How to Choose My Servo Motor: A Comprehensive Guide
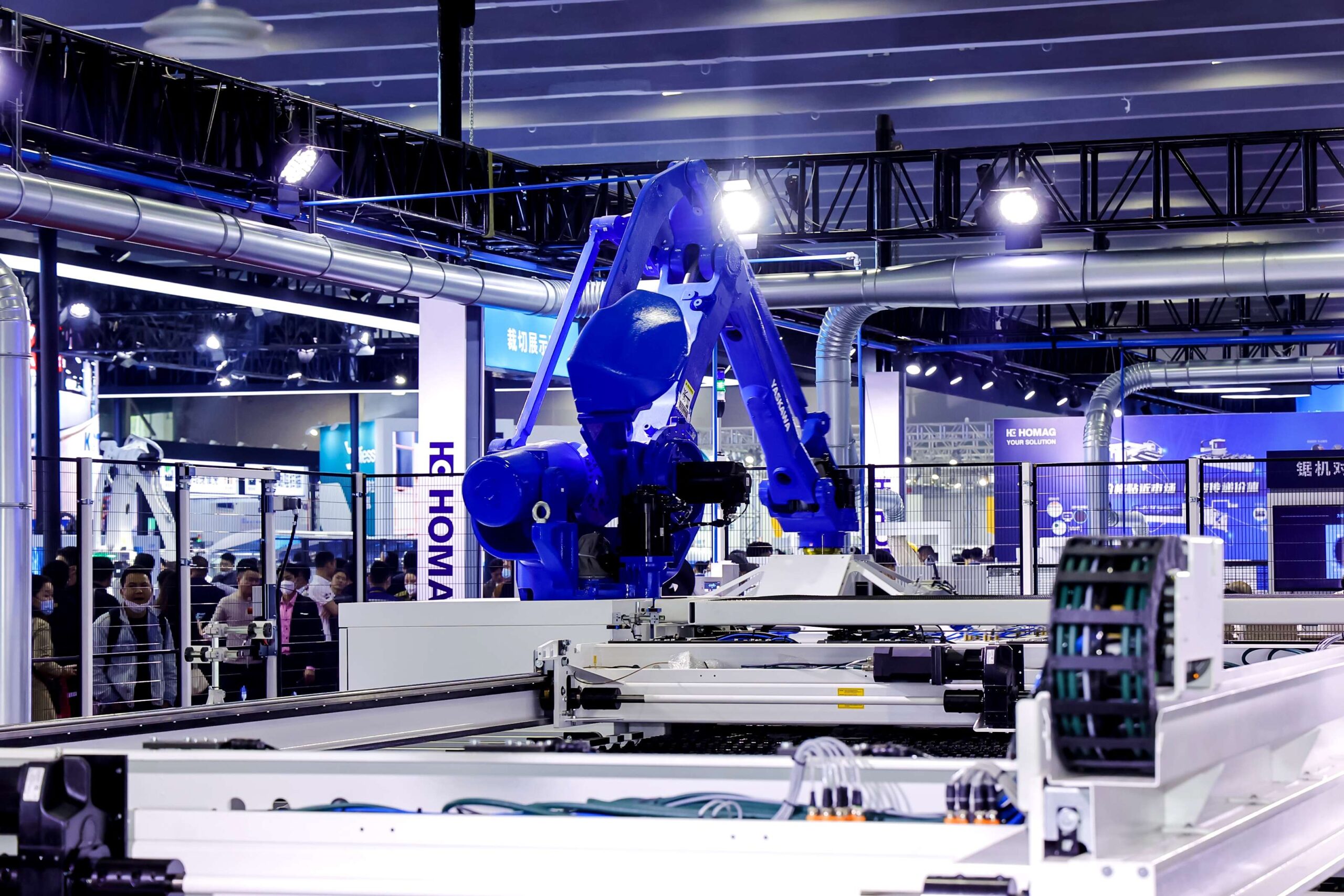
Servo motors are a fundamental part of automation and motion control systems. Choosing the right servo motor for your project is crucial for optimal performance and long-term reliability. In this guide, we will delve into the step-by-step process of how to choose my servo motor, covering everything from determining your load requirements to evaluating the inertia ratio and control systems.
