How to Calculate the Torque Applied by a Servo Motor
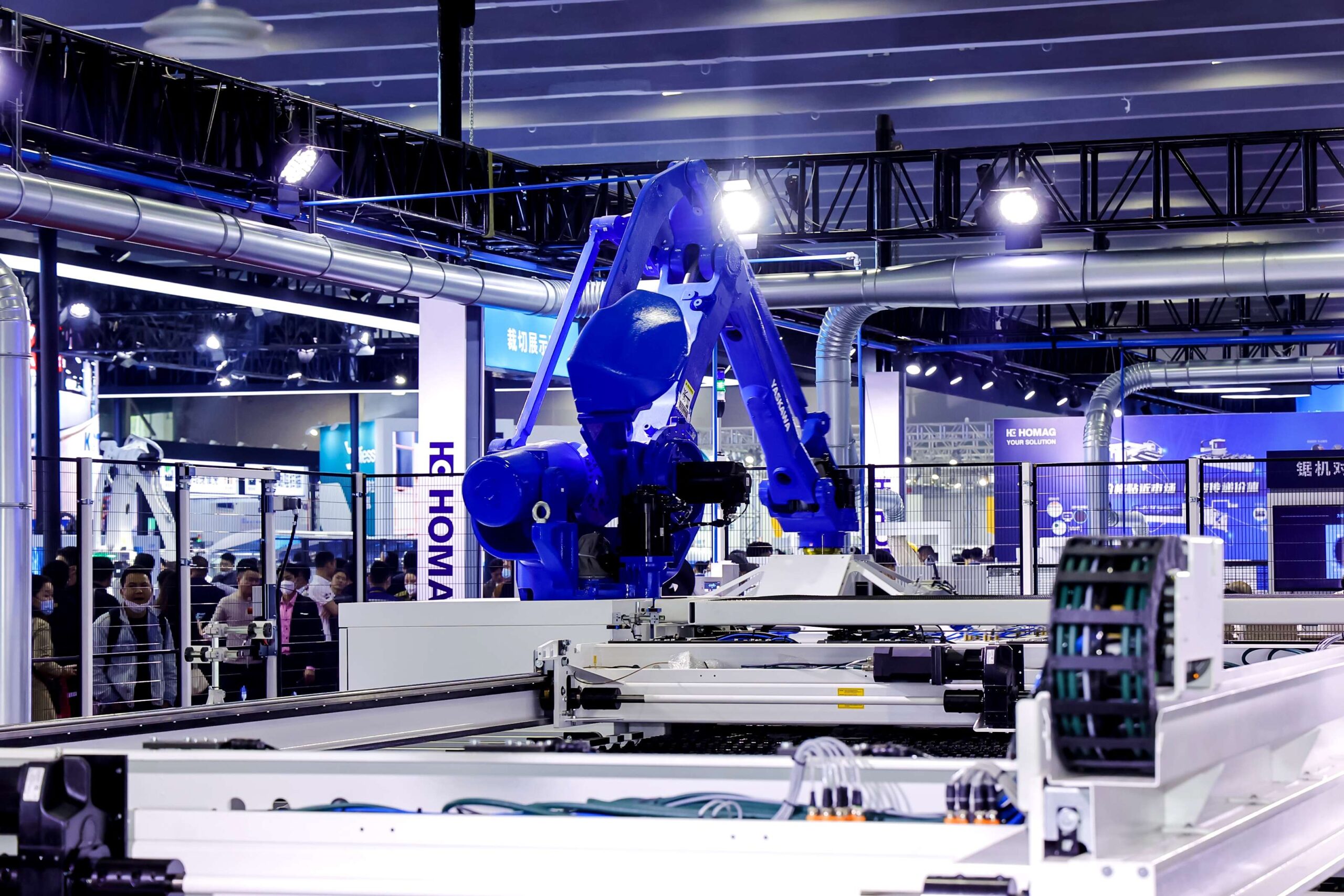
This article is your go-to guide for understanding and calculating servo motor torque. We’ll break down the complex concepts into simple terms, providing practical examples and insights. Whether you’re a hobbyist tinkering with robotics or a professional in the manufacturing industry, this article will equip you with the knowledge you need. With clear explanations and step-by-step instructions, you’ll find the answers you’re looking for to measure and apply torque effectively in your projects.
1. What is Torque, and Why is it Important in Servo Motors?
Torque is the measure of the rotational force that causes an object to rotate about an axis. It is a crucial parameter in various mechanical systems, especially in servo motors. Torque is essentially the twisting force that is applied to make something rotate. Think of it like turning a doorknob or tightening a screw. The force you apply combined with the distance from the axis (like the length of a wrench) determines the torque.
