How to Choose the Right Servo Motor
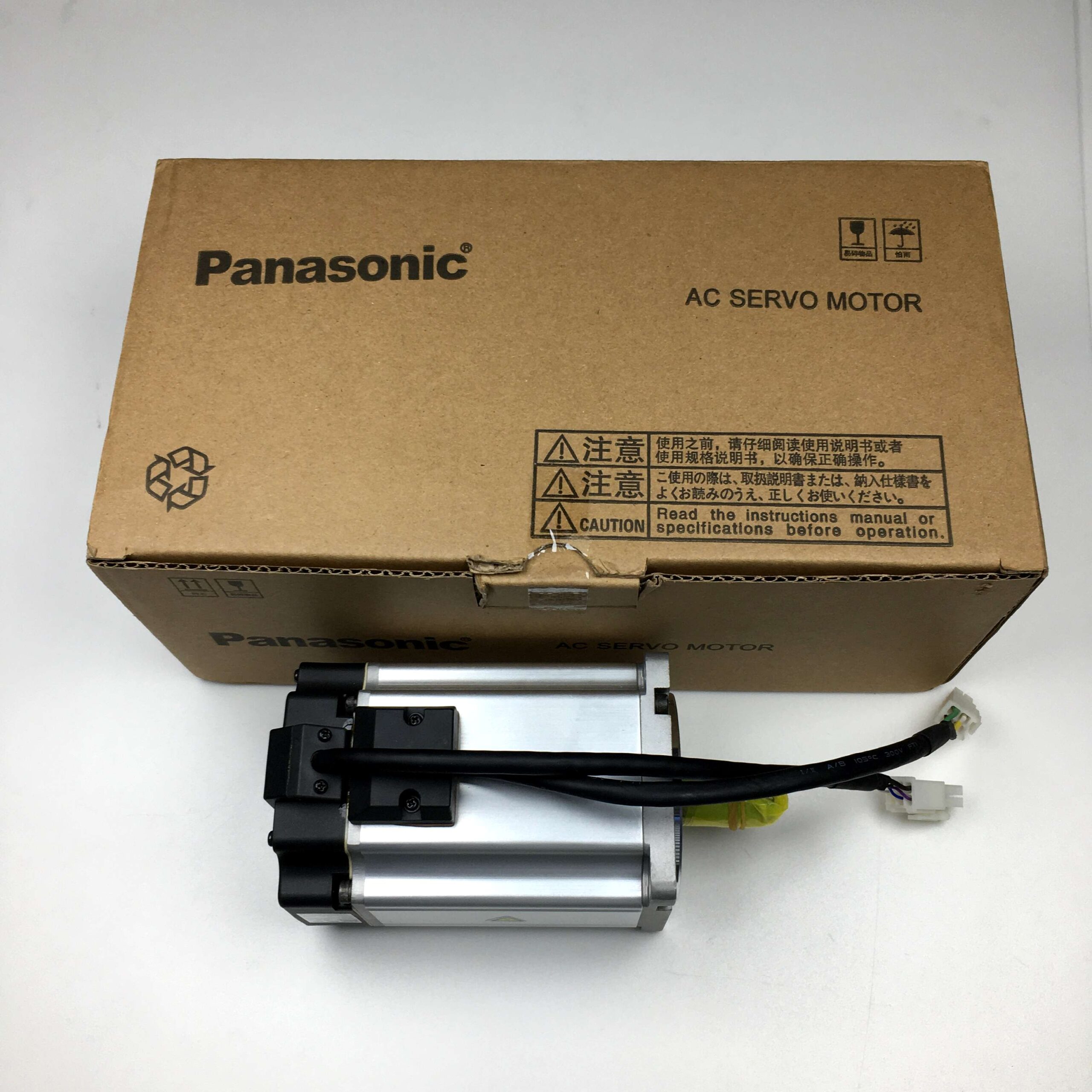
When choosing a servo motor, you want the best solution for your specific application. Servo motors come in many different types and sizes, making it essential to understand your needs and how each option fulfills them. In this guide, we will explore how to select the appropriate servo motor based on a number of critical factors such as torque, speed, inertia, and overall system requirements.
Whether you’re working on a robotics project, an automation system, or CNC machinery, choosing the correct servo motor impacts the system’s performance and reliability. We’ll cover all the main considerations to help you make the right choice.
Understanding Servo Motor Types
AC and DC Servo Motors
Servo motors are generally classified into two types: AC servo motors and DC servo motors. Understanding their differences helps in determining which type suits your requirements.
- AC Servo Motors: These motors are widely used in industrial applications for their efficiency and reliability. AC servo motors can handle higher torque and speed requirements and are typically used in manufacturing and automation systems.
- DC Servo Motors: These motors are more common in smaller-scale applications like robotics. DC servo motors offer good torque control, especially at low speeds, which makes them suitable for precise and small movements.
Tip: The Panasonic Servo Motor MINAS A5 1KW offers excellent performance for medium power applications where accuracy and reliability are essential.
Stepper Motors vs. Servo Motors
Many people wonder whether stepper motors can be used in place of servo motors and vice versa. The two motor types serve distinct purposes, each with unique advantages and limitations.
Feature | Stepper Motor | Servo Motor |
---|---|---|
Control | Open-loop | Closed-loop |
Torque | High at low speed | High across all speeds |
Speed | Limited | Very High |
Efficiency | Lower | High |
Servo motors are generally superior to stepper motors in applications where high speed, precision, and torque are required. Stepper motors are simpler but often lack the adaptability needed for dynamic environments.