Step 1: Define Your Application Requirements
Before choosing a servo motor, it’s crucial to understand the requirements of your project. Different applications have different demands, and you need a motor that matches those specifications perfectly.
Identify the Load Characteristics
- Load Weight: The total weight of the load your motor will need to move.
- Load Type: Is the load static or dynamic? For instance, in robotic arms, the load may change depending on the task being performed.
- Torque and Speed Requirements: Calculate the torque required to move the load and the speed at which the load needs to move.
Determine Torque Requirements
The amount of torque required is critical when choosing a servo motor. Torque can be categorized as:
- Continuous Torque: This is the amount of torque required to maintain a constant speed.
- Peak Torque: This is the torque needed for short bursts, like during acceleration.
To determine the right motor for your torque requirements, use formulas like:
Torque = Force x Distance
Choose the Motor Size Based on Speed
The speed requirements depend on how fast you need your application to move. Servo motors come in various power ratings that can meet different speed requirements, so it’s crucial to match the motor’s speed capabilities to your system’s needs.
Step 2: Evaluate the Inertia Ratio
Inertia matching is a critical factor in selecting a servo motor. Inertia is the property of an object that resists changes in its state of motion. The inertia ratio is the ratio of the load inertia to the motor inertia, and it should ideally be between 1:1 and 5:1 for most applications.
Importance of Inertia Matching
- Lower Inertia Ratio: Results in smoother performance, but may increase the size and cost of the motor.
- Higher Inertia Ratio: Can lead to oscillations and may require more precise control adjustments.
An optimized inertia ratio ensures that the motor can handle the load efficiently and without excessive wear on the system.
Pro Tip: To improve inertia matching, consider adding a gearbox to reduce the load’s reflected inertia.
Step 3: Select the Drive System
A servo motor needs a drive system to interpret signals from the control system and convert them into actual movement. Selecting the right drive depends on your control system and application requirements.
Types of Drive Systems
- Analog Drives: Suitable for simple applications where you need basic control over speed and torque.
- Digital Drives: Allow more flexibility and precise control, and come with features like auto-tuning and position memory.
For best performance, it is essential to pair the servo motor with a suitable drive system, ensuring compatibility with control signals and power supply requirements.
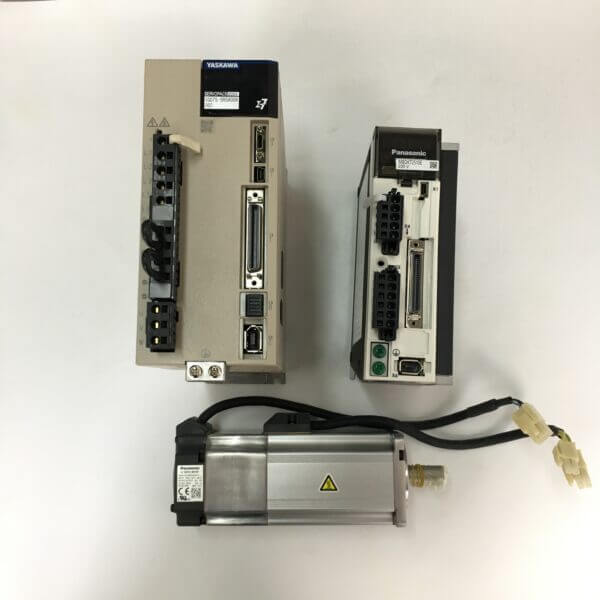
Step 4: Gear Selection
Gears can dramatically affect how your servo motor performs. The gear ratio helps adapt the motor’s output to the application by increasing torque or reducing speed.
Types of Gears
- Spur Gears: Common and suitable for lower load applications.
- Planetary Gears: More robust, and used for high-torque applications.
