How to Check Step Response of a Servo Motor: A Complete Guide
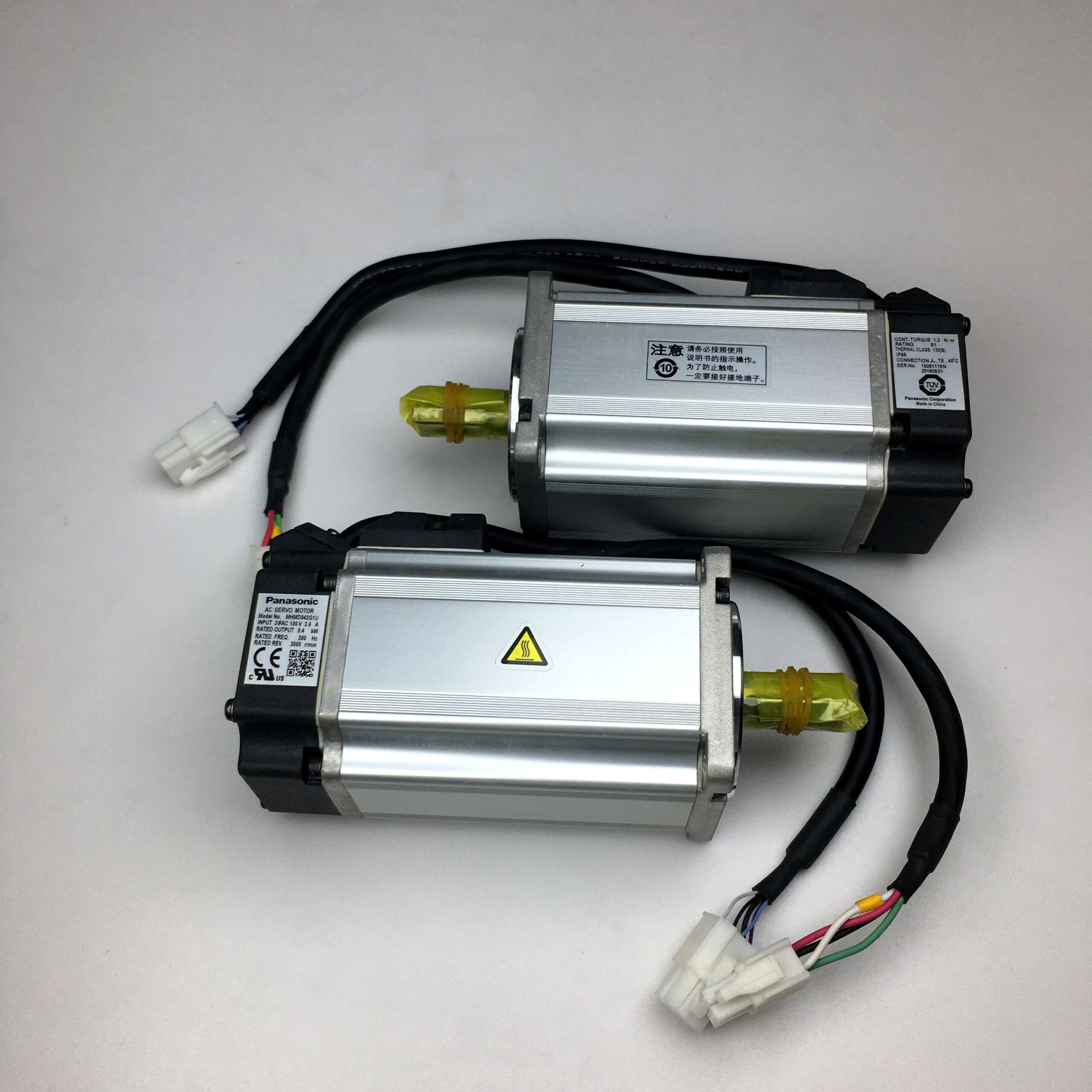
Servo motors are widely used in various industries due to their precision in controlling speed, acceleration, and position. One of the crucial performance aspects of a servo motor is its step response, which allows engineers to assess the motor’s dynamic behavior and overall performance. Understanding and checking the step response can provide essential insights into system efficiency and help diagnose issues early. This article will guide you through everything you need to know about checking the step response of a servo motor, with step-by-step instructions, practical examples, and useful tips.