Factors to Consider When Selecting a Servo Motor
1. Load and Inertia Requirements
Servo motors are often chosen based on the load they will be driving. The load inertia must be carefully matched to the motor to ensure stable and responsive control. The inertia ratio between the load and the motor should ideally be below 10:1 for stable operation.
When the load’s inertia is too high compared to the motor’s, the control system can become unstable, leading to erratic movements and poor accuracy.
- High Inertia Ratios: For situations with a high load inertia, consider using a gearbox with the servo motor. A gearbox can help reduce the inertia seen by the motor and improve performance.
For high-torque applications, the Yaskawa Servo Motor SGD7S is an excellent choice due to its precise control and feedback capabilities.
2. Torque Requirements
Torque is a critical factor when selecting a servo motor. It’s essential to distinguish between continuous torque and peak torque:
- Continuous Torque: This is the amount of torque the motor can provide continuously without overheating. It must meet or exceed the requirements of your system during normal operation.
- Peak Torque: This is the maximum torque the motor can provide for a short period, often during acceleration or sudden changes in load.
Ensure your servo motor can handle both the continuous and peak torque demands of your application.
3. Speed Requirements
Speed is another key factor. Servo motors can operate at a wide range of speeds, typically from a few RPMs to thousands of RPMs. Identify the speed required for your application:
- For high-speed manufacturing or conveyor systems, an AC servo motor with a higher speed range may be needed.
- For robotic arms or 3D printers, where fine precision and slower speeds are essential, a lower-speed motor with high control accuracy may be preferable.
For systems needing precise speed control, the Panasonic MINAS A5 400W Servo Motor is a solid option with versatile control features.
4. Drive and Control System Compatibility
A servo motor must be paired with the appropriate servo drive. The drive converts the signals from the controller to control the motor effectively. Not all drives are compatible with every motor, so ensure:
- Voltage and Current: The drive must match the voltage and current specifications of the servo motor.
- Control Signals: Compatibility with pulse width modulation (PWM) or other control signal types must be verified.
5. Environmental Conditions
The environment in which the servo motor will operate also impacts the selection. Consider factors such as:
- Temperature: Ensure the motor can handle the ambient temperatures where it will operate.
- Ingress Protection (IP) Rating: For dusty or wet environments, choose a motor with an appropriate IP rating to avoid failures due to contamination.
Torque-Speed Curve Analysis
The torque-speed curve of a servo motor tells you how the motor behaves under different loads and speeds. It’s crucial to evaluate this curve before selecting a motor.
- At low speeds, most servo motors can produce high torque, which is ideal for applications requiring lifting or positioning.
- As the speed increases, the torque typically drops. Be sure to select a motor that can provide sufficient torque at the highest speed required by your application.
Example of Torque-Speed Curve
Below is a sample torque-speed table for a typical AC servo motor:
Speed (RPM) | Torque (Nm) |
---|---|
0-500 | 4.0 |
500-1000 | 3.2 |
1000-1500 | 2.5 |
1500-2000 | 1.8 |
Using this curve, you can understand if the selected motor can maintain the necessary torque throughout your operation.
Load Matching and Application
1. Dynamic vs. Static Loads
Different applications have different load profiles, and it is important to choose a servo motor that can handle these profiles.
- Static Load: These are loads that do not change much over time. Servo motors used in lift mechanisms often deal with static loads.
- Dynamic Load: Applications like robotic arms experience constant changes in load, which demands fast response times and accurate control.
2. Selecting Based on Application
- Robotic Arms: Require a servo motor that can provide precise movements and maintain torque across varying loads. DC servo motors are often used here.
- CNC Machines: Need a high-torque motor that can work accurately across high speeds. AC servo motors are typically a better choice for these tasks.
- Conveyors: Should use a motor that can run continuously and efficiently at higher speeds.
Need a motor for a conveyor? Check out the Panasonic MINAS A6 2kW for robust and efficient operation in automation environments.
FAQs
1. How do I choose between an AC and a DC servo motor?
AC servo motors are generally more robust and suitable for industrial applications with high torque and speed needs, while DC servo motors are better for low-power, precise control applications like robotics.
2. What is a torque-speed curve, and why is it important?
A torque-speed curve is a graph that shows how much torque a motor can deliver at different speeds. It is important for ensuring the motor meets the operational requirements at various load speeds.
3. Can I use a stepper motor instead of a servo motor?
Stepper motors can be used in place of servo motors in some applications, but they lack feedback control, which makes them less suitable for tasks requiring precise movements and load adaptability.
4. What are the most important factors in servo motor selection?
Key factors include torque requirements, speed requirements, drive compatibility, and environmental factors. Ensuring a good match with these criteria helps in selecting the right motor.
5. Do servo motors require a specific type of drive?
Yes, each servo motor must be paired with a compatible drive that matches its voltage, current, and control needs.
6. How do environmental conditions affect servo motor performance?
Environmental factors such as temperature, dust, and moisture can impact motor performance. Selecting a motor with a suitable IP rating ensures it can handle such conditions effectively.
Conclusion
Selecting the right servo motor is critical to the performance of your system. Factors such as torque, speed, inertia matching, drive compatibility, and environmental conditions must all be considered to ensure the motor fits well with your requirements. Understanding the distinctions between AC and DC motors, and the role of stepper motors, will further help in determining the optimal solution.
To choose the perfect servo motor for your needs, always compare the torque-speed curves, assess your system’s load requirements, and consider the environment in which the motor will operate. For expert guidance and a variety of motors to choose from, visit the Servo Motor Store. We provide detailed specifications and expert assistance to help you get the best fit for your project.