How to Determine the Resistor Needed for a Servo Motor
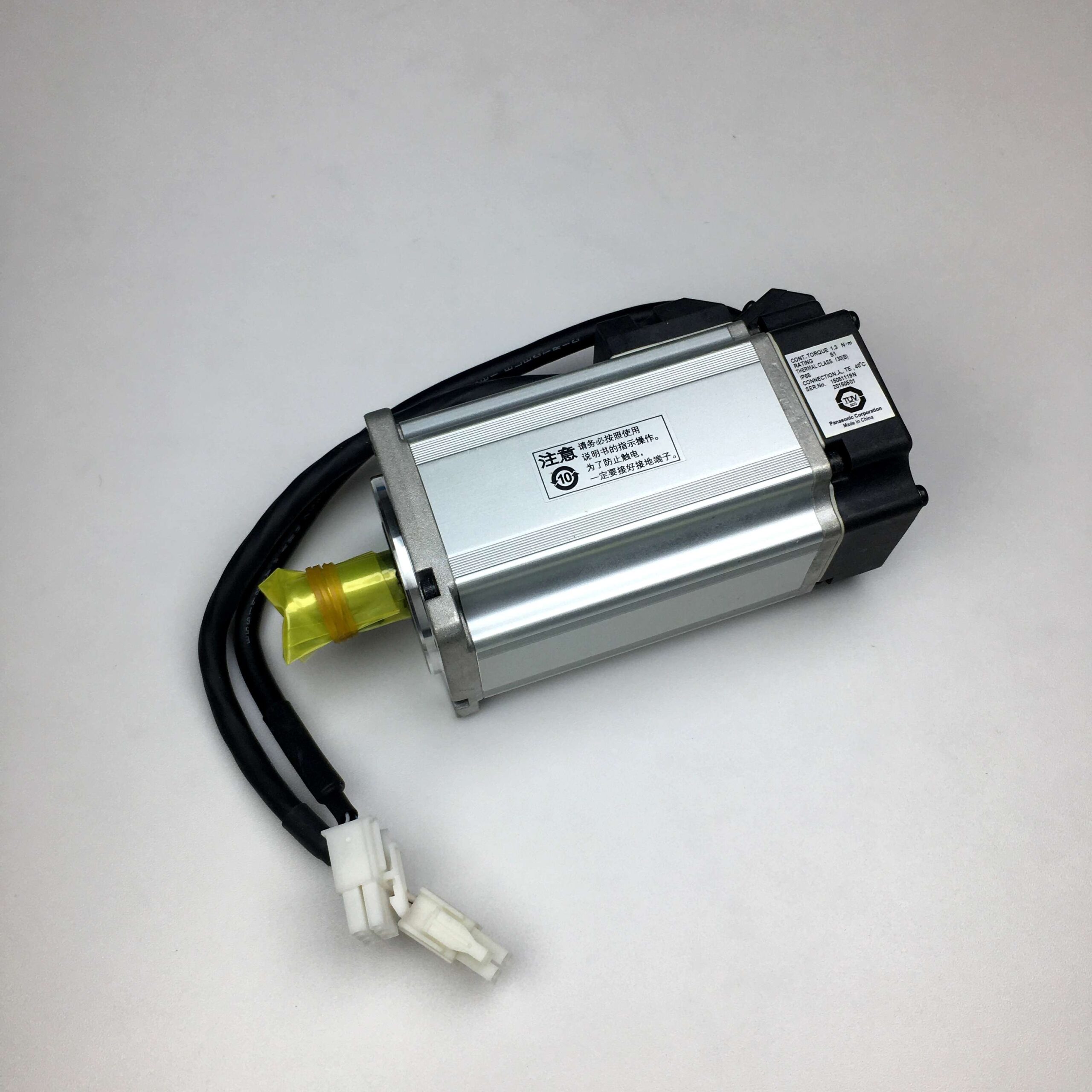
Selecting the correct resistor for a servo motor circuit is a crucial step that ensures proper functioning and helps avoid potential damage to your components. Whether you are working on a robotic arm or an automated system, understanding the electrical requirements is key. This article will walk you through the process of determining the correct resistor value for your servo motor, explaining why it is needed and providing practical guidance to help you make an informed decision.
Why Do Servo Motors Need a Resistor?
The resistor in a servo motor circuit helps control current flow and can also be used for signal conditioning. When using a servo motor, you must take care to ensure that the current does not exceed the motor’s capacity, as too much current can lead to overheating or even burn out. A resistor is used to limit the current and provide appropriate voltage drop.
In some instances, resistors are also used for pull-up or pull-down purposes in the control circuit to ensure the motor receives the correct signals from the microcontroller.
Key Parameters to Consider When Selecting a Resistor
1. Motor Voltage and Current Rating
The voltage and current ratings of the servo motor are the primary parameters to consider when selecting a resistor. You need to ensure that the resistor can handle the maximum current that will pass through it and that it can help manage the voltage according to the motor’s specifications.
- Voltage Rating: Determine the input voltage required by the motor (typically 5V, 12V, or 24V).
- Current Requirement: Check the datasheet of your servo motor for its maximum current rating.
For instance, a Panasonic Servo Motor MINAS A5 might have different current and voltage requirements compared to a smaller, less powerful motor. You can find detailed specifications for Panasonic Servo Motors on our website.
2. Resistor’s Power Rating
The power rating of the resistor is critical because resistors convert electrical energy into heat. To avoid overheating, it is essential to choose a resistor that has a power rating that can handle the expected load. Use the formula:
P = I² * R
Where:
- P = Power in watts
- I = Current in amps
- R = Resistance in ohms
For example, if your servo motor draws 2 A of current, and you are using a 5 ohm resistor:
P = 2² * 5 = 20 W
This means you need a resistor that can handle at least 20 W.
