How to Check Step Response of a Servo Motor: A Comprehensive Guide
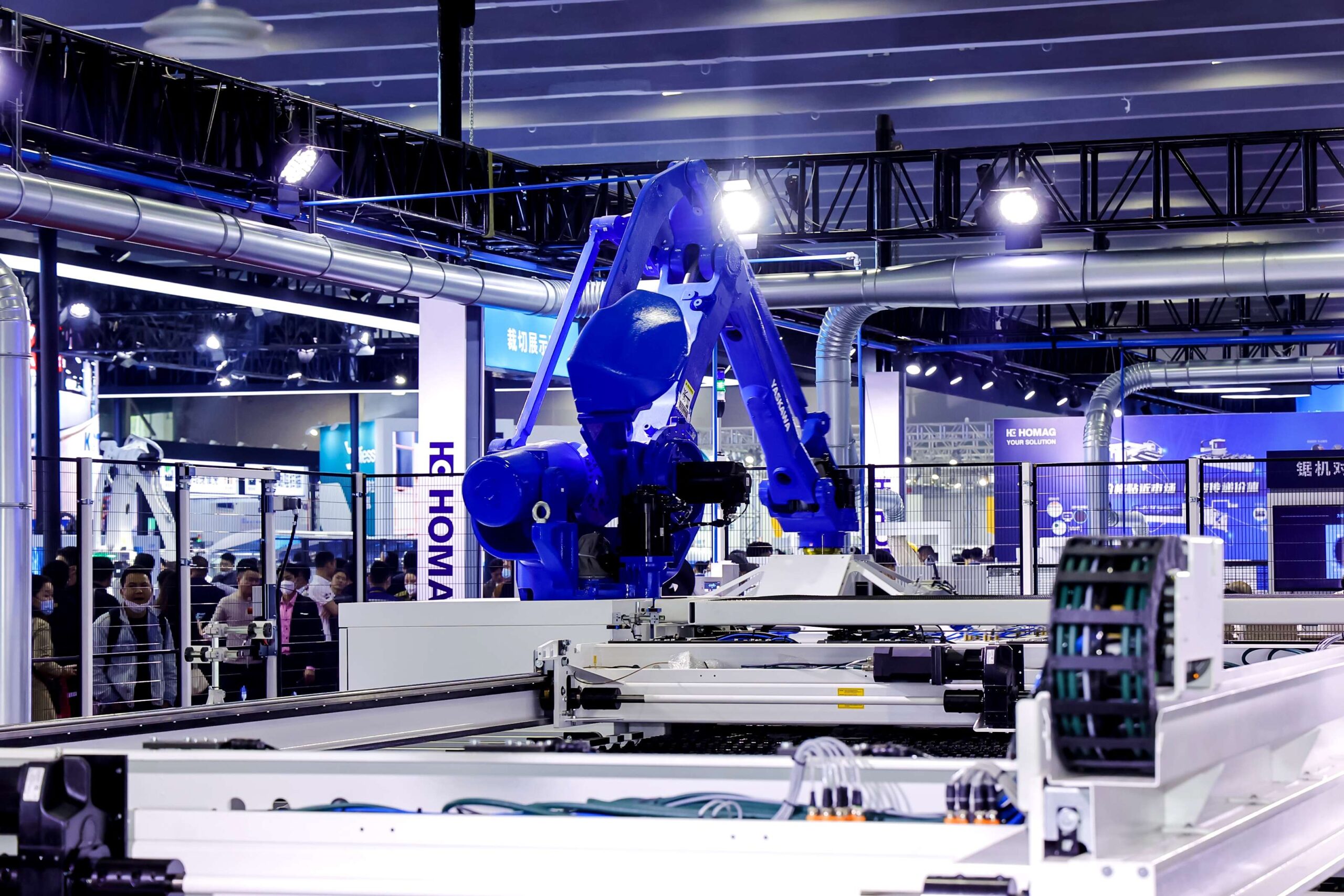
Servo motors play an essential role in numerous applications, ranging from robotics to CNC machines. A crucial aspect of optimizing these motors is understanding how they respond to different control inputs. This process, known as evaluating the step response of a servo motor, provides insights into how quickly and accurately a motor can reach its desired position. In this comprehensive guide, we will delve into the fundamentals of step response, how to test it effectively, and why this matters for your projects.
Understanding the Concept of Step Response in Servo Motors
What is Step Response?
The step response of a servo motor is a measure of how the motor responds to a sudden change in the control input, often represented as a sudden increase in the reference signal. Essentially, it describes how the motor reaches its target position after an abrupt command. This helps assess the motor’s dynamic performance, which includes the speed, precision, and stability of movement.
