Can Servo Motors Take in AC Signals?
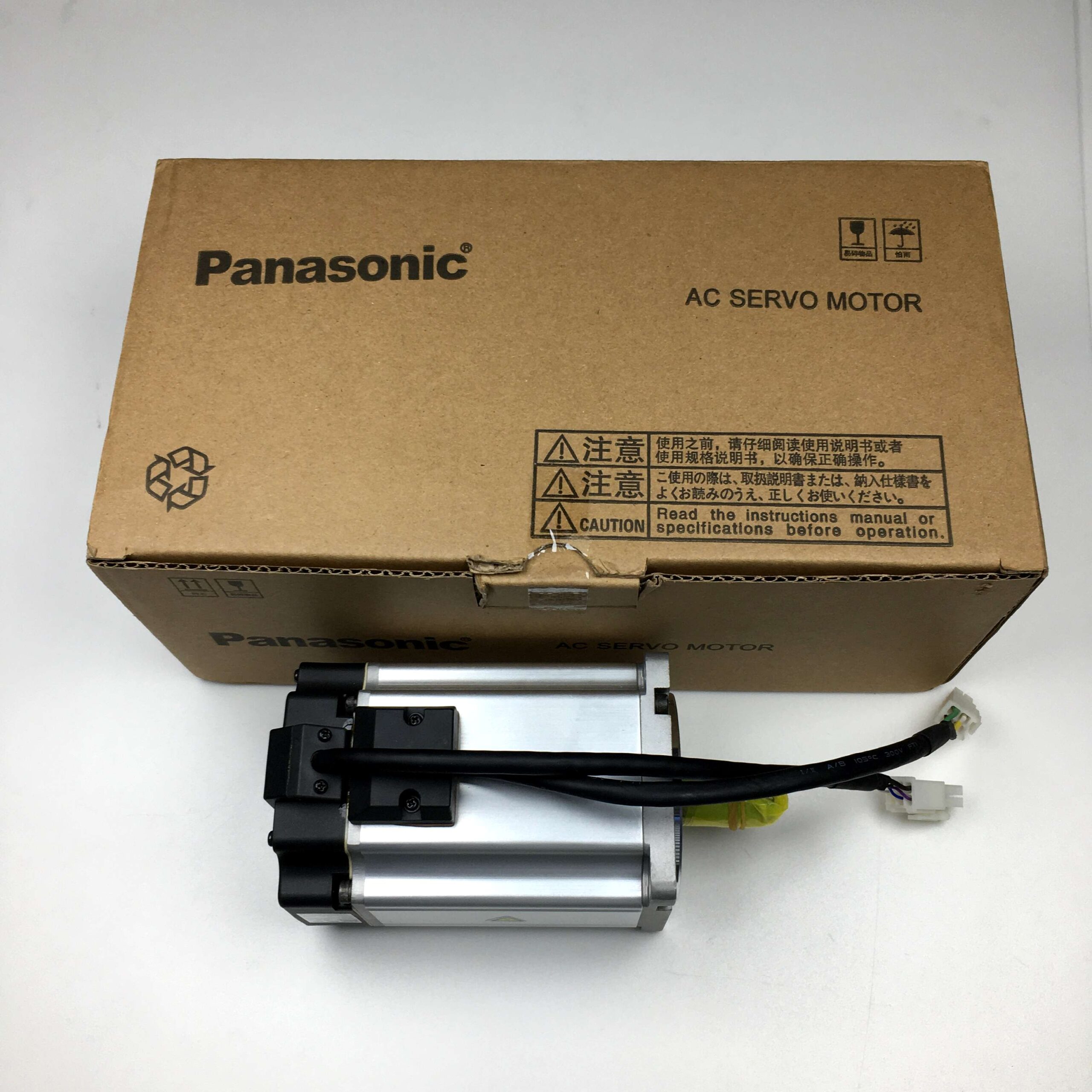
Servo motors are widely used in both industrial and commercial applications where precise movement is required. One key question often arises: Can servo motors take in AC signals? To fully understand the nature of servo motors and whether they are capable of accepting AC signals, we need to explore how different types of servo motors work, their control mechanisms, and the role of AC and DC signals in their operations. This article will guide you through everything you need to know, providing comprehensive insight into the capability of servo motors to accept AC signals.