Calculating the Resistor Value for Your Servo Motor
Ohm’s Law for Resistor Calculation
To calculate the required resistor value, use Ohm’s Law:
V = I * R
Where:
- V is the voltage drop across the resistor.
- I is the current flowing through the circuit.
- R is the resistance in ohms.
Rearrange the formula to solve for R:
R = V / I
For example, if your servo motor operates at 6V and draws 1.5 A of current, and you need to reduce the voltage by 3V:
R = 3V / 1.5A = 2 ohms
Ensure you choose a resistor that can handle the power dissipated, which can be calculated as shown earlier.
Series and Parallel Configurations
If the required resistance is not available as a single resistor, you can achieve the desired resistance value by using series or parallel resistor combinations.
- Series Combination: Adding resistors in series results in a higher overall resistance value.
- Parallel Combination: Placing resistors in parallel will decrease the total resistance and is useful if you need a lower value.
Configuration Type | Total Resistance Formula |
---|---|
Series | R_total = R1 + R2 + R3 + … + Rn |
Parallel | 1/R_total = 1/R1 + 1/R2 + … + 1/Rn |
Practical Example
Let’s say you have a Panasonic Servo Motor MINAS A5 400W with a maximum current draw of 3 A and a 12V supply voltage. If you want to limit the current to 2 A, you need a resistor that drops 4V at 2 A:
R = 4V / 2A = 2 ohms
The power dissipated by the resistor would be:
P = I² * R = 2² * 2 = 8 W
You should select a 2-ohm resistor with a power rating of at least 10W to ensure safety.
For more information on suitable servo motors, check out our Panasonic Servo Motor MINAS A5 400W.
Additional Factors to Keep in Mind
1. Tolerance of the Resistor
Tolerance indicates how close the actual resistance value is to the stated value. For precise applications, select resistors with lower tolerance values (e.g., 1% or 2%). Servo motors used in robotics or CNC machines require consistent and precise current control, making low-tolerance resistors an ideal choice.
2. Temperature Coefficient
Resistors have a temperature coefficient, which defines how much their resistance changes with temperature. For applications involving continuous operation or high power, choose resistors with a low temperature coefficient to ensure stability.
3. Type of Resistor
There are several types of resistors you can use in your servo motor circuit, including carbon film, metal oxide, and wire-wound resistors. Wire-wound resistors are often used for high-power applications because of their ability to handle large currents and dissipate heat effectively.
4. Safety Considerations
Always prioritize safety when designing your servo motor circuit. Incorrect resistor values can lead to excessive heat build-up, which can cause component failure or fire hazards. It is good practice to use a heat sink with high-power resistors to dissipate excess heat.
Additionally, if your servo motor is part of an industrial system, consider integrating a fuse in series with the motor to protect against accidental current surges.
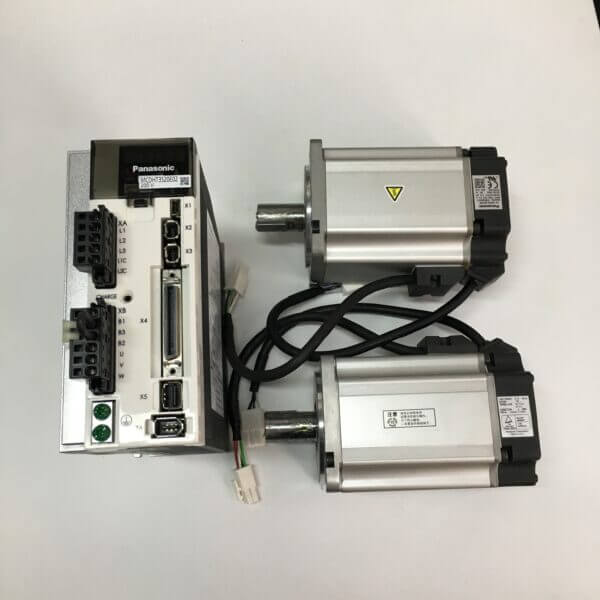
Summary
Determining the correct resistor for your servo motor is all about understanding your motor’s specifications and using Ohm’s Law to calculate the appropriate resistance value. Take into account parameters such as voltage, current rating, power rating, tolerance, and the temperature coefficient to make an informed decision.
Whether you’re controlling a robotic arm or powering an industrial servo system, selecting the right resistor ensures safe and efficient operation of your servo motor. Always remember to consider the resistor’s power rating and take necessary safety precautions when building your circuit.
For additional support or to explore a variety of servo motors and accessories, visit our Servo Motor Store.
FAQs
1. How do I calculate the correct resistor value for my servo motor?
To calculate the resistor value, use Ohm’s Law: R = V / I, where V is the voltage you want to drop, and I is the current through the resistor.
2. What power rating should my resistor have?
The power rating should be calculated using P = I² * R. Ensure that the power rating of your resistor is higher than the calculated value to prevent overheating.
3. Can I use multiple resistors instead of one?
Yes, you can use resistors in series or parallel to achieve the desired resistance value if you don’t have the exact resistor available.
4. What type of resistor should I use for high-power applications?
For high-power applications, a wire-wound resistor is typically the best choice due to its ability to handle large currents and effectively dissipate heat.
5. Why is resistor tolerance important in servo motor circuits?
Tolerance is important because it indicates the accuracy of the resistor. In precise applications like servo motor control, a lower tolerance ensures better consistency and stable operation.