Understanding the Step Response of a Servo Motor
The step response is essentially how a system reacts when subjected to a sudden change, typically a step change in input. In the case of a servo motor, the step response evaluates how well the motor can follow sudden positional commands and return to stability without overshooting or oscillating excessively.
Key Parameters of Step Response
The step response of a servo motor is characterized by several key parameters:
- Rise Time: The time it takes for the motor to go from 10% to 90% of the desired position.
- Overshoot: The extent to which the motor exceeds the desired position before settling.
- Settling Time: The time taken for the motor to stabilize within a specific error margin.
- Steady-State Error: The difference between the final motor position and the desired target position.
Each of these parameters provides insight into the motor’s accuracy, speed, and stability. A good step response is defined by minimal overshoot, short settling time, and negligible steady-state error.
Importance of Step Response in Servo Motors
The step response of a servo motor is a vital indicator of its dynamic performance. It tells you how well the servo can adapt to sudden changes in commands, an important aspect for applications that require precise, dynamic motion such as robotics, CNC machining, and automated conveyor systems.
If the step response of a servo motor is not optimized, you might experience:
- Inaccurate Positioning: Difficulty in achieving desired positions accurately.
- Excessive Oscillation: The system may keep oscillating, leading to wear and increased maintenance.
- Slow Response Time: A sluggish system that cannot adapt quickly to new commands, reducing overall productivity.
Tools and Equipment Needed to Check Step Response
To effectively check the step response of a servo motor, you will need the following tools and equipment:
- Oscilloscope: An oscilloscope is essential for capturing the motor’s response to a step input.
- Function Generator: This device is used to apply the step input signal to the motor’s control system.
- Servo Drive Software: Most modern servo systems come with proprietary software that allows you to set input parameters and analyze the response.
- Servo Motor Test Stand: A sturdy setup to mount the servo motor and safely test its responses.
For a reliable and robust servo motor suitable for high-precision applications, consider exploring the Original Panasonic Servo Motor MINAS A5 1KW available at Servo Motor Store.
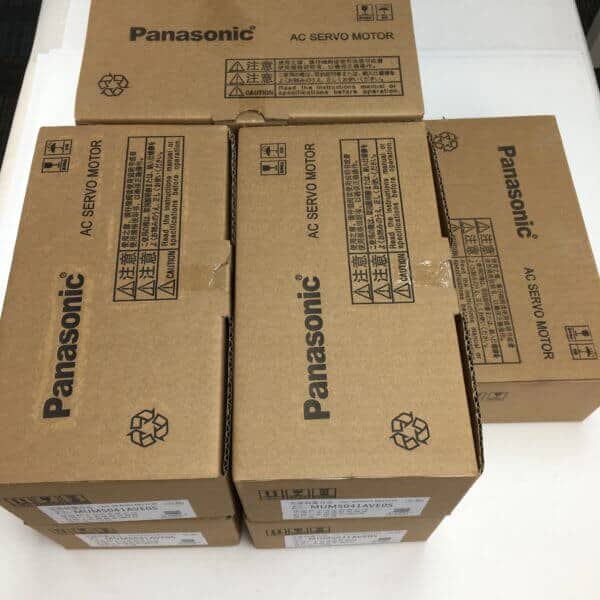
Step-by-Step Procedure to Check Step Response
1. Preparing the Servo Motor
Before you begin, ensure the servo motor is securely mounted on a test stand to avoid movement during operation. Verify that the power supply, drive, and feedback (encoder) connections are in good condition.
- Safety First: Always work in a safe, well-ventilated area with proper protective gear such as insulated gloves.
- Software Setup: Use the servo drive software to configure initial settings, such as proportional gain (P), integral gain (I), and derivative gain (D) if you are using a PID controller.
2. Apply a Step Input Signal
- Set the Function Generator: Connect the function generator to the servo driver, setting it to produce a step input signal. Typically, this is a square wave that changes from one value to another abruptly.
- Select Amplitude: Choose an amplitude that represents a realistic change in motor position, such as a 10-degree step change.
The input should be visible on the oscilloscope and ideally reflected in the motor’s output.
3. Observe the Motor Response
- Oscilloscope Readings: Monitor the output on the oscilloscope. The rise time, overshoot, settling time, and steady-state error can be derived from the waveform.
- Evaluate the Curve: A well-behaved motor will exhibit a smooth rise with minimal overshoot and a short settling time. Excessive oscillations or a long settling time indicate issues with the control parameters.
For example, using a Yaskawa Single Axis Servo Driver with built-in diagnostics features can simplify the evaluation process. More details can be found here.
