How to Control Servo Motor Speed: A Comprehensive Guide
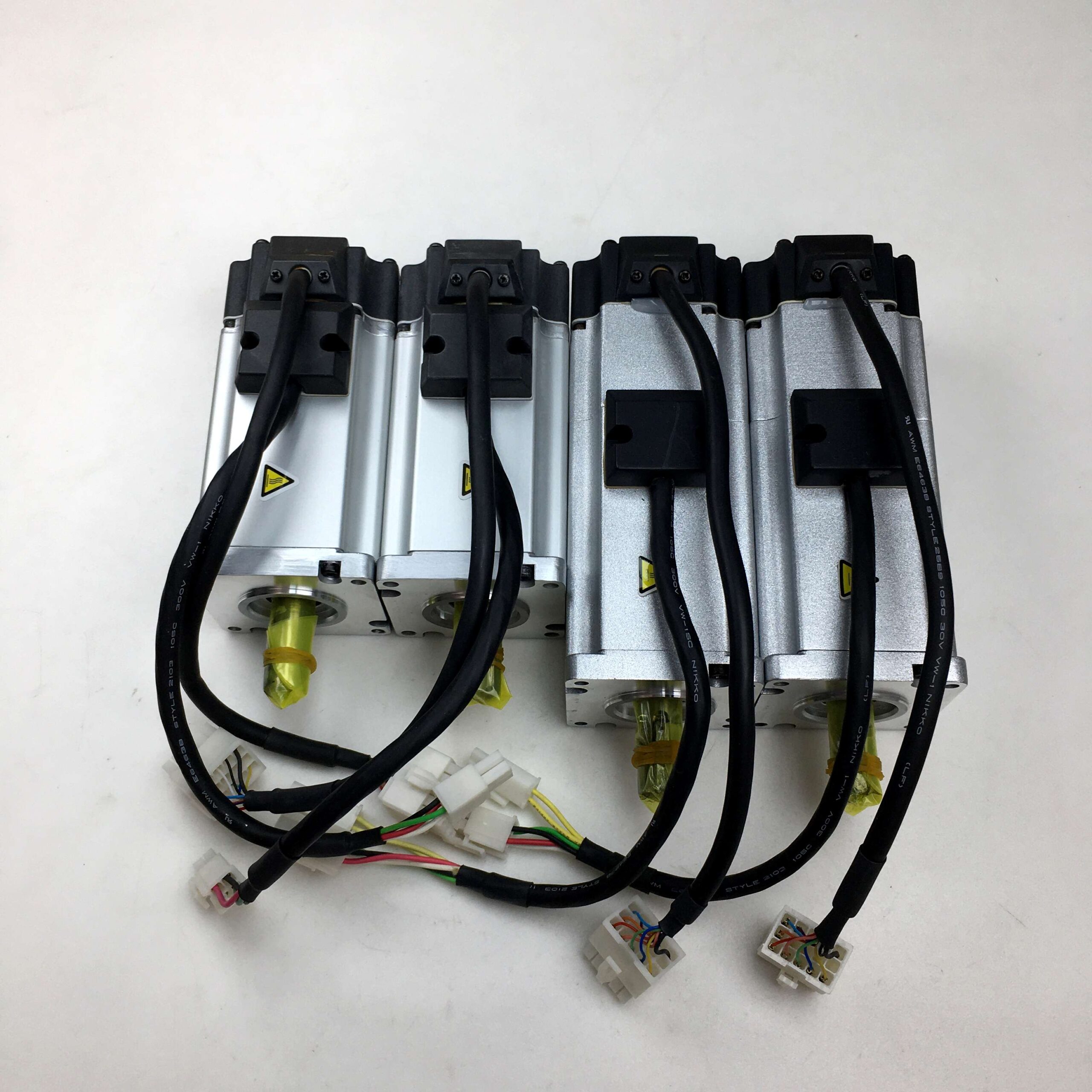
Servo motors are an integral part of various industries, from robotics to manufacturing. Controlling the speed of a servo motor is a fundamental aspect of optimizing its performance for specific applications. In this comprehensive guide, we will cover everything you need to know about how to control servo motor speed effectively. We will discuss key aspects such as speed controllers, techniques, and practical applications.
Techniques to Control Servo Motor Speed
1. Pulse Width Modulation (PWM)
One of the most common techniques for controlling the speed of a servo motor is through Pulse Width Modulation (PWM). PWM is a method used to vary the duty cycle of the input signal, thereby adjusting the amount of power delivered to the motor.
- Duty Cycle: The duty cycle represents the percentage of time the signal is high. By adjusting this percentage, you can control the speed of the motor.
- Frequency Considerations: The frequency of the PWM signal also plays a role in smooth operation. A higher frequency can lead to finer control over the speed.
PWM is particularly effective because it allows the servo motor to operate efficiently without generating too much heat. This makes it ideal for robotic applications that require rapid speed adjustments.
Benefits of PWM:
- Efficient control of motor speed.
- Minimizes energy loss.
- Allows precise control over the motor’s response.
2. Closed-Loop Control Systems
Servo motors are known for their use in closed-loop control systems. In these systems, sensors provide real-time feedback on the motor’s position and speed, which is used to adjust the motor’s operation. This feedback mechanism ensures that the motor maintains a consistent speed even when there are load changes.
“Closed-loop control allows for extremely precise control of servo motor speed and position, making it invaluable in applications such as CNC machinery and automated production lines.”
Closed-loop control systems use proportional-integral-derivative (PID) controllers to maintain the desired speed. Adjusting the proportional gain, integral gain, and derivative gain helps fine-tune the motor’s performance.
Factors to Consider for Speed Control
1. Load and Inertia
The load connected to the servo motor has a significant impact on speed control. Higher load inertia requires the motor to exert more force to accelerate or decelerate, which directly affects speed control.
- Inertia Ratio: To ensure optimal performance, the load-to-motor inertia ratio should ideally be kept below 10:1. This reduces vibrations and improves control accuracy.
- Gear Reduction: Using a gearbox can help manage high inertia by reducing the load seen by the motor, thereby making speed control easier.
If you need a motor suited for applications with higher load inertia, consider our Panasonic Servo Motor MINAS A5 2KW Break.
2. Power Supply Voltage
Power supply voltage is another crucial factor in controlling servo motor speed. The voltage directly affects the motor’s ability to generate torque and, consequently, its speed.
- High Voltage: Higher voltage can lead to higher torque, allowing the motor to accelerate faster.
- Low Voltage: Low voltage will limit the speed, making the motor respond more slowly to changes.
Always choose a power supply that matches the voltage requirements of your servo motor to ensure efficient speed control. For more information, see our detailed servo motor options at the Servo Motor Store.
3. Speed Torque Curves
The speed torque curve of a servo motor indicates how much torque the motor can generate at various speeds. Understanding this curve is essential for determining how fast a motor can go while maintaining sufficient torque for your application.
Speed (RPM) | Torque (Nm) | Application Example |
---|---|---|
0-500 | High | Precision robotic arms |
500-1000 | Moderate | Packaging machines |
1000-3000 | Low | Conveyor belts, rapid sorting |
For instance, applications like conveyor belts require a different combination of speed and torque compared to robotic arms, which need higher torque at lower speeds for precision.
4. External Forces and Environment
The environment where the servo motor operates can impact how you control its speed. Factors such as temperature, dust, and humidity can affect motor efficiency. Motors used in industrial settings may need IP-rated enclosures to protect against dust and moisture.
“When selecting a servo motor for speed control, always consider the environment to ensure reliable performance and minimize downtime.”
Practical Applications of Servo Motor Speed Control
1. Robotics
In robotics, precise speed control is essential for ensuring that robotic arms and end-effectors move accurately and safely. Servo motors are used for everything from controlling the joints of robotic arms to driving mobile robots.
- Pick-and-Place Robots: Speed control allows the robot to pick items at one speed and place them at another, ensuring efficiency.
- Collaborative Robots (Cobots): Cobots require both speed and precision, especially when working alongside humans. Servo motors provide smooth and safe motion control in such scenarios.
2. Conveyor Systems
Conveyor systems use servo motors for smooth operation and material handling. Speed control is critical for adjusting the flow rate of products along the conveyor.
- Variable Speed Drive: Using a servo motor with a variable speed drive allows for real-time adjustment of conveyor speed based on production needs.
- Synchronization: Servo motors are used to synchronize the speed of multiple conveyor belts, which is important in packaging and assembly lines.
For conveyor systems that need high reliability and power, you might consider our Panasonic Servo Motor MINAS A5 400W Break.
Tips for Effective Speed Control
1. Choosing the Right Servo Drive
A servo drive is responsible for converting the command signals into power for the motor. To achieve precise speed control, it is important to select a drive that matches the motor’s specifications:
- Voltage and Current: Ensure the drive can handle the motor’s voltage and current requirements.
- Feedback Compatibility: Check if the drive supports the motor’s feedback type, such as encoder or resolver.
2. PID Tuning for Smooth Operation
Adjusting PID (Proportional, Integral, Derivative) gains is critical for refining speed control. Here’s how each gain affects the servo motor:
- Proportional Gain (Kp): Increases the speed response but too much can lead to oscillations.
- Integral Gain (Ki): Helps in minimizing steady-state error but may slow down the response.
- Derivative Gain (Kd): Reduces overshoot, enhancing stability.
Many servo motor controllers offer auto-tuning features, but manual adjustments are often required for applications needing high precision.
Conclusion
Controlling the speed of a servo motor is a key aspect of getting the most out of your automation and precision systems. By understanding and utilizing techniques like PWM, closed-loop control, and PID tuning, you can achieve the desired speed performance for your specific application. Additionally, considering factors such as inertia, gear ratios, and external environments will help you make informed decisions for motor selection and control strategies.
For a wide range of servo motors and expert advice on which model fits your speed control needs, visit our Servo Motor Store. Our selection includes high-quality motors designed for a variety of industrial applications, providing both efficiency and precision.
FAQs
1. How does Pulse Width Modulation (PWM) control the speed of a servo motor?
PWM controls the speed of a servo motor by adjusting the duty cycle of the input signal, which in turn changes the power supplied to the motor. A higher duty cycle results in a higher speed.
2. What are the benefits of using a closed-loop control system for servo motors?
Closed-loop control systems offer high precision by constantly adjusting the motor’s speed and position based on feedback. This makes them ideal for applications where accuracy is critical.
3. How do you select the right gear ratio for speed control?
The gear ratio should be selected based on the desired balance between speed and torque. A higher gear ratio will reduce speed but increase torque, which can be helpful for handling heavier loads.
4. What is the role of PID tuning in speed control?
PID tuning adjusts the proportional, integral, and derivative gains to achieve a balance between speed response, accuracy, and stability. Proper tuning can significantly improve the performance of a servo motor.
5. Can servo motors be used for continuous speed applications like conveyor belts?
Yes, servo motors are well-suited for continuous speed applications like conveyor belts, especially where precision and the ability to adjust speed dynamically are required.
6. What should be considered when choosing a power supply for a servo motor?
Ensure the power supply voltage matches the motor’s requirements, and that it can provide sufficient current for both the motor’s continuous and peak demands.