How to Choose a Servo Motor: A Detailed Guide for Precision Applications
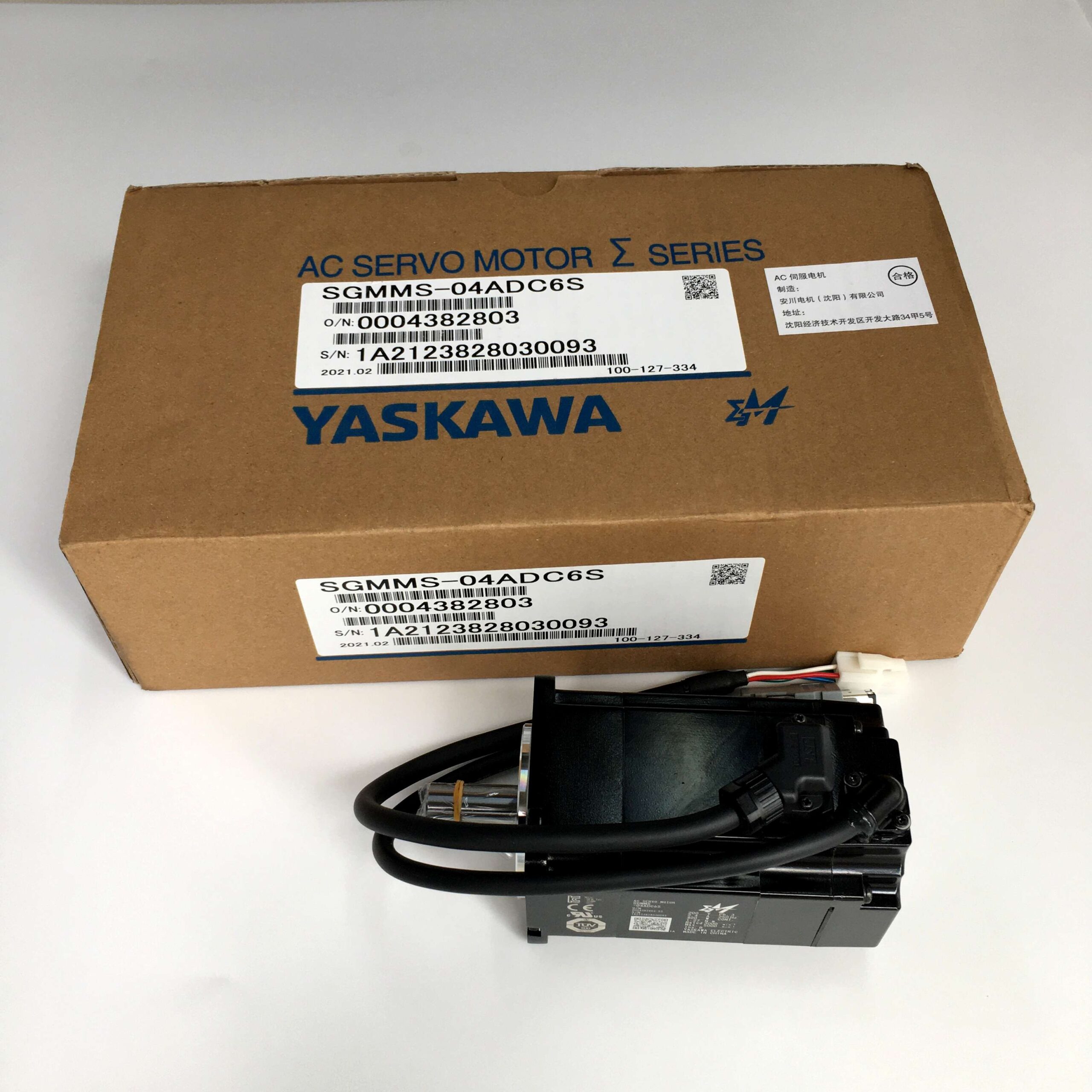
Servo motors are a critical component in a wide range of industrial applications, from robotics to automation systems. Selecting the right servo motor for your specific needs can be a challenging task. This article will provide a detailed guide on how to choose a servo motor that fits your requirements, focusing on various factors like torque, speed, inertia, and application type. Let’s dive into the key aspects that you should consider for effective servo motor selection.
