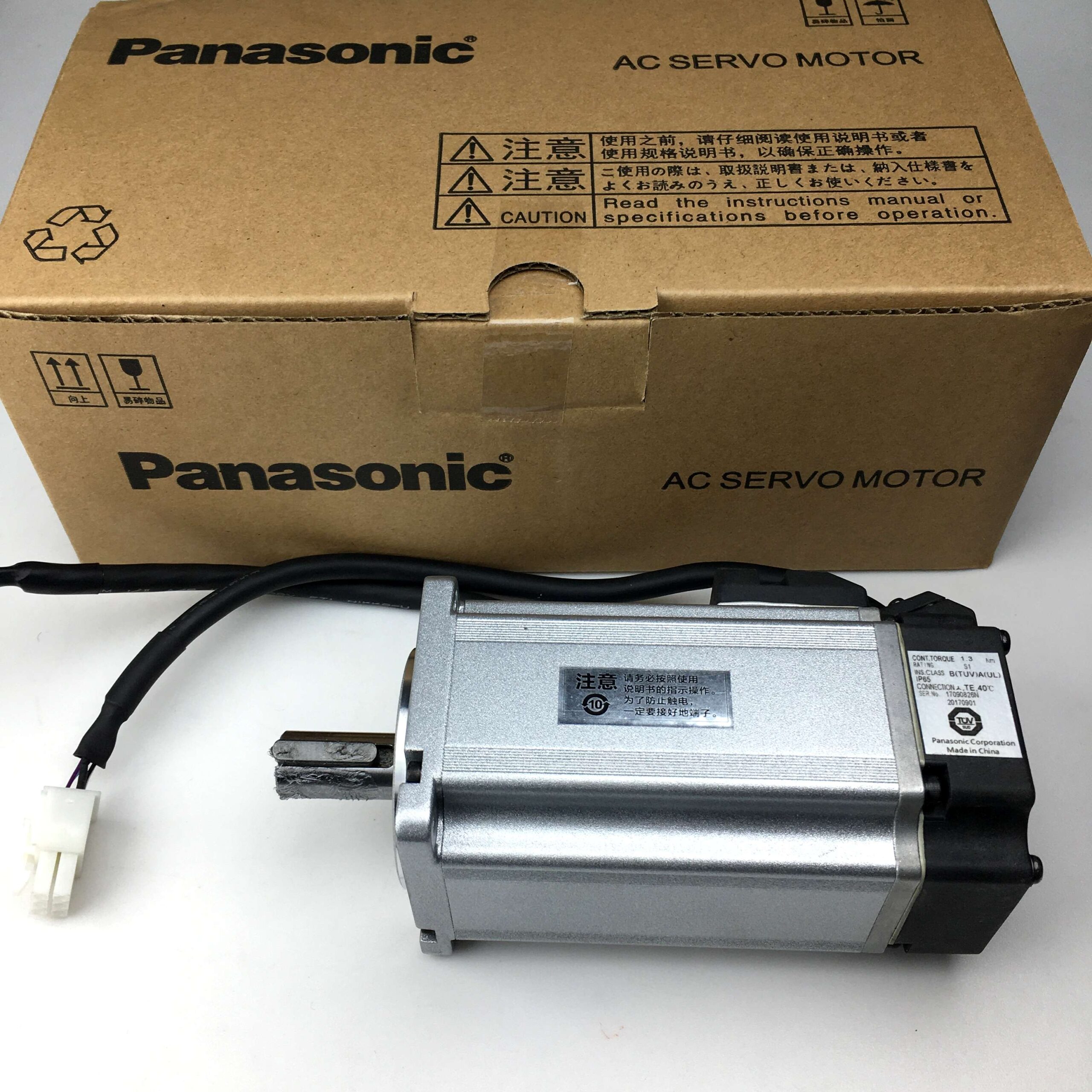
When it comes to selecting the right motor for your application, DC motors and servo motors are two popular options often considered. Understanding their load capacity is critical, as it directly affects how effectively each motor performs under specific conditions. The question at hand is: Can DC motors take more load than servos? This article will delve into the details of these two types of motors, exploring their strengths, weaknesses, and practical applications to help you determine which motor best suits your needs.
