How to Determine the Servo Motor to Use
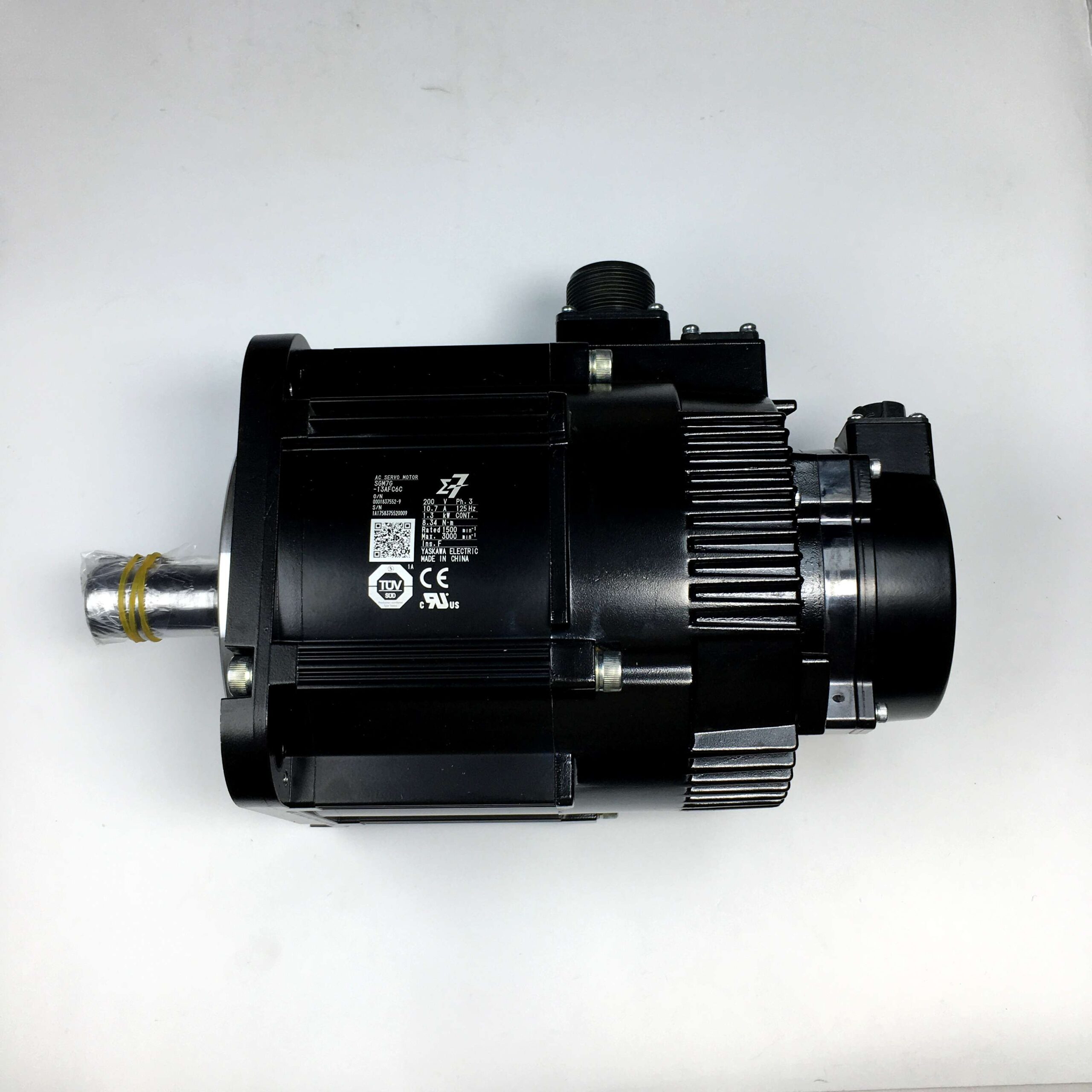
Choosing the right servo motor can be overwhelming, especially when you need the precision and reliability that a complex system demands. Whether it’s for a robotics project, an industrial application, or an RC plane, selecting the correct servo motor is crucial for achieving the desired performance. In this comprehensive guide, we will help you determine the ideal servo motor to use for your specific application, covering everything from torque to inertia ratios.
Servo motors play a pivotal role in automation and robotics, and understanding how to pick the right one can make all the difference in terms of efficiency, cost, and operational success.