Understanding Servo Motors and Their Applications
What is a Servo Motor?
A servo motor is a rotary actuator or motor that allows for precise control of angular or linear position, velocity, and acceleration. Servo motors are used in closed-loop systems where feedback signals, typically from encoders, provide data to adjust the motor’s output and ensure accurate control. They’re well-known for their precision and are commonly used in robotics, conveyor systems, and CNC machines.
Servo motors have several distinct features:
- High Precision: Due to the use of feedback mechanisms, servo motors offer excellent precision in controlling the position.
- Speed Control: They can vary speed according to the input control signal, allowing versatile use across different applications.
- Torque Control: Servo motors can adjust their torque to adapt to load changes.
Applications of Servo Motors
Servo motors are versatile and are used in many industrial and commercial applications:
- Robotics: Servo motors provide the precise movements required for robotic joints.
- CNC Machines: Used for precise control of milling, drilling, and cutting.
- Automated Conveyor Systems: Servo motors are used to ensure smooth movement of materials along conveyor lines.
- Medical Devices: Applications like surgical robots and prosthetics also depend on the accuracy of servo motors.
For instance, you can check out our Yaskawa series prodcuts that are ideal for automation needs where precision and reliability are crucial.
Key Factors to Consider When Choosing a Servo Motor
1. Torque Requirements
Torque is a key factor when selecting a servo motor. It is essential to understand both continuous torque and peak torque requirements:
- Continuous Torque: This is the torque a motor needs to maintain throughout normal operation without overheating.
- Peak Torque: This represents the torque that the motor can provide for short periods, typically during acceleration.
For instance, when working on a robotic arm, the continuous torque is required for holding positions, while peak torque may be needed when initiating movements.
Calculating Torque
A simple way to estimate the torque requirements is to determine the load’s weight, radius, and friction components in your setup. This can be done using the formula:
Torque (Nm) = Force (N) x Radius (m)
Selecting a motor with an appropriate torque rating ensures that the servo can handle the load without causing damage or instability.
For more information on torque-controlled motors, take a look at our Panasonic Servo Motor MINAS A5 1KW.
2. Speed and Velocity
Speed is another important consideration when choosing a servo motor. Depending on your application, you need to select a motor that can deliver the required speed without compromising on control or accuracy.
- High-speed applications: These are typically found in conveyor belts and packaging systems where rapid movement is required.
- Low-speed applications: Precision tasks like pick-and-place robots or assembly operations require lower speeds but higher torque.
The speed-torque curve of a motor is a crucial factor to examine, as it illustrates the relationship between the motor’s speed and the torque it can deliver. Servo motors designed with a broader speed range are generally more versatile.
3. Inertia and Load Matching
Matching the inertia of the servo motor to the load inertia is vital for system stability. A poorly matched inertia ratio can result in oscillations, vibrations, and an overall lack of control.
- Inertia Ratio: Ideally, the load-to-motor inertia ratio should be less than 10:1. If the load inertia is too high, the servo motor may not be able to accurately control the load, leading to inefficient operation.
- Gear Reduction: Using a gearbox can help match load inertia with motor inertia by effectively reducing the load’s impact on the motor.
“The right inertia ratio can make all the difference in the smooth and efficient performance of a servo motor-driven system.”
4. Gear Ratios and External Forces
Servo motors often utilize gear reducers to adjust the output speed and torque to better suit the application. The gear ratio can significantly impact both the speed and torque characteristics of the motor.
For example, if a gear ratio of 5:1 is used, the motor’s speed is reduced by a factor of five, while the torque is increased by the same factor. This setup is particularly useful in applications requiring high torque at a lower speed, such as positioning heavy objects.
External Forces: Factors like gravitational pull and mechanical forces should also be considered when determining the gear ratio, especially in applications where parts of the load may need to be suspended.
5. Servo Drive Requirements
Servo drives are used to control the power delivered to the motor. The specifications of the drive should match the requirements of the servo motor, including:
- Voltage: Ensure the servo drive can handle the voltage requirements of the motor.