What Are DC Motors and Servo Motors?
Before we can adequately assess whether DC motors can handle more load than servo motors, it’s essential to understand the basics of these two types of motors and how they function.
DC Motors: Power and Simplicity
DC motors are among the most widely used types of motors, thanks to their simple design and versatility. They convert direct electrical current (DC) into mechanical energy by generating a magnetic field that produces torque, causing the rotor to rotate. This simple yet powerful design allows DC motors to be employed in a variety of applications, from small devices to industrial machinery.
- Types of DC Motors:
- Brushed DC motors: These motors use brushes to transfer electricity, which makes them cost-effective and easy to control. However, they tend to wear out over time and require regular maintenance.
- Brushless DC motors (BLDC): These are more efficient and have a longer lifespan compared to brushed motors. They are more complex in their design and require electronic controllers but provide smoother operation.
DC motors are best suited for applications that require continuous rotation and high torque. Their simplicity and low cost make them a popular choice for automotive systems, fans, and conveyor belts.
Servo Motors: Control and Precision
Servo motors are more sophisticated than DC motors and are designed for high-precision control. A servo motor is a rotary actuator that provides precise control of angular position, speed, and acceleration. Unlike DC motors, servo motors incorporate feedback mechanisms that adjust the output to maintain accurate movement.
- Types of Servo Motors:
- AC Servo Motors: These are powered by alternating current and are generally used in high-torque, high-precision applications.
- DC Servo Motors: These operate on direct current and are more common in lower power or simpler precision applications.
Servo motors are commonly used in robotics, CNC machinery, and automation systems, where precise positioning and speed control are critical.
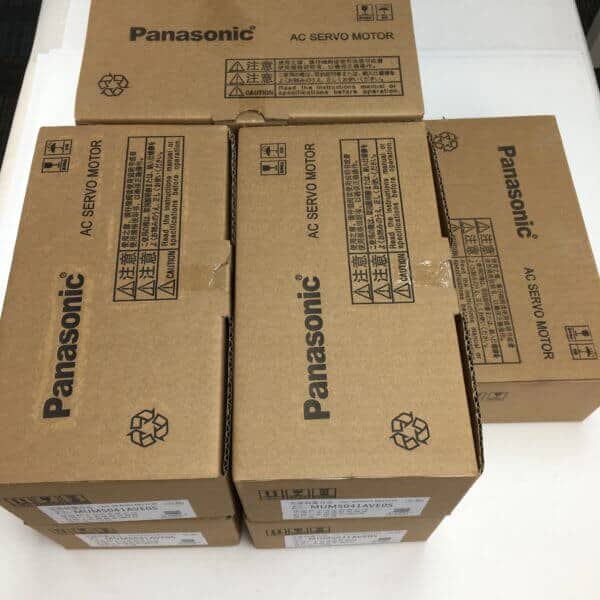
[Original Panasonic Servo Motor MINAS A5 1KW MDME102GCH/MDME102GCHM. More details can be found here.]
Comparing Load Handling Capabilities
Understanding Torque and Load
The load handling capability of a motor primarily depends on its ability to produce torque, which is the rotational force needed to move a load. Both DC and servo motors can generate substantial torque, but their ability to handle loads differs due to their design characteristics.
- Torque Output in DC Motors: DC motors, especially those with appropriate gearing, can generate high torque suitable for moving large loads. They can be configured with gear systems that increase their ability to handle heavy mechanical loads.
- Torque in Servo Motors: Servo motors, though generally smaller in size, are engineered to produce a high amount of torque relative to their physical dimensions. Their integrated gear reduction systems allow them to handle load efficiently while maintaining precision.
Load Control Mechanisms
One of the key differences between DC motors and servo motors lies in how they handle loads under varying conditions.