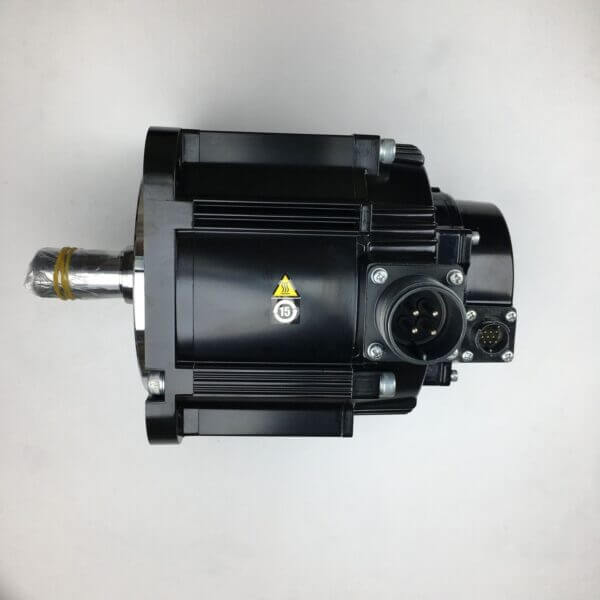
4. Adjust Controller Parameters
- Adjust Proportional, Integral, and Derivative Gains: Most servo motors use a PID controller to manage the step response. Adjust the P, I, and D values to improve the response. If there is too much overshoot, consider reducing the proportional gain.
- Repeat Test: Apply the step input again and observe the changes on the oscilloscope. Fine-tune until the desired performance is achieved.
5. Record Results and Analyze
- Document Parameters: Record the optimal settings for your servo motor, including rise time, overshoot, settling time, and other observations.
- Compare to Manufacturer Specifications: Consult the motor datasheet to see if the recorded values meet the manufacturer’s specifications for performance.
Common Issues and Troubleshooting Tips
Excessive Overshoot
If your servo motor shows excessive overshoot, it could be due to a high proportional gain or low damping.
- Solution: Reduce the proportional gain slightly and increase the derivative gain to provide more damping.
Long Settling Time
A long settling time indicates that the motor struggles to reach the target position and stabilize.
- Solution: Increase the proportional gain to make the system more responsive, but avoid excessive values that could lead to instability.
Oscillations
Persistent oscillations indicate improper tuning of the PID parameters.
- Solution: Reduce the integral gain to lower the accumulated error or increase damping via the derivative gain.
Practical Applications of Step Response Analysis
The step response of a servo motor is critical in several practical applications where precision and accuracy are paramount. For instance:
- Robotics: In robotics, the step response ensures that robotic arms move precisely to designated positions without delay or overcorrection.
- CNC Machines: CNC machines depend on accurate step response for the cutting head to follow predefined paths without deviation, ensuring product quality.
- Packaging Systems: In high-speed packaging systems, the response time directly impacts the rate at which packages are processed, affecting efficiency.
Frequently Asked Questions (FAQs)
1. Why is step response important in servo motors?
The step response helps determine how quickly and accurately a servo motor can react to sudden changes in command, which is crucial for ensuring smooth and precise operation in industrial applications.
2. How do I reduce overshoot in the step response?
Reducing overshoot typically involves lowering the proportional gain or increasing the derivative gain. This helps minimize the risk of the motor exceeding the desired position.
3. Can software help in checking step response?
Yes, modern servo drives come with proprietary software that allows you to apply step inputs, observe the response, and adjust settings easily. This makes the process more efficient and reliable.
4. How often should step response tests be conducted?
It’s advisable to perform step response tests during initial setup, after maintenance, or whenever there are noticeable performance changes in the motor.
5. What are the dangers of an improper step response?
An improper step response can lead to excessive mechanical wear, inaccurate positioning, and even potential safety hazards in automated systems.
Conclusion
Checking the step response of a servo motor is an essential part of maintaining high performance in dynamic applications. Understanding the fundamentals, using the right tools, and knowing how to interpret the results will help you keep your servo motor operating smoothly and accurately. Whether you are in robotics, automation, or CNC machining, proper step response analysis ensures that your systems are efficient, reliable, and safe.
For more information on servo motors and accessories, including servo motor drivers and testing equipment, visit Servo Motor Store. We provide a range of high-quality products that are ideal for keeping your automation systems running at peak efficiency.