In servo motors, torque is important because it dictates the motor’s ability to move a load. A servo motor with high torque can handle heavier loads or overcome greater resistance. Servo motor torque is usually measured in Newton-meters (Nm) or ounce-inches (oz-in).
- For example, if a servo motor has a torque rating of 10 Nm, it can apply a force of 10 Newtons at a distance of 1 meter from the rotational axis. Unit Conversion to Nm Newton-meter (Nm) 1 Ounce-inch (oz-in) 0.00706155 Kilogram-force centimeter (kgf-cm) 0.0980665 Pound-foot (lb-ft) 1.35582 Note: 1 kgf-cm is the torque resulting from a force of one kilogram-force applied perpendicular to a lever which is one centimeter long.
2. How Does a Servo Motor Generate Torque?
Servo motors generate torque through the interaction of magnetic fields. Inside a servo motor, there are coils of wire and magnets. When current flows through the coils, it creates a magnetic field. This field interacts with the magnetic field of the permanent magnets, causing the motor to rotate.
- Current and Magnetic Field: When an electric current is applied through the coil, a magnetic field is generated around it. The direction of the magnetic field depends on the direction of the current.
- Interaction of Fields: This magnetic field interacts with the field of permanent magnets within the motor. Opposite poles attract, and like poles repel, creating a rotational force.
- Rotation: This interaction causes the motor’s shaft to rotate. The amount of torque produced is proportional to the current applied to the coils.
Servo motor torque is proportional to the current flowing through the coils. By controlling the current, you can control the torque.
“The torque of a servo is directly related to the current flowing through its coils. More current means more torque.”
Here’s a basic table illustrating how current affects torque:
Current (A) | Torque (Nm) |
---|---|
0.5 | 2.5 |
1.0 | 5.0 |
1.5 | 7.5 |
2.0 | 10.0 |
Note: These values are for illustrative purposes. Actual torque values will vary depending on the specific servo motor. If you want to explore a wide range of servo motors, feel free to visit our selection of Yaskawa Servo Motors. We offer a diverse range of motors with varying torque specifications to meet your needs.
3. What Factors Affect Servo Motor Torque?
Several factors can affect the torque of a servo motor. Understanding these factors can help you optimize the performance of your servo motor.
- Voltage: The operating voltage of the servo motor plays a significant role. A higher voltage can increase the torque, but it’s essential to stay within the motor’s specified voltage range to avoid damage.
- Current: As mentioned earlier, torque is proportional to the current. However, exceeding the motor’s rated current can cause it to overheat and potentially fail.
- Load: The torque load on the servo motor affects its performance. A higher load requires more torque to move. If the load exceeds the motor’s stall torque, the motor will stall and may be damaged.
- Temperature: High temperatures can reduce the efficiency of a servo motor and decrease its torque output. Proper cooling can help maintain optimal performance.
- Arm Length: In applications where a servo motor is moving an arm, the arm length affects the torque required. A longer arm requires more torque to move the same load compared to a shorter arm. Think of it as trying to lift a weight at the end of the arm versus close to your body.
Here is a table summarizing the factors:
Factor | Effect on Torque |
---|---|
Voltage | Higher voltage, higher torque |
Current | Higher current, higher torque |
Load | Higher load, more torque needed |
Temperature | Higher temp, lower torque |
Arm Length | Longer arm, more torque needed |
Note: These are general guidelines. The specific impact of each factor can vary depending on the servo motor model.
4. How to Calculate Torque Requirements for Your Servo Motor Application?
Calculating the torque requirements for your application is crucial for selecting the right servo motor. Here’s a step-by-step guide:
- Determine the Load: Identify the weight of the load you need to move. This includes any arms, attachments, or the object itself. For instance, if you’re building a robotic arm, consider the weight of the arm and the end effector, plus the maximum weight it will lift.
- Calculate the Force: Convert the weight to force. Remember, weight is a force due to gravity. On Earth, 1 kg exerts a force of approximately 9.81 Newtons (N).
- Measure the Distance: Measure the distance from the rotational axis to where the force is applied. In the case of a robotic arm, this would be the arm length when the arm is parallel to the ground.
- Multiply: Calculate the torque using the formula: Torque (Nm) = Force (N) * Distance (m).
For example, if you have a robotic arm that is 0.5 meters long and needs to lift a 1 kg object (approximately 9.81 N), the required torque would be 9.81 N * 0.5 m = 4.905 Nm.