- Continuous Current and Peak Current: The drive should support the motor’s continuous and peak current needs to avoid overheating and to ensure consistent performance.
For a complete servo drive solution, consider visiting our Servo Motor Store for high-performance options.
Comparing Different Servo Motors
DC vs. AC Servo Motors
Servo motors are available as AC and DC types. Each has specific benefits that may suit different applications:
Feature | AC Servo Motor | DC Servo Motor |
---|---|---|
Efficiency | Generally more efficient in high-power apps | Suitable for lower power applications |
Maintenance | Less maintenance due to brushless design | Requires periodic brush maintenance |
Speed Range | Wider speed range with better control | Limited speed range |
Cost | More expensive upfront | Usually more affordable |
AC servo motors are preferred for industrial automation, whereas DC servo motors are often used in hobbyist projects or low-power devices.
Continuous vs. Intermittent Duty
Servo motors may also be rated based on whether they are intended for continuous duty or intermittent duty. A continuous-duty motor can run for long periods without overheating, while an intermittent-duty motor is designed for shorter bursts of operation. Select your motor based on your application’s duty cycle to avoid unnecessary overheating or motor failure.
Tuning Servo Motor Systems
The Importance of Servo Tuning
Proper tuning of a servo motor system is necessary to achieve desired performance characteristics such as minimal position error, high responsiveness, and stability. Typically, servo tuning involves adjusting the following gains:
- Proportional Gain (Kp): Affects how forcefully the motor tries to reach the desired position.
- Integral Gain (Ki): Helps to eliminate residual errors over time.
- Derivative Gain (Kd): Used to reduce overshoot and dampen oscillations.
Many servo systems come with auto-tuning software that simplifies this process, making it accessible for beginners or those without extensive engineering experience.
Choosing the Right Feedback Device
Servo motors utilize feedback devices such as encoders or resolvers to provide information about the motor’s position and speed.
- Encoders: Provide digital feedback and are commonly used in applications where high precision is required.
- Resolvers: Are more robust and can operate in extreme conditions but may provide less precision compared to encoders.
Choose a feedback device based on the environmental conditions of your application and the level of accuracy needed.
Position Error Considerations
Servo motors operate by minimizing position error, which is the difference between the commanded position and the actual position. This requires continuous feedback and adjustment of motor parameters to align with real-time demands.
“In high-precision applications, minimizing position error is crucial for ensuring consistent product quality and performance.”
Conclusion
Selecting the right servo motor is essential for achieving optimal performance in any automation or control system. By considering factors such as torque, speed, inertia, and control requirements, you can make informed choices that lead to a more efficient and reliable system. Whether you are working on a robotic arm, a conveyor system, or a medical device, the right motor can make all the difference.
For expert guidance on choosing the perfect servo motor and to explore a wide variety of models, visit our Servo Motor Store. Our inventory includes models that meet diverse industrial and commercial requirements, and we offer both AC and DC servo motors for your specific needs.
FAQs
1. What is the difference between AC and DC servo motors?
AC servo motors are generally more efficient for high-power applications, have a wider speed range, and require less maintenance compared to DC servo motors, which are usually more affordable.
2. How do I determine the right torque for my servo motor?
You need to consider both continuous torque and peak torque. Calculate based on the load’s weight, radius, and any friction components in your setup.
3. What role does inertia play in selecting a servo motor?
Inertia matching between the motor and the load is crucial for stability. An incorrect inertia ratio can cause oscillations and reduce control accuracy.
4. Is it necessary to use a gear reducer with a servo motor?
Using a gear reducer can help manage the load more effectively, especially in applications that require high torque at lower speeds.
5. How do I tune a servo motor?
Servo motors can be tuned using Proportional, Integral, and Derivative gains to achieve desired performance. Some systems also provide auto-tuning software to simplify this process.
6. What feedback device should I use with my servo motor?
Choose an encoder for high precision or a resolver for extreme environmental conditions. Both provide essential data for adjusting motor output in a closed-loop system.