How to Control Torque of Servo Motor
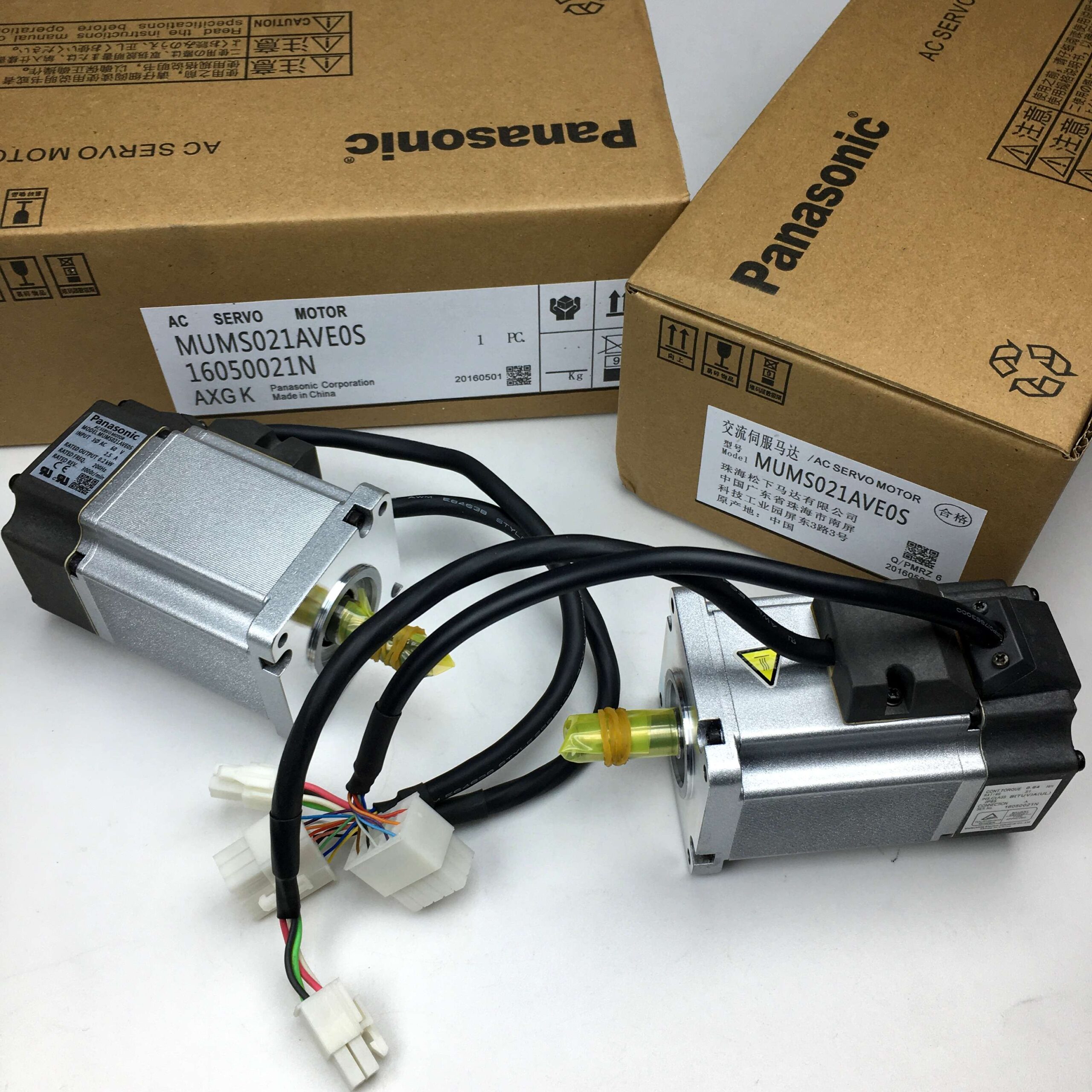
Servo motors are essential in many applications requiring precise motion control, from robotics to automated manufacturing. Understanding how to control the torque of a servo motor is paramount for achieving optimal performance and ensuring the longevity of your equipment. This comprehensive guide will walk you through the intricacies of servo motor torque control, offering practical tips and insights that will empower you to master this crucial aspect of automation. Let’s dive in and unlock the secrets to harnessing the power of your servo motors!