Note: This calculation assumes the force is applied perpendicular to the arm. In real-world applications, you may need to take into account angles and other forces, but this gives you a good starting point. If you have specific requirements or need guidance on selecting the right motor, our team is always ready to assist you.
- Additional Considerations:
- Acceleration: If your application requires rapid acceleration, you’ll need additional torque. The amount of torque needed for acceleration depends on the moment of inertia of the load and the desired acceleration rate.
- Friction: Friction in the system can increase the torque required. It’s essential to account for frictional forces, especially in applications with bearings or moving parts.
- Safety Margin: It’s always a good idea to choose a servo motor with a torque rating slightly higher than your calculated requirement. This provides a safety margin and ensures reliable operation.
5. How to Measure the Torque of a Servo Motor?
Measuring the torque of a servo motor can be done in several ways. Here are two common methods:
- Using a Torque Sensor: A torque sensor is a device that measures rotational force. It can be directly attached to the output shaft of the servo motor to measure the torque produced.
- Attach the torque sensor to the servo motor’s shaft.
- Apply a known load to the sensor.
- Read the torque value from the sensor.
- Using a Force Sensor: If you don’t have a torque sensor, you can use a force sensor along with a known arm length.
- Attach an arm of known length to the servo motor’s shaft.
- Attach the force sensor to the end of the arm.
- Apply a load or move the arm against resistance.
- Read the force from the sensor.
- Calculate the torque using the formula: Torque = Force * Arm Length.
For example, if you have a 0.2-meter arm and the force sensor reads 5 N, the torque is 5 N * 0.2 m = 1 Nm.
Note: When measuring torque, ensure the servo motor is securely mounted and the setup is safe.
Method | Pros | Cons |
---|---|---|
Torque Sensor | Direct measurement, accurate | Can be expensive, requires specific sensor |
Force Sensor | Can use common sensors, cost-effective | Requires calculation, may be less accurate |
Note: Torque sensors provide a direct and accurate measurement but can be more expensive. Using a force sensor is a more budget-friendly approach but requires calculation and may be slightly less accurate due to potential measurement errors in force and distance. For hobbyists and small-scale projects, our Original Panasonic Servo Motor MINAS A5 series offers a great balance of performance and affordability.
6. What is the Difference Between Rated Torque and Stall Torque?
Rated torque and stall torque are two important specifications of a servo motor. Understanding the difference between them is crucial for choosing the right motor for your application.
- Rated Torque: This is the torque that the servo motor can continuously produce without overheating. It’s the torque at which the motor can operate for extended periods under normal conditions. The rated torque is typically lower than the maximum torque the motor can produce.
- Stall Torque: This is the maximum torque the servo motor can produce when it’s stalled, meaning the shaft is not rotating. When a servo motor is stalled, it draws the maximum current and generates the highest torque. However, operating a servo motor at stall torque for an extended time can cause it to overheat and potentially damage the motor.
For example, a servo motor might have a rated torque of 5 Nm and a stall torque of 10 Nm. This means it can continuously operate at 5 Nm but can produce up to 10 Nm for short periods.
Here’s a table summarizing the differences:
Specification | Description | Operation Time |
---|---|---|
Rated Torque | Torque for continuous operation | Long |
Stall Torque | Maximum torque when the motor is not rotating (stalled) | Short |
Note: Always refer to the servo motor’s datasheet for accurate rated torque and stall torque values. Exceeding these values can lead to reduced performance or damage to the motor.
7. How to Increase the Torque of a Servo Motor?
There are several ways to increase the torque output of a servo motor:
- Increase Voltage: Increasing the voltage supplied to the servo motor can increase its torque. However, it’s crucial to stay within the motor’s specified voltage range to avoid damage.
- Use Gears: Gears can be used to multiply the torque of a servo motor. A gear system with a higher gear ratio will increase the torque at the output shaft, although it will also reduce the speed.
- Choose a Higher Torque Motor: If you need significantly more torque, the best solution is to choose a servo motor with a higher torque rating. This ensures that the motor can handle the required load without overheating or getting damaged.
For example, if you have a servo motor with a torque of 2 Nm and you need 4 Nm, you could use a 2:1 gear ratio to double the torque.
Note: When increasing torque through gearing, remember that you’ll also decrease the speed. It’s a trade-off between torque and speed.
Method | Pros | Cons |
---|---|---|
Increase Voltage | Simple, direct increase in torque | Risk of damage if voltage limits are exceeded |
Use Gears | Significant torque increase | Reduces speed, adds complexity |
Higher Torque Motor | Reliable, designed for higher torque | May be more expensive, larger size |
Note: Each method has its advantages and disadvantages. Choose the method that best suits your application’s requirements and constraints. If you’re looking for a motor with higher torque capabilities, consider exploring our selection of Original Panasonic Servo Motor MINAS A6 series. These motors offer excellent performance for demanding applications.