- DC Motors: The load-handling capacity of DC motors is relatively straightforward, influenced by input voltage and current. They are ideal for applications that require consistent high loads without the need for high precision.
- Servo Motors: Servo motors employ feedback systems, such as encoders or potentiometers, to manage load with precision. This allows for the motor to adjust its output dynamically to accommodate changes in load, ensuring accuracy and preventing overload.
Real-World Application Example
Consider an industrial conveyor belt versus a robotic arm. A conveyor belt that moves heavy objects over long periods benefits from a DC motor because it can deliver continuous high torque without intricate positioning needs. Conversely, a robotic arm that requires precision to pick and place objects benefits more from a servo motor due to its feedback mechanism that enables precise movement.
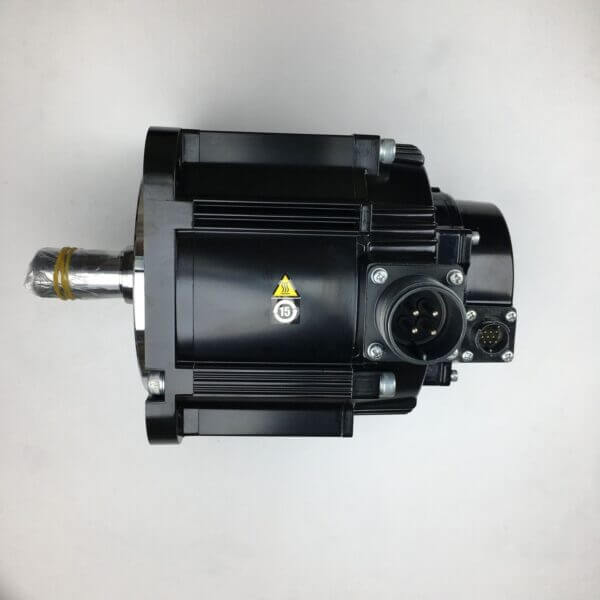
[Original Yaskawa Single Axis Servo Driver SGD7S-120A00A. Learn more here.]
Efficiency and Energy Consumption
DC Motors: Raw Power with Variable Efficiency
DC motors are known for their efficiency in converting electrical energy into mechanical energy, especially when operating at moderate to high speeds. Brushed DC motors have higher energy losses due to friction from brushes, whereas brushless DC motors (BLDC) are more efficient and have fewer mechanical parts that can wear out.
However, DC motors may experience efficiency drops when load conditions vary significantly, mainly due to thermal losses and friction. This makes them better suited for applications where load remains constant.
Servo Motors: Energy-Efficient with Dynamic Load Management
Servo motors are specifically designed to be energy-efficient, especially in applications that require precision and control. The feedback mechanism ensures that only the energy necessary to meet the desired movement or position is used, thus optimizing efficiency.
In scenarios like automated assembly lines, servo motors save energy by maintaining precision control over repetitive tasks, preventing unnecessary energy expenditure. For this reason, while DC motors may support larger static loads, servo motors excel in energy management when dynamic load handling and precise control are involved.
High Torque vs Precision: The Trade-Off
DC Motors for High Torque at Lower Costs
If your application requires high torque at a lower cost and the load is largely static, DC motors are often the preferred choice. You can easily modify their torque output by changing the electrical input or using gear systems.
- High Torque Applications:
- Winches
- Fans
- Electric Vehicles
The affordability of DC motors, combined with their simple construction, makes them ideal for many heavy-duty applications that do not require precise positioning or speed control.
Servo Motors for Precision Load Handling
Servo motors, in contrast, are the go-to choice when precision matters. These motors come equipped with control systems that allow for consistent load handling with pinpoint accuracy. The feedback systems used by servo motors enable them to perform tasks with minimal deviation, making them essential for applications like robotic welding and automated assembly.
The integrated controller and encoder ensure that every movement is precise, even when load conditions change, which is crucial for operations where accuracy is paramount.
