How to Troubleshoot a Servo Motor