8. Can a Sensor Help in Monitoring Servo Motor Torque?
Yes, sensors can play a crucial role in monitoring servo motor torque. They provide real-time feedback on the torque being applied, which can be invaluable in various applications.
- Torque Sensors: As mentioned earlier, torque sensors directly measure the rotational force applied by the servo motor. They can be integrated into the motor system to provide continuous torque readings. This data can be used to monitor performance, detect overloads, and prevent damage.
- Current Sensors: Since torque is proportional to the current in a servo motor, a current sensor can indirectly measure torque. By monitoring the current draw, you can estimate the torque being produced. This method is less accurate than using a torque sensor but can be more cost-effective.
- Encoders: Encoders provide position feedback and can be used to infer torque in some applications. By measuring the servo motor’s position and knowing the load characteristics, you can compute the torque. This method is more complex and requires careful calibration.
For example, if you have a robotic arm lifting a known weight, you can use an encoder to measure the arm’s position and calculate the torque being applied based on the weight and arm length.
Here’s a table summarizing the types of sensors and their uses:
Sensor Type | Measurement | Torque Measurement | Accuracy | Cost |
---|---|---|---|---|
Torque Sensor | Direct Torque | Direct | High | High |
Current Sensor | Current | Indirect | Medium | Low |
Encoder | Position | Indirect | Low | Medium |
Note: The choice of sensor depends on the specific application requirements, accuracy needs, and budget constraints.
9. What are Common Issues Related to Torque in Servomotors?
Several common issues can arise related to torque in servomotors. Understanding these issues can help you troubleshoot and maintain your servo motor system effectively.
- Insufficient Torque: If the servo motor does not have enough torque for the application, it may struggle to move the load or may stall. This can lead to jerky movements, slow response, or complete failure to operate.
- Solution: Choose a servo motor with a higher torque rating or use gears to increase the torque.
- Overheating: Operating a servo motor near its stall torque for extended periods can cause it to overheat. This can reduce the motor’s lifespan and may lead to failure.
- Solution: Ensure proper cooling, reduce the load, or choose a motor with a higher rated torque.
- Oscillations: In some cases, a servo motor may oscillate around the desired position, especially when dealing with high torque loads. This can be caused by various factors, including improper tuning of the control system or mechanical issues.
- Solution: Tune the control parameters, check for mechanical play or backlash, and ensure the servo motor is properly mounted.
“A common mistake is choosing a servo motor based solely on stall torque without considering the continuous torque requirements, leading to overheating issues.”
Issue | Symptoms | Possible Causes |
---|---|---|
Insufficient Torque | Slow movement, stalling, unable to move load | Load too heavy, motor too small |
Overheating | Motor hot to touch, reduced performance, failure | Exceeding rated torque, poor cooling |
Oscillations | Jerky movement around the target position | Poor control tuning, mechanical play, high inertia |
Note: Regular monitoring and maintenance can help prevent these issues and ensure the longevity of your servo motor system.
10. How to Choose the Right Servo Motor Based on Torque Needs?
Choosing the right servo motor based on torque needs involves several steps:
- Calculate Torque Requirements: As discussed earlier, determine the torque needed for your application by considering the load, distance, acceleration, and any other relevant factors.
- Consider Duty Cycle: Determine whether your application requires continuous operation or intermittent use. For continuous operation, choose a motor with a rated torque that meets or exceeds your calculated requirement. For intermittent use, you may consider a motor where the stall torque meets your needs, but ensure it won’t be stalled for extended periods.
- Factor in Safety Margin: It’s a good practice to add a safety margin to your torque calculations. Choose a motor with a torque rating 20-50% higher than your calculated requirement to account for unexpected loads or variations.
- Evaluate Speed Requirements: Torque and speed are inversely related in servo motors. If your application requires high speed, you may need a motor with a higher power rating to achieve the desired torque at that speed.
- Check Physical Size and Mounting: Ensure the servo motor fits within your system’s physical constraints and that the mounting options are compatible with your setup.
- Consider Environmental Factors: If your application involves extreme temperatures, humidity, or other harsh conditions, choose a servo motor designed to withstand those conditions.
“Don’t just look at the price tag. Consider the long-term cost, including potential maintenance and replacement, when choosing a servo motor based on its torque rating.”