By using a gearbox, you can reduce the size of the servo motor without compromising on torque or speed. This makes it ideal for applications where space is limited, or the load requires more torque than a standard motor can provide.
Step 5: Control System Considerations
Servo motors require precise control to operate effectively. There are different types of control systems used for servo motors, such as position control, velocity control, and torque control.
Choosing the Right Control System
- Position Control: Ideal for applications like CNC machines and robotics where accurate positioning is essential.
- Velocity Control: Used when maintaining a specific speed is important, such as in conveyor systems.
- Torque Control: This type of control is used in applications that need constant torque, like winding machines.
The right control system allows you to optimize the motor’s operation to meet the unique requirements of your application.
Step 6: Power Supply and Current Requirements
Your servo motor will need the right power supply to function correctly. It’s important to determine both the voltage and current requirements before selecting your motor.
Voltage and Current
- Voltage Rating: Ensure the motor’s voltage rating matches the power supply available. Using incorrect voltage may damage the motor or reduce efficiency.
- Current Requirements: Peak and continuous current ratings need to be matched to your motor’s requirements to prevent overheating and ensure optimal performance.
Note: Servo motors with higher continuous torque generally require more current, so make sure your power source is capable of supplying it without fluctuations.
Step 7: Environmental Factors
Environmental conditions play an essential role in the longevity and performance of a servo motor.
Temperature and Humidity
- Operating Temperature: The motor’s operating temperature should be within the limits specified by the manufacturer to prevent overheating and potential damage.
- Humidity: High humidity levels can affect electrical components and lead to short circuits or insulation failures.
Ensure that the motor you select has the appropriate IP rating for your environmental needs.
Step 8: Mounting and Space Constraints
Space limitations can significantly affect the selection of a servo motor. Some motors are bulky and require more room for mounting, so you must consider:
- Motor Dimensions: Check the physical dimensions of the motor against the available space in your setup.
- Mounting Orientation: Some applications require specific motor orientations, so ensure that the selected motor fits your installation requirements.
Step 9: Budget Considerations
The cost of a servo motor depends on various factors, including torque rating, power, drive type, and additional features like feedback. It’s essential to balance cost against the requirements of your application.
Lower-Cost Alternatives
If your application does not need high precision, consider alternatives like stepper motors or brushed DC motors. These can be cost-effective in applications where fine-tuning is not critical.
Conclusion
Selecting the right servo motor is a detailed process that requires careful consideration of torque, speed, control systems, environmental factors, and cost. By following the steps outlined in this guide, you can confidently choose the best servo motor that meets your specific application needs.
Servo motors play an important role in automation, and choosing the right one ensures efficiency, accuracy, and reliability in your projects. If you’re interested in exploring servo motors for your application, check out our Original Panasonic Servo Motor MINAS A5 or browse our full selection at our Servo Motor Store.
FAQs
1. How do I determine the torque needed for my servo motor?
To determine the torque, you need to know the load weight, speed, and distance it will be moved. Calculating Torque = Force x Distance helps in finding the torque requirement.
2. Can I use a servo motor without a gearbox?
Yes, but using a gearbox can improve torque performance and allow the use of a smaller motor in applications that need more torque.
3. How important is inertia matching in servo motor selection?
Inertia matching is critical for efficient performance and smooth motion. A poor inertia ratio can lead to oscillations and increased wear on the system.
4. What control mode should I choose for a robotic application?
For robotics, position control is often used as it ensures precise control over movement, essential for tasks like picking and placing.
5. How do I know if the motor is suitable for my environment?
Check the motor’s IP rating for water and dust resistance. Additionally, ensure it can operate within the temperature and humidity conditions of your environment.
6. What should I consider regarding power supply?
Ensure that the power supply matches the voltage and current requirements of the motor, as incorrect values can lead to damage or inefficient operation.
By choosing the right servo motor, you can guarantee enhanced performance and productivity for your application. Remember, investing time in the selection process will lead to improved reliability and efficiency in your automation projects.