Step response is vital for applications where accuracy and rapid movement are paramount. Understanding how your servo motor behaves when subjected to a sudden control command helps you determine if it can meet your operational requirements. The key parameters measured during a step response test include:
- Rise Time: The time it takes for the output to go from 10% to 90% of its final value.
- Overshoot: How much the motor overshoots its target before settling down.
- Settling Time: How long it takes for the motor to remain within a small percentage of the target value.
- Steady-State Error: The difference between the final motor position and the desired position.
Why is Step Response Important?
Accurate step response evaluation is critical for determining whether a servo motor is suitable for high-precision applications like CNC machines or robotic arms. A poor step response can lead to excessive vibration, slower operational cycles, and increased wear and tear on the machinery.
To optimize a motor’s performance, engineers often need to adjust parameters within the servo motor drive. Proper tuning can significantly improve motor efficiency, reducing both the error and the time it takes to achieve the target position.
For information about different models of servo motors that offer robust control features, you can check out Original Panasonic Servo Motor MINAS A5 1KW MDME102GCH.
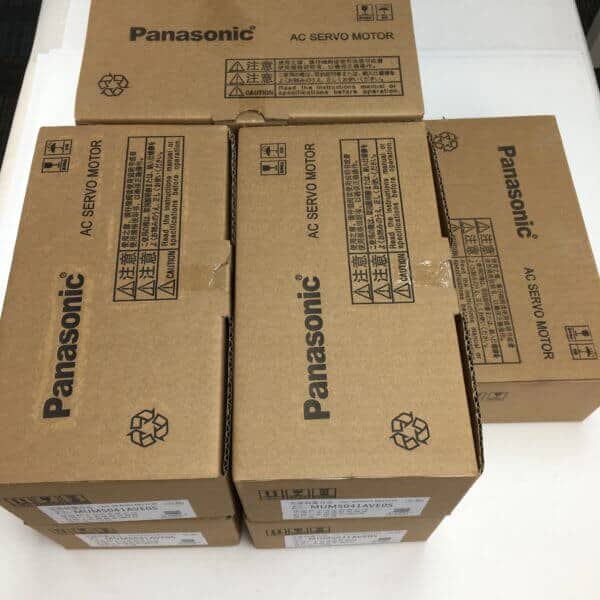
Tools Required for Testing the Step Response of a Servo Motor
To accurately measure the step response of a servo motor, you need some essential tools and equipment:
- Oscilloscope: To visualize the response waveform.
- Function Generator: Generates the step signal to trigger motor response.
- Servo Drive Controller: Allows you to control input signals and adjust gain settings.
- Multimeter: For basic checks of current and voltage.
- Data Acquisition System (DAQ): For recording data and analyzing response.
Having these tools at your disposal allows you to accurately capture and analyze how well your servo motor responds to sudden changes in control input.
Step-by-Step Guide to Testing Step Response
1. Setting Up the Equipment
The first step is to set up your equipment to conduct the test safely and effectively.
- Connect the Servo Motor to the Servo Drive: Ensure proper connections between the servo motor and the servo drive controller. Make sure all cables are securely attached to prevent signal interference.
- Power On the Setup: Connect the power supply and turn on the equipment, making sure all components are functioning correctly.
- Connect the Oscilloscope: Connect the oscilloscope to the output of the motor. This will help you visualize the motor’s step response.
2. Generating a Step Input Signal
Next, you will use a function generator to create a step input signal for the motor. Set up the signal parameters as follows:
- Amplitude: Determine an appropriate amplitude that falls within the motor’s specifications.
- Pulse Width: Set the width of the step appropriately so that it represents a sudden change.
Ensure the step signal is set within the motor’s operational limits to avoid any potential damage to the system.
3. Observing and Analyzing the Response
Once the step signal is applied, observe the waveform on the oscilloscope. Key metrics to focus on include:
- Rise Time and Settling Time: Measure how fast the motor reaches its desired position and how quickly it settles without oscillation.
- Overshoot: Note the amount by which the motor exceeds the target position.
- Stability: Determine if the motor reaches a stable state quickly or continues oscillating.
A well-tuned servo motor should show minimal overshoot and a short settling time. If the response shows a high overshoot or takes a long time to settle, adjustments in the PID control parameters may be required.
Tuning the Servo Drive for Optimal Step Response
Understanding PID Control
Proportional-Integral-Derivative (PID) control is the most commonly used feedback loop mechanism to fine-tune a servo motor’s performance. By adjusting the P, I, and D values, you can significantly influence the motor’s response.