Here’s a table summarizing the selection criteria:
Criteria | Considerations |
---|---|
Torque Requirement | Calculate based on load, distance, acceleration |
Duty Cycle | Continuous vs. intermittent use, rated vs. stall torque |
Safety Margin | Add 20-50% to calculated torque |
Speed | Higher speed may require higher power for the same torque |
Size & Mounting | Physical dimensions, mounting compatibility |
Environment | Temperature, humidity, other harsh conditions |
Note: These criteria provide a general guideline. The specific requirements of your application may necessitate additional considerations. For example, in robotics applications, the moment of inertia of the load and the required acceleration play a significant role. Our Original Panasonic Servo Motor MINAS A5 750W Break MSMJ082G1V/MSMD082G1V is a popular choice for such applications due to its robust performance and reliability.
Summary
Here’s a quick recap of the key takeaways from this article:
- Torque is the rotational force that causes an object to rotate.
- Servo motor torque is crucial for determining the motor’s ability to move a load.
- Torque is generated in servo motors through the interaction of magnetic fields.
- Factors like voltage, current, load, temperature, and arm length affect servo motor torque.
- Calculate torque requirements by considering the load, force, and distance from the axis.
- Torque can be measured using torque sensors or force sensors.
- Rated torque is for continuous operation, while stall torque is the maximum torque at stall.
- Torque can be increased by using gears, increasing voltage, or choosing a higher torque motor.
- Sensors can help monitor torque and prevent issues like overheating or insufficient torque.
- Choose the right servo motor based on torque needs, duty cycle, safety margin, speed requirements, size, and environmental factors.
- Common issues related to torque include insufficient torque, overheating, and oscillations.
- Always refer to the servo motor’s datasheet for accurate specifications.
- Consider the specific requirements of your application, such as acceleration and moment of inertia.
- Our website offers a wide range of servo motors to meet various torque requirements, including the SGD7S-120A00A Original Yaskawa Single axis servo driver SGD7S-120A00A and SGD7S-120A00A002 Original Yaskawa Single axis servo driver SGD7S-120A00A002.
Remember, understanding servo motor torque is essential for building efficient and reliable systems. Whether you’re working on a hobby project or an industrial application, these insights will help you make informed decisions and achieve optimal performance. We are committed to protecting your privacy; please review our privacy policy for more information.
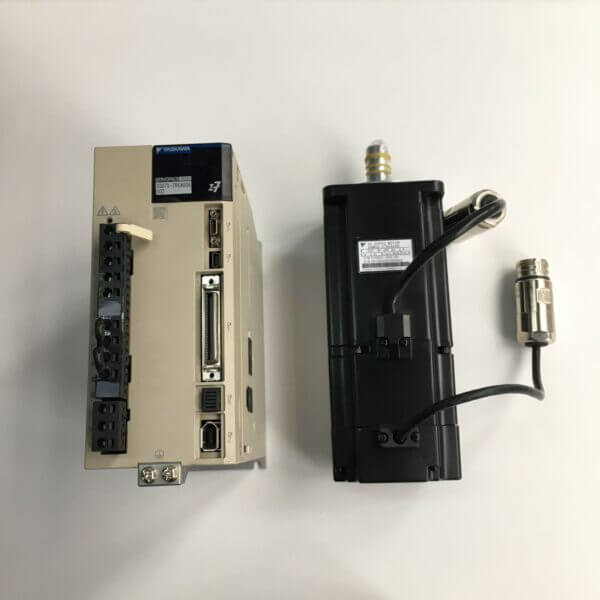
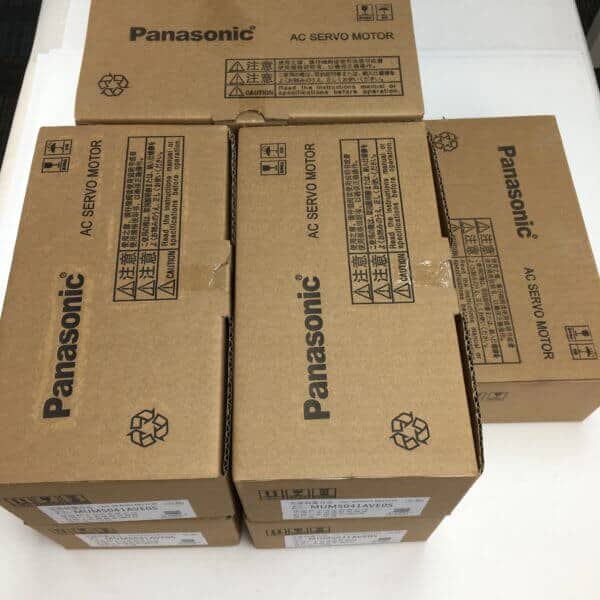