Cost and Maintenance Considerations
Cost Factors
One of the primary differences between DC motors and servo motors lies in their cost.
- DC Motors are generally cheaper due to their simple construction. They do not have complex control mechanisms or integrated electronics, which significantly reduces production costs.
- Servo Motors, by contrast, are typically more expensive because of their sophisticated design, including feedback mechanisms and control units that enable precision control.
Maintenance Requirements
- DC Motors:
- Brushed DC Motors need regular maintenance due to brush wear. Over time, these brushes wear down and must be replaced.
- Brushless DC Motors require less mechanical maintenance since they do not use brushes, but they may still need occasional electronic upkeep.
- Servo Motors: The maintenance requirements of servo motors are mainly related to their electronic components. Because of their reliance on digital controllers, any issues with calibration or control systems can be complex to troubleshoot.
Despite these higher maintenance demands, servo motors generally last longer in high-precision environments since they do not undergo the same physical wear as brushed DC motors.
Energy Management: A Key Factor in Load Handling
Thermal Management in DC Motors
DC motors can handle significant loads but tend to generate substantial heat when operating under high load conditions. Thermal management is crucial to prevent overheating, which can lead to decreased efficiency and potential failure.
To keep the motors cool, cooling fans or heat sinks are often added. However, in environments where load conditions fluctuate significantly, maintaining optimal temperature can be a challenge.
Servo Motors and Effective Cooling
Servo motors, on the other hand, are designed with efficiency in mind, including thermal management features. Since servo motors only use as much power as required for the task, they tend to generate less heat. Additionally, the feedback control ensures that the motor doesn’t overwork itself, which inherently reduces the amount of heat produced.
This makes servo motors ideal for applications that require variable loads and consistent performance without the risk of overheating.
Key Differences in Application Scenarios
To effectively determine whether a DC motor can take more load than a servo motor, it’s important to define what we mean by “load.”
- If we refer to sheer mechanical load capacity, DC motors can indeed be designed to handle larger loads by using appropriate gearing and increasing voltage input.
- If, however, we refer to the ability to handle loads with high accuracy, dynamic response, and varying conditions, then servo motors are the superior choice.
Motor Type | Load Handling | Cost | Precision | Maintenance |
---|---|---|---|---|
DC Motor | High, cost-efficient | Lower initial cost | Lower precision | Moderate |
Servo Motor | High with precision | Higher initial cost | Very high | Lower mechanical, more electronic |
FAQs
1. Can DC motors handle variable loads efficiently?
DC motors can handle variable loads, but they lack the feedback mechanisms present in servo motors. Thus, while a DC motor can accommodate changes in load, it won’t adapt as precisely as a servo motor would. This can affect efficiency and control in dynamic applications.
2. What motor type should I use for a high-precision application?
For applications that require high precision, such as robotic control or CNC machinery, servo motors are the ideal choice. The integrated feedback and control systems ensure precise movements and adjustments.
3. Are servo motors more energy-efficient than DC motors?
Yes, servo motors tend to be more energy-efficient compared to DC motors, especially in dynamic applications. Their efficiency is largely due to their feedback mechanisms, which ensure that they only use the necessary amount of energy for each movement.
4. Which motor is cheaper to maintain?
Brushed DC motors are generally cheaper to maintain in the short term due to their simple construction. However, servo motors might offer lower long-term costs in precision applications due to reduced wear and fewer moving mechanical parts.
5. Do servo motors offer better load control than DC motors?
Yes, servo motors provide superior load control thanks to their integrated feedback mechanisms. This allows them to maintain precise positioning, speed, and torque under various load conditions.
Conclusion
The question of whether DC motors can take more load than servo motors is nuanced. While DC motors can indeed handle substantial loads, especially in applications that do not require precision, servo motors excel in handling loads with high accuracy and dynamic response. The decision comes down to the requirements of your specific application—if you need high torque at a low cost with limited precision, DC motors are a suitable choice. On the other hand, if precision, control, and dynamic load handling are crucial, then servo motors are unmatched.