Can I Replace Plastic Gears in a Servo Motor?
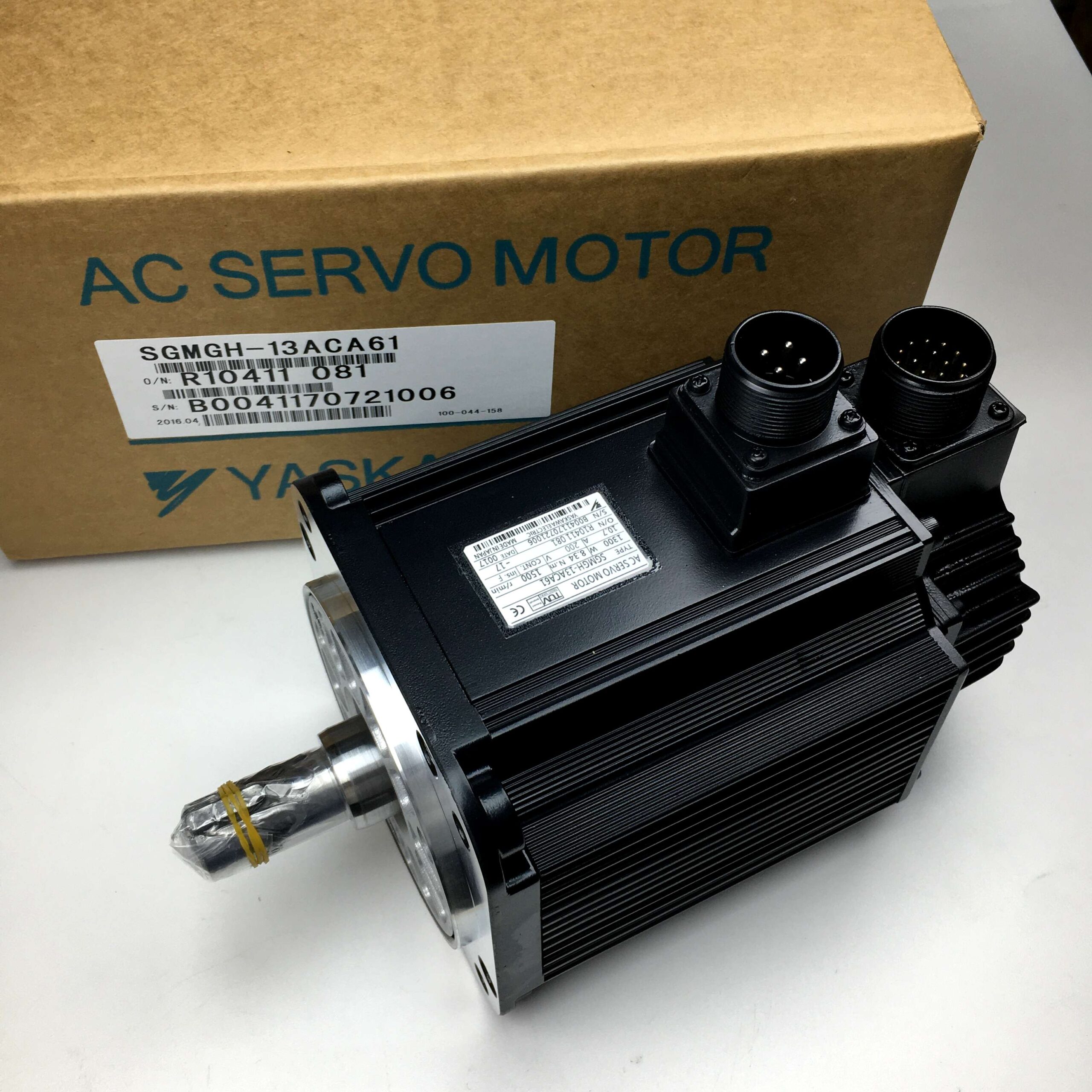
Servo motors are essential components in many types of machinery, including robotics, CNC machines, and other automation systems. While they are reliable, the gears inside them are subject to wear and tear, especially if they are made of plastic. This leads to a common question: Can plastic gears in a servo motor be replaced? This comprehensive guide will explore the possibility of replacing plastic gears, the benefits and challenges of doing so, and what alternatives might be available.
Understanding Servo Motor Gears
The gears inside a servo motor serve a crucial purpose: they help control speed and torque, enabling precise movements. In many hobby-grade or cost-effective servo motors, these gears are often made from plastic. Plastic gears are lightweight and inexpensive, making them suitable for light-duty applications. However, they may not withstand high stress or heavy loads as effectively as their metal counterparts.
Types of Gears in Servo Motors
Servo motors can contain different types of gears, including:
- Plastic Gears: Common in hobby and small-scale servos. They are cost-effective but wear down quickly under high load conditions.
- Metal Gears: Found in industrial and heavy-duty servo motors. They are more durable and capable of handling larger loads.
- Composite Gears: A combination of plastic and metal gears. These offer a balance between cost and performance.
Why Do Plastic Gears Fail?
Plastic gears in servo motors can fail for several reasons, including:
- Overloading: Excessive torque can cause the teeth of plastic gears to strip or break.
- Wear and Tear: Continuous use leads to gradual wear, especially in high-speed or heavy-load applications.
- Heat: Plastic gears can become deformed when exposed to excessive heat, leading to inefficiency and failure.
Replacing Plastic Gears with Metal Gears
One of the most common fixes for a servo motor with worn-out plastic gears is replacing them with metal gears. This upgrade can significantly enhance the motor’s durability and load-handling capability. However, there are important considerations to take into account.
Benefits of Replacing Plastic Gears with Metal
- Increased Strength: Metal gears are much stronger than plastic gears, allowing the servo motor to handle higher torque and more challenging tasks.
- Longevity: Metal gears tend to last longer, especially in environments with continuous or heavy use.
- Reduced Maintenance: With metal gears, the frequency of maintenance and replacements is reduced, saving time and cost.
Note: If you plan to replace plastic gears with metal gears, ensure that the motor casing and other components can handle the increased weight and potential wear caused by metal.
Challenges of Metal Gear Replacement
- Weight: Metal gears are heavier than plastic ones, which might affect the motor’s performance, especially in applications that require quick, lightweight movement.
- Compatibility: Not all servo motors are designed for gear swapping. The replacement gears must be compatible with the motor’s housing and shaft.
- Cost: Metal gears are more expensive compared to plastic, which might be a consideration depending on the scale of the project.
Step-by-Step Guide to Replacing Plastic Gears
If you’ve decided to replace plastic gears in your servo motor, follow these steps to ensure a successful replacement:
1. Gather Necessary Tools
To begin, gather the following tools and materials:
- Replacement metal gears
- Screwdrivers (appropriate for the servo screws)
- Lubricant (for smooth operation of the new gears)
- Cleaning cloths
2. Disassemble the Servo Motor
Carefully open the servo motor casing by removing the screws. Be cautious of the electronic components, such as the potentiometer, which might be delicate.
3. Remove and Inspect the Gears
Once the motor is open, remove the plastic gears. Inspect the gear train for signs of wear, such as stripped or broken teeth. If other components like bearings are worn out, replace them as well.
4. Install the New Gears
Install the metal gears, ensuring they mesh properly and fit snugly in the housing. Proper alignment is crucial for smooth and noise-free operation.
5. Lubricate the Gears
Apply a suitable gear lubricant to the metal gears. Lubrication reduces friction and prolongs the life of the gears.
6. Reassemble the Motor
Carefully reassemble the motor, ensuring that all parts are securely in place. Make sure the casing is tightly screwed to prevent dust or particles from entering.
Are Metal Gears Always the Best Choice?
While metal gears offer significant advantages, they might not always be the best choice for every application. Consider these factors:
- Application Requirements: For lightweight or low-torque applications, plastic gears might suffice and even offer advantages such as quieter operation.
- Budget: For hobbyists or projects with limited budgets, replacing plastic gears with metal may not be cost-effective.
- Compatibility: Some servo motors are designed specifically for plastic gears, and switching to metal might require additional modifications that are impractical.
For servo motors with integrated electronics, such as the Panasonic Servo Motor MINAS A5 1KW, switching gears might not be advisable unless you’re certain of compatibility.
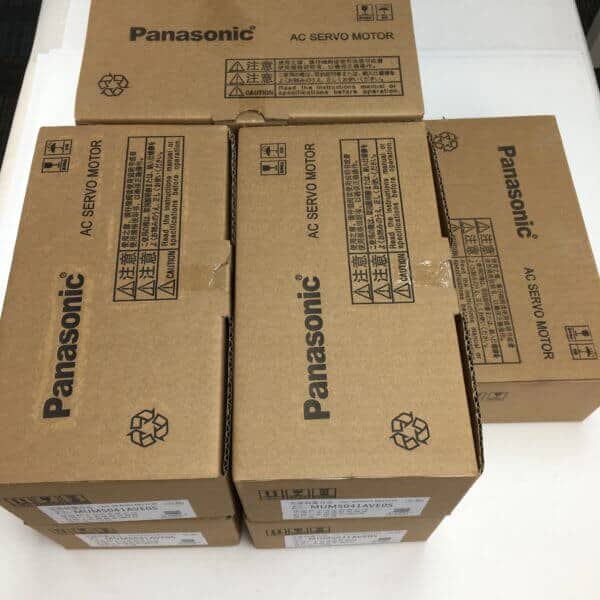
Alternatives to Replacing Plastic Gears
If replacing plastic gears isn’t the ideal solution, there are a few other options to consider:
1. Reinforcing Plastic Gears
Some plastic gears can be reinforced with metal inserts or coated to provide extra durability without fully switching to metal. This option can provide some benefits of metal gears while retaining the advantages of plastic, such as lighter weight and reduced noise.
2. Upgrading to a Servo with Metal Gears
If the servo motor frequently fails due to gear issues, consider upgrading to a new servo with factory-installed metal gears. This could be more cost-effective in the long run and would eliminate compatibility concerns.
You can browse our selection of servo motors with metal gears for a reliable upgrade option.
3. Using Composite Gears
Composite gears, made from a combination of plastic and metal, offer a balance between the durability of metal and the lightweight benefits of plastic. These gears are ideal for mid-range applications where neither plastic nor metal is perfectly suitable.
Preventing Gear Failure in Servo Motors
Whether you choose plastic, metal, or composite gears, preventive measures can help extend the life of your servo motor gears:
1. Avoid Overloading
One of the primary reasons gears fail is excessive torque. Make sure that your application is within the torque rating of the servo motor.
2. Regular Maintenance
Conduct regular maintenance checks. Lubricate the gears periodically and look for signs of wear to address issues before they lead to failure.
3. Proper Application
Ensure that you are using the correct type of servo motor for the application. For industrial tasks that require high torque, always opt for servos with metal gears.
Conclusion
Replacing plastic gears in a servo motor with metal gears can be an effective way to extend the motor’s lifespan and improve its performance under heavy load. However, it’s crucial to consider the weight, cost, and compatibility factors before proceeding. Metal gears are not always the best choice for every application, especially when lightweight and quiet operation is a priority.
If you’re looking for a reliable servo motor or need parts for your next upgrade, explore our Servo Motor Store for a variety of options, including metal-geared models and replacement parts. Remember that regular maintenance and choosing the appropriate motor for your needs are key to avoiding unnecessary gear failure.