- Proportional (P): Determines the reaction to the current error. High P gain may result in faster response but could lead to overshoot.
- Integral (I): Helps eliminate steady-state errors. However, too high an I value can result in slower response and integrator windup.
- Derivative (D): Reacts to the rate of error change, helping reduce overshoot and oscillations.
How to Tune the PID for Better Step Response
- Start with P Gain: Gradually increase the P gain until the motor starts responding rapidly. Be careful not to increase it too much, as it can cause excessive oscillation.
- Adjust the I Gain: Introduce I gain to reduce the steady-state error. Find a balance to minimize the settling time without causing instability.
- Fine-Tune with D Gain: Finally, adjust the D gain to counteract any oscillation. The D gain is useful in reducing overshoot and ensuring the motor reaches the desired position efficiently.
For more information on servo drives that offer advanced tuning options, visit the Yaskawa SGD7S Servo Driver.
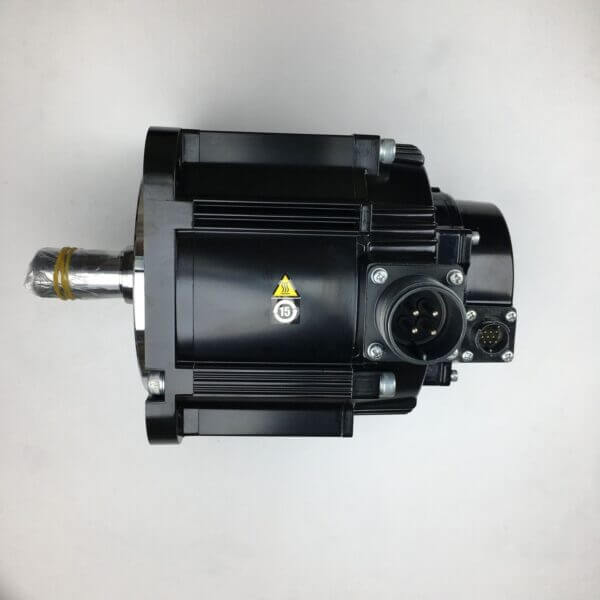
Interpreting Common Step Response Issues
1. High Overshoot
High overshoot typically indicates that the motor’s P gain is too high, causing the system to react too aggressively to the step input. This can lead to excessive movement beyond the desired position.
- Solution: Reduce the P gain or increase the D gain to dampen the response.
2. Slow Response or Long Settling Time
A slow response means that the motor takes too long to reach the target position. This often indicates insufficient P gain or inappropriate I gain settings.
- Solution: Gradually increase the P gain to speed up the response while monitoring the overall stability.
3. Continuous Oscillation
Oscillation can occur if the PID gains are not properly balanced, particularly if the I gain is too high or the D gain is too low.
- Solution: Reduce the I gain or slightly increase the D gain to provide more damping and stabilize the motor.
Benefits of Evaluating Step Response
Evaluating the step response of a servo motor has several benefits, including:
- Improved Efficiency: Fine-tuning the motor ensures that it reaches desired positions faster, reducing the overall cycle time.
- Reduced Mechanical Stress: By minimizing oscillations and overshoot, you decrease wear and tear on mechanical components, enhancing the longevity of the system.
- Greater Precision: Ensuring a smooth and quick response to step changes directly improves the precision of positioning, which is critical in robotics and automation.
Conclusion
Understanding and evaluating the step response of a servo motor is crucial for achieving optimal motor performance in any high-precision application. By using tools like an oscilloscope and a function generator, and adjusting the PID control parameters, you can achieve a balance between speed, accuracy, and stability. Proper tuning not only improves the performance of the motor but also extends the life of the equipment by reducing unnecessary mechanical stress.
If you’re looking for high-quality servo motors and drives that support easy tuning and optimal performance, visit the Servo Motor Store. Our experts are available to help you find the best solutions for your automation needs.
Frequently Asked Questions
1. What is the ideal step response for a servo motor?
An ideal step response has minimal overshoot, a fast rise time, and a short settling time with no oscillations.
2. How do I reduce overshoot in my servo motor?
To reduce overshoot, decrease the P gain or increase the D gain in your PID controller settings. This helps in providing a more dampened response.
3. Why is the D gain important in tuning a servo motor?
The D gain helps reduce oscillations by counteracting the rate of change of the error. It is crucial for ensuring that the motor stops exactly at the desired position without excessive movements.
4. Can I use any servo motor for high-speed applications?
Not all servo motors are suited for high-speed applications. Ensure the motor specifications meet the required speed and torque demands of your particular use case.