Understanding AC Signals
AC (Alternating Current) is an electric current in which the flow of electric charge periodically reverses direction. AC is the standard form of electricity supplied by power companies and is primarily used in most household and industrial equipment. The waveform of AC power is typically sinusoidal, and it allows for efficient long-distance energy transmission.
AC signals play a major role in various motor applications, including servo motors. But does this mean that servo motors can directly accept AC signals?
Types of Servo Motors and Their Compatibility with AC Signals
1. AC Servo Motors
AC servo motors are specifically designed to operate with alternating current. These types of servo motors are ideal for applications requiring high speed, accuracy, and consistent torque. The components of an AC servo motor include a rotor, a stator, and an encoder. Unlike traditional AC motors, AC servo motors have an integrated control system that allows precise movement, making them ideal for robotics and machine tools.
How AC Servo Motors Handle AC Signals
In AC servo motors, the AC signal is used to power the stator, generating a rotating magnetic field that interacts with the rotor to produce torque. The AC servo motor’s driver, also known as the servo drive, converts the control signals into the appropriate phase and frequency required by the motor, ensuring that the motor performs precisely as commanded.
AC servo motors are specifically designed to use alternating current to achieve accurate movement, making them highly suitable for applications demanding high torque and speed control.
Advantages of AC Servo Motors
- Higher Efficiency: Due to the alternating current’s ability to produce a rotating magnetic field, AC servo motors tend to have higher efficiency.
- Durability: AC servo motors are known for their robust construction and durability, especially in industrial environments.
- Speed Control: With the help of a servo drive, AC servo motors can achieve precise speed and position control, even under changing load conditions.
Feature | AC Servo Motor |
---|---|
Power Type | Alternating Current (AC) |
Efficiency | High |
Applications | Industrial automation, robotics, CNC |
2. DC Servo Motors
Unlike AC servo motors, DC servo motors operate using direct current. The internal structure and operational dynamics differ significantly from their AC counterparts. DC motors usually have brushes and commutators that help in transferring electrical current, which inherently limits their speed range compared to AC motors.
Can DC Servo Motors Accept AC Signals?
No, DC servo motors cannot directly accept AC signals. These motors are specifically designed to use direct current, and applying AC directly can lead to damage. Instead, if the motor driver receives AC input, it will convert the alternating current into DC internally before it reaches the motor.
Tip: If you are using a DC servo motor and need to connect it to an AC power source, always use a rectifier or a motor drive that is capable of converting AC to DC.
3. Brushless Servo Motors (BLDC)
Brushless servo motors, also known as BLDC motors, use electronic commutation instead of mechanical brushes. They have a stator with windings that produce a rotating magnetic field, much like an AC motor. In this sense, brushless motors can accept AC-like three-phase signals from their drives, which are converted from DC using a dedicated control circuit.
These motors are highly efficient and are increasingly used in applications that require high speed and low maintenance.
Servo Drives and Their Role in Signal Compatibility
What is a Servo Drive?
A servo drive is an electronic device that receives commands from a motion controller and translates them into power signals that drive the motor. The servo drive plays a crucial role in determining whether the motor can accept AC signals.
Servo drives can work with either AC or DC power and convert it as necessary to match the motor’s needs. For an AC servo motor, the drive will convert incoming AC power into the appropriate voltage, frequency, and phase to control the motor’s rotation.
How Servo Drives Handle AC Input
- AC Input Drives: These drives accept AC power directly from the source, typically around 120V or 240V, depending on the application. The servo drive then processes this AC power into a form that is suitable for the connected motor.
- DC Input Drives: For DC servo motors, the drive receives AC power and converts it to DC through a rectifier circuit.
A servo drive also uses the feedback from the motor encoder to adjust power delivery in real-time, ensuring that the motor reaches the desired position, speed, and torque.
AC Servo Motors vs DC Servo Motors: Which is Better?
Performance Comparison
The choice between AC servo motors and DC servo motors largely depends on the requirements of the application:
- Speed and Torque Control: AC servo motors are better suited for applications requiring high-speed, high-torque performance.
- Precision: Both AC and DC servo motors offer high precision, but AC servo motors tend to perform better in industrial environments due to their higher power capacity.
- Maintenance: DC motors generally require more maintenance due to the presence of brushes, whereas AC motors have a brushless design that is maintenance-free.
Summary Table
Criteria | AC Servo Motor | DC Servo Motor |
---|---|---|
Power Source | Alternating Current (AC) | Direct Current (DC) |
Maintenance | Low | High |
Applications | Industrial, Robotics | Small machinery, Toys |
Speed Range | Higher | Moderate |
When to Choose an AC Servo Motor
- High-Load Applications: If the application involves moving heavy machinery, an AC servo motor is recommended.
- High-Speed Requirements: For systems where high-speed rotation is necessary, AC servo motors can provide consistent performance.
When to Choose a DC Servo Motor
- Compact Projects: DC servo motors are more suitable for smaller, less demanding tasks where space is a constraint.
- Cost Sensitivity: DC servo motors are generally more cost-effective for lower-power applications.
Practical Applications of AC Servo Motors
1. Robotics
In robotics, AC servo motors provide the precision and repeatable positioning required for robotic arms. By accepting AC power and translating it into highly controlled movements, AC servo motors can ensure the smooth operation of multiple robotic joints.
2. CNC Machines
CNC (Computer Numerical Control) machines also employ AC servo motors due to their high torque and speed control. Accurate movement of the cutting tool ensures the quality of the final product, which requires consistent power from the AC motor.
3. Automated Conveyor Systems
In conveyor systems, the use of AC servo motors ensures that the movement of items on the conveyor remains consistent, even under changing loads. The ability to use AC signals directly helps in minimizing energy conversion losses.
FAQs
1. Can I connect a DC servo motor to an AC power source?
No, a DC servo motor should not be connected directly to an AC power source. You need to use a rectifier or a servo drive that can convert AC power to DC before feeding it to the motor.
2. Are AC servo motors better for industrial applications?
Yes, AC servo motors are typically better suited for industrial applications that require high power, speed, and precision, such as robotics and machine tools.
3. What role does a servo drive play in handling AC signals?
A servo drive converts the input power, whether AC or DC, into the appropriate form required by the servo motor. It also uses feedback from the motor encoder to adjust power delivery and maintain accurate control.
4. Can a brushless servo motor use AC signals?
Yes, brushless servo motors often use three-phase AC-like signals generated by the servo drive, which converts DC into this form for smoother and more efficient motor control.
5. How do I choose between an AC and a DC servo motor?
Choosing between AC and DC servo motors depends on your application. For high power and precision tasks, AC motors are recommended, while DC motors are more suited for small, simple, and cost-effective applications.
Conclusion
Servo motors are an essential part of modern automation, providing the precision and control necessary for tasks ranging from robotic arm movement to industrial CNC machining. When it comes to whether servo motors can take in AC signals, the answer lies in the type of servo motor. AC servo motors are designed specifically to accept and utilize AC signals effectively, making them a robust choice for industrial and high-performance applications. On the other hand, DC servo motors require a conversion process to work with AC power, highlighting the importance of understanding your application needs before making a choice.
For further information on servo drives and various servo motor models, feel free to explore our Servo Motor Store, which offers a wide selection of both Panasonic Servo Motors and Yaskawa Servo Drivers tailored to fit any industrial application.