Understanding the Basics of Servo Motors
What Is a Servo Motor?
A servo motor is a type of motor equipped with a feedback mechanism. It is designed to accurately control angular or linear position, velocity, and acceleration. Servo motors are widely used in robotics, CNC machinery, and other automated systems due to their ability to provide highly precise movements.
- Closed-Loop System: Servo motors operate with feedback systems, typically either rotary encoders or potentiometers. This feedback ensures that the motor’s position and speed can be continuously adjusted and maintained.
- Rotary vs. Linear: Servo motors are available in both rotary and linear versions, and the choice depends on your specific application requirements. For example, industrial robots often use rotary servos, while CNC machines may use linear versions for precision.
The feedback mechanism makes servo motors distinct from conventional motors, providing them with the ability to self-correct errors and maintain exact control over movement.
For more detailed information, check out our range of Panasonic Servo Motors designed for precise applications.
Key Considerations When Choosing a Servo Motor
1. Understanding Torque Requirements
Torque is a critical factor when determining the right servo motor. Torque refers to the rotational force the motor is capable of producing, which is necessary to move the attached load efficiently.
- Load Characteristics: First, determine the nature of the load. Is it heavy, light, or variable? Heavy loads require motors with higher torque.
- Speed-Torque Curve: Servo motors are characterized by a speed-torque curve. At lower speeds, higher torque is achievable, but as the speed increases, the torque usually decreases. Understanding these dynamics is vital to match the right motor to your application.
Typical Torque Guidelines:
Application Type | Torque Needed | Notes |
---|---|---|
Robotics Arm | Medium to High Torque | Depends on the payload |
Conveyor Systems | High Torque | For heavy, continuous loads |
CNC Machines | Low to Medium Torque | Focus on precise control |
Ensure you select a servo motor with adequate torque for your application’s needs, as this will prevent motor overheating and failure. Torque requirements are essential in deciding between digital and analog servos as well.
For higher torque demands, the Yaskawa Single Axis Servo Motor is a great option for robust industrial usage.
2. Speed and Acceleration Needs
Another important criterion is the speed of the motor, which refers to how quickly it can achieve a particular position.
- Speed Ratings: The speed of a servo motor is measured in degrees per second or rotations per minute (RPM). The application will determine the motor speed required.
- Balancing Speed with Torque: Often, higher speed is accompanied by reduced torque. Therefore, you need to balance speed with the torque output to meet your functional requirements.
Considerations for Speed:
- For robotic arms that need to perform quick, repetitive tasks, a high-speed motor is essential.
- CNC applications, on the other hand, typically favor a slower motor to ensure precision.
If your application involves quick changes or repetitive motions, you might want to consider pulse-width modulation (PWM) to optimize the speed-to-torque ratio.
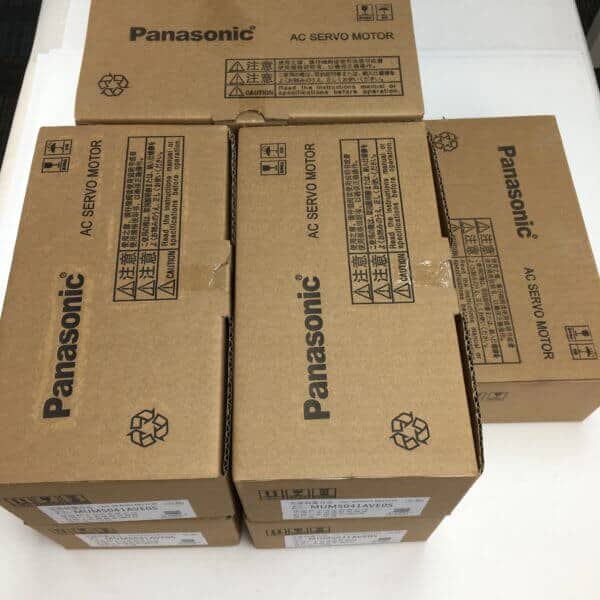
3. Load Inertia Ratio
The load-to-motor inertia ratio is another crucial parameter. It affects how well the motor can control the load without overshooting or oscillating.
- Ideal Ratio: The general rule of thumb is to maintain a load-to-motor inertia ratio between 1:1 and 5:1. Ratios higher than this may lead to instability, where the motor finds it difficult to control the load smoothly.
- Acceleration/Deceleration: If the motor must frequently accelerate and decelerate, a lower inertia ratio is ideal to prevent damage or inefficiency.
Check out our Panasonic MINAS A5 Servo Motor for an example of a motor with excellent control capabilities for varying load inertias.
4. Electrical Requirements and System Compatibility
Electrical compatibility is essential to ensure smooth operation.
- Voltage and Current: Make sure the voltage rating matches your power supply. Servo motors generally operate at 5V, 12V, or 24V. Using the wrong voltage can cause the motor to either underperform or burn out.
- Pulse Width Modulation (PWM): PWM control signals are used in servo motors to control their speed and position. Ensure that the motor driver/controller is compatible with your chosen servo motor’s PWM requirements.
5. Type of Application and Environment
The environment in which the motor will be used also plays a key role in the selection process.
- Industrial Automation: Applications in industrial environments often have higher torque, more stringent accuracy requirements, and possibly exposure to harsh conditions. Motors should be dustproof or waterproof, if necessary.
- Outdoor Applications: If used outdoors, choose a motor that can handle varying temperatures and is resistant to moisture.
6. Motor Size and Dimensions
The physical size of the servo motor must fit within the space available in your system. Small servos are ideal for light robotic applications, while larger motors are better for demanding industrial applications.
- Weight Considerations: Remember that larger motors weigh more, which may affect the design and efficiency of portable or airborne systems.
- Mounting Options: Consider if the motor offers the appropriate mounting configurations for your application (e.g., flange mounts or foot mounts).
Digital vs. Analog Servo Motors
Choosing between a digital or an analog servo motor depends on the level of precision and speed required.
Digital Servos
- High Precision and Speed: Digital servos operate with much higher signal frequency, allowing them to respond faster and hold positions more precisely.
- Higher Cost: They are generally more expensive than analog servos.
Best for: Applications requiring high responsiveness, such as industrial automation or high-performance robotics.
Analog Servos
- Basic Control: Analog servos are controlled by a signal sent 50 times per second. This slower response may lead to a slight lag.
- Cost-Effective: They are cheaper and ideal for less demanding applications.
Best for: Simple, less demanding tasks like controlling the ailerons of an RC plane or performing basic automation tasks.
Comparison Table
Feature | Digital Servo | Analog Servo |
---|---|---|
Signal Frequency | 300 Hz+ | 50 Hz |
Responsiveness | High | Moderate |
Power Consumption | Higher | Lower |
Cost | Expensive | Affordable |
Calculating Torque Requirements for Servo Motors
Proper torque calculation is fundamental to choosing a suitable servo motor. Here’s how you can estimate the required torque:
- Determine Load Weight: Find out the total weight the motor will move.
- Calculate Radius: Measure the distance from the center of the servo to where the load is applied.
- Use the Torque Formula: Torque (Nm) = Force (N) x Radius (m)
For example, if you have a 10 kg load and need to rotate it at a distance of 0.2 m, you would calculate:
Torque = 10 kg x 9.81 m/s² x 0.2 m = 19.62 Nm
Ensure to factor in additional torque if the load is subjected to vibration or shock.
FAQs
1. How do I calculate the right servo motor size?
To calculate the right servo motor size, determine your torque requirements, load weight, speed, and inertia. Properly evaluate each of these criteria to find the best fit.
2. Can I use an analog servo motor for industrial applications?
Yes, but it is generally not recommended due to their slower response rate and lower accuracy compared to digital servos.
3. What is the difference between peak and continuous torque?
Continuous torque is the maximum torque a servo motor can provide for a prolonged period without overheating, while peak torque is the short-term maximum torque output.
4. How do I choose between metal and plastic gears?
Metal gears are more durable and ideal for high-stress applications, while plastic gears are suitable for lightweight, less demanding uses.
5. Is it possible to change the servo motor after installation?
Yes, but you must ensure that the replacement motor matches the original motor’s specifications in terms of voltage, torque, and speed.
Conclusion
Selecting the right servo motor involves understanding your application’s requirements thoroughly—from torque and speed to inertia and environmental factors. Whether you need a digital servo for a high-precision task or an analog servo for a simple automation project, understanding these parameters will guide you to the perfect choice.
Don’t forget to evaluate your electrical system compatibility and environment to choose a motor that ensures long-term reliability and efficiency. If you need more guidance, feel free to browse our range of high-quality servo motors to find the best fit for your needs.