Understanding Servo Motor Torque
Servo motors are electromechanical devices that provide precise control over angular or linear position, velocity, and acceleration. A key characteristic that distinguishes them from other motors is their ability to deliver specific amounts of torque. Torque, in simple terms, is the rotational force produced by the motor. Controlling this force is essential for applications where the motor needs to move a load, maintain a position against resistance, or exert a specific amount of force. The ability to control torque allows for precise movements and ensures that the motor can handle the demands of the application without stalling or overheating.
Why is Torque Control Important?
Torque control is critical in various scenarios. Imagine a robotic arm that needs to pick up an object and place it with precision. How to control the torque of a servo motor will dictate the arm’s ability to grip the object firmly without crushing it, as well as its ability to move the object smoothly and accurately to the desired location. In industrial automation, torque control is essential for tasks such as tightening bolts to a specific torque, controlling the tension of materials in a web handling process, or regulating the force applied by a press. Without precise torque control, these tasks would be difficult, if not impossible, to perform accurately and consistently.
Factors Affecting Servo Motor Torque
Several factors influence the amount of torque a servo motor can produce. These include the motor’s design, size, and the electrical current supplied to it. Larger motors generally have higher torque ratings, as do motors designed with more powerful magnets and windings. The current flowing through the motor’s windings is directly proportional to the torque produced. Therefore, by controlling the current, you can effectively control the torque. Additionally, factors like the motor’s speed and the efficiency of the mechanical components connected to it (e.g., gears, belts) can also impact the available torque.
Methods for Controlling Servo Motor Torque
There are primarily two methods for controlling the torque of a servo motor:
- Current Control: This is the most direct method. As mentioned earlier, the torque produced by a servo motor is directly proportional to the current flowing through its windings. By precisely regulating the current, you can control the torque output. Specialized servo drives are often used for this purpose. These drives can be configured to operate in “torque mode,” where they receive a torque command and adjust the motor current accordingly. For example, the SGD7S-2R8A00A Original Yaskawa Single axis servo driver is well-suited for precise torque control applications.
- Voltage Control (Indirect): While less precise than current control, adjusting the voltage supplied to the servo motor can indirectly influence its torque. This method is often used in simpler, less demanding applications. Reducing the voltage will generally reduce the motor’s speed and, consequently, its maximum available torque. However, this method provides limited control over the actual torque produced and is not suitable for applications requiring high precision.
Implementing a Closed-Loop Torque Control System
For accurate and responsive torque control, a closed-loop system is essential. This involves using a sensor to measure the actual torque being produced by the motor and feeding this information back to the controller. The controller then compares the measured torque to the desired torque and adjusts the motor current accordingly.
Here’s a breakdown of a typical closed-loop torque control system:
- Servo Motor: The heart of the system, responsible for generating the rotational force.
- Servo Drive: A specialized electronic device that regulates the power supplied to the motor. It receives commands from the controller and adjusts the current and voltage to achieve the desired torque.
- Torque Sensor: A transducer that measures the actual torque output of the motor. It provides a feedback signal to the controller.
- Controller: The “brain” of the system. It receives the desired torque command, compares it with the feedback from the torque sensor, and sends appropriate signals to the servo drive. This can be a microcontroller (like an Arduino) or a dedicated motion controller.
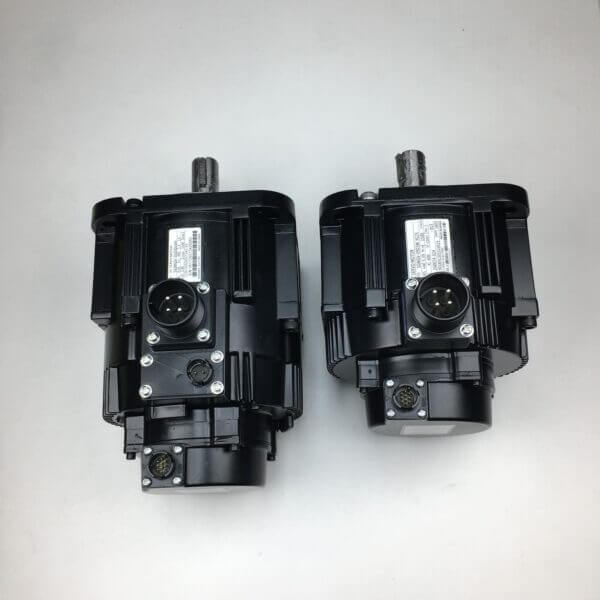
- Feedback Loop: The continuous cycle of measuring the actual torque, comparing it to the desired torque, and adjusting the motor control signals.
Tuning the Torque Control Loop
Achieving optimal performance in a closed-loop torque control system requires careful tuning of the control loop parameters. These parameters, often referred to as gains, determine how the controller responds to the difference between the desired and actual torque.
- Proportional (P) Gain: This determines the immediate response of the controller to the torque error. A higher P gain results in a faster response but can lead to oscillations or overshoot.
- Integral (I) Gain: This helps eliminate steady-state error by accumulating the torque error over time. A higher I gain reduces steady-state error but can also contribute to instability if set too high.
- Derivative (D) Gain: This anticipates future torque errors based on the rate of change of the current error. It helps dampen oscillations and improve stability.
Tuning these parameters is often an iterative process. You’ll need to experiment with different values to find the optimal settings for your specific application. There are systematic methods for tuning, such as the Ziegler-Nichols method, but they often require fine-tuning through trial and error.
Practical Considerations for Torque Control
When implementing torque control, several practical aspects need careful consideration:
- Inertia Matching: The inertia of the load connected to the motor should be appropriately matched to the motor’s inertia for optimal control. A significant mismatch can lead to instability or poor performance.
- Gear Ratios: If using a gearbox, the gear ratio will affect the torque and speed at the output shaft. Choose a gear ratio that balances the need for torque amplification with the desired speed range. For high-torque needs, the Original Panasonic Servo Motor MINAS A6 4400w could be an excellent choice with the right gearbox.
- Mechanical Design: The mechanical components connecting the motor to the load should be rigid and free of backlash to ensure accurate torque transmission.
- Safety: Always prioritize safety when working with servo motors. Ensure proper grounding, and use appropriate safety measures to prevent injury or damage to equipment. When using a powerful motor like the Original Panasonic Servo Motor MINAS A6 5KW Break MDMF502L1H6M, extra caution is warranted.
Frequently Asked Questions (FAQs)
1. How can I determine the required torque for my application?
Determining the required torque involves analyzing the load’s inertia, friction, and any external forces acting on it. You’ll need to calculate the torque needed to accelerate the load, overcome friction, and counteract any opposing forces.
2. What is the difference between stall torque and continuous torque?
Stall torque is the maximum torque a motor can produce when its shaft is stationary (stalled). Continuous torque is the torque a motor can sustain indefinitely without overheating. When selecting a motor, ensure that both the stall and continuous torque ratings meet your application’s requirements.
3. Can I use an Arduino to control the torque of a servo motor?
Yes, an Arduino can be used for basic torque control, especially in hobbyist projects. By using pulse width modulation (PWM) signals, you can control the speed and indirectly influence the torque of small servo motors. For more precise control, you can interface the Arduino with a dedicated motor driver and a torque sensor.
4. What are the advantages of using a brushless servo motor for torque control?
Brushless servo motors offer several advantages, including higher efficiency, longer lifespan, less maintenance, and a higher torque-to-inertia ratio compared to brushed motors. These characteristics make them well-suited for demanding torque control applications.
5. How do I protect my servo motor from over-torque conditions?
Many servo drives have built-in over-torque protection features. These features monitor the motor current and shut down the drive if the current exceeds a predefined limit, preventing damage to the motor. Additionally, you can implement software limits in your controller to restrict the maximum torque command sent to the drive.
6. What is the relationship between torque and speed in a servo motor?
Torque and speed are inversely related in a servo motor. At higher speeds, the available torque generally decreases. This relationship is often depicted in a torque-speed curve provided by the motor manufacturer. Understanding this relationship is crucial when selecting a motor for a specific application.
Conclusion
Mastering how to control the torque of a servo motor is a valuable skill for anyone working with precision motion control systems. By understanding the principles of torque control, implementing closed-loop systems, and carefully tuning control parameters, you can achieve accurate and reliable performance in your applications. Remember to consider factors like inertia matching, gear ratios, and safety when designing your system. With the right knowledge and approach, you can harness the full potential of your servo motors and bring your projects to life with precision and power. With this guide, you’re well on your way to becoming a servo motor torque control expert! Remember, the key to success lies in understanding the fundamentals, applying best practices, and never stop learning.