Can I Reset the Limits on a Servo Motor?
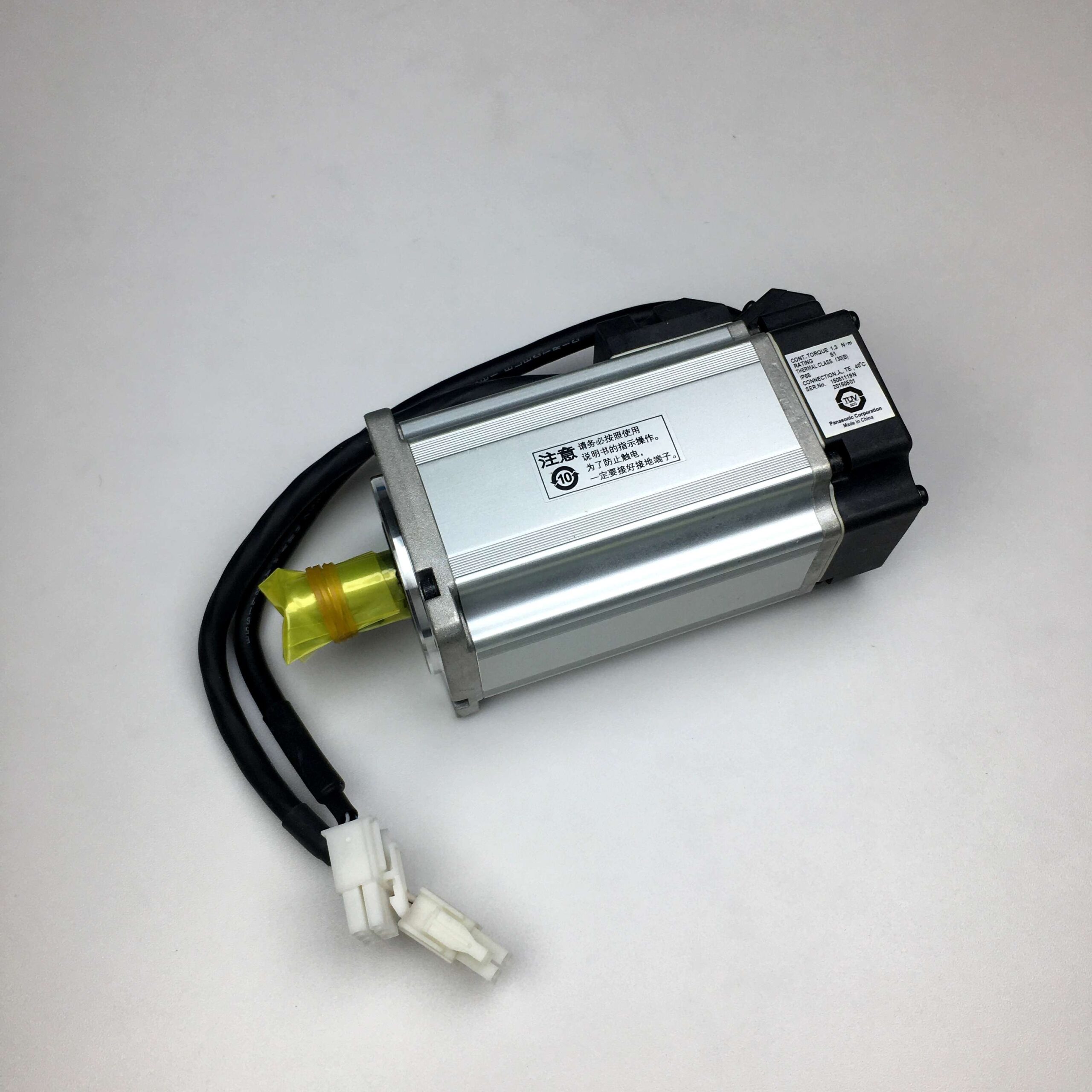
Servo motors are key components in many industrial and automated systems. The importance of precision in servo motor control cannot be overstated, as it directly affects the efficiency and accuracy of various machines. In this article, we explore whether it is possible to reset the limits on a servo motor, and if so, how this process can be carried out. We will also cover situations where limit resets are necessary, the procedures involved, and how to maintain your servo motor for optimal performance.
Understanding Servo Motor Limits
What Are Servo Motor Limits?
Servo motor limits refer to the maximum and minimum boundaries of movement that a servo motor can operate within. These limits are critical for preventing the motor from moving beyond its intended range, thus protecting both the motor and the connected mechanical components from damage. There are generally two types of limits:
- Software Limits: These are limits set through the servo drive or control software. They define how far the motor can move and are easily adjustable.
- Hardware Limits: Physical devices, such as limit switches, are used to stop the motor if it reaches a certain point, ensuring it does not exceed its physical boundaries.
In many cases, resetting or reprogramming these limits may be necessary to accommodate new applications, calibrate the system, or fix errors caused by unexpected events.
Why Are Limits Important?
- Protecting Equipment: Limits are vital for protecting both the servo motor and the attached mechanical system.
- Safety: They prevent accidents, especially in large systems involving heavy loads or high speed.
- Precision: Limits ensure that a servo motor accurately returns to predefined positions without overshooting, which is essential in tasks like CNC routing or robotic arm control.
“Servo motor limits are like guardrails that help ensure both safety and precision in industrial applications.”
When Should You Reset Servo Motor Limits?
There are specific situations where resetting servo motor limits becomes necessary:
- Reprogramming for a New Task: If the servo motor is being repurposed for a different function, the original limits may not be suitable.
- Calibration: Over time, mechanical wear or external forces might lead to slight inaccuracies. Resetting the limits can help recalibrate the system.
- Error Correction: If the motor has reached an unintended position due to a malfunction, the limits might need to be reset to correct the error.
- Controller Replacement: When upgrading or replacing a servo drive, the new controller might require recalibration, including adjusting the limits.
Tools Needed to Reset Servo Motor Limits
Before attempting to reset servo motor limits, gather the following tools and materials:
- Servo Controller or Drive Software: Most modern systems allow you to set limits through control software.
- Programming Cable: To connect the servo drive to a computer or other programming device.
- Manufacturer Manual: Each motor might have different settings and procedures, so refer to the manual.
- Safety Gear: Protective gloves and goggles if working with live machinery.
Step-by-Step Guide to Resetting Servo Motor Limits
1. Safety First
- Power Down the System: Make sure the entire system is powered off to avoid any accidental movements.
- Disengage Mechanical Load: If possible, disconnect any mechanical components linked to the motor to prevent unintended movement.
2. Connect to the Servo Controller
Most servo motors are connected to a controller that allows you to set or reset software limits. Use the programming cable to connect the controller to your computer or handheld programmer.
- Step 1: Plug the programming cable into the servo drive.
- Step 2: Launch the software provided by the manufacturer, such as Yaskawa’s SigmaWin+ or Panasonic’s MINAS software.
3. Access the Limit Settings
- Navigate to the position settings menu. The software interface will typically provide a graphical representation of the motor’s operational range.
- Locate the current limit settings for both the positive and negative directions.
4. Adjust the Limits
- Enter new values for the maximum and minimum travel limits.
- It’s advisable to move the motor manually to the desired endpoint, and then use the software to set the limit at this position.
Tip: Always move the motor to its extreme intended positions manually to confirm that the limits you are setting will not cause collisions or damage to the system.
5. Save and Test the New Settings
- Save the Settings: Confirm that the new limit settings are saved to the controller memory.
- Testing: Run a controlled test to verify the new limits. Ensure the motor stops as expected when reaching the set boundaries.
Step | Description |
---|---|
Power Down | Turn off the system before starting. |
Connect | Use programming cable to link the servo drive. |
Adjust Limits | Set new min and max limits in the software. |
Save & Test | Save settings and test motor movement. |
6. Update the Mechanical Limits (If Required)
If your system also uses mechanical limit switches, you might need to reposition these to match the new software limits. These switches act as a fail-safe to protect against software or hardware malfunctions.
Common Issues During Limit Reset
1. Communication Problems
Sometimes, the connection between the servo controller and the computer might not work as expected.
- Solution: Make sure the programming cable is properly connected, and that the correct driver software is installed.
2. Software Compatibility
Different motors and drives require different software versions.
- Solution: Ensure you are using the correct software for your specific servo drive. For example, the Panasonic Servo Motor MINAS A5 has specific software requirements.
3. Motor Movement During Setup
If the motor unexpectedly moves during the setup process, it could indicate a control issue.
- Solution: Always have an emergency stop button nearby and disconnect any mechanical load before adjusting settings.
Image Alt: Panasonic Servo Motor MINAS A5 2kW used for precision automation
Frequently Asked Questions
1. Can I reset the servo motor limits without specialized software?
In most cases, you need specialized software to reset servo motor limits effectively. However, some servo drives come with onboard control panels that allow limited manual adjustments.
2. What happens if my servo motor exceeds the set limits?
Exceeding set limits can lead to mechanical damage or motor burnout. Software limits and physical limit switches are essential for preventing such occurrences.
3. How often should servo motor limits be checked or reset?
Regular maintenance schedules should include checking the servo motor limits, particularly after mechanical changes or controller updates. Ideally, check every 6 to 12 months.
4. Are software or hardware limits better for servo motor protection?
Both are essential. Software limits are more versatile and adjustable, while hardware limits provide a physical fail-safe that ensures safety regardless of software errors.
Conclusion
Resetting the limits on a servo motor is a crucial procedure that helps maintain the safety, accuracy, and reliability of automated systems. Whether it’s to accommodate new requirements, recalibrate after wear and tear, or to fix issues caused by accidental misalignment, resetting servo motor limits should be done with precision and care. Utilizing the appropriate software, following correct procedures, and making use of both software and hardware limits will ensure that your servo motor functions efficiently within its intended boundaries.
For more information on servo motors and their components, visit our Servo Motor Store, where you can explore a range of high-quality products including Panasonic Servo Motor MINAS A5 2kW and Yaskawa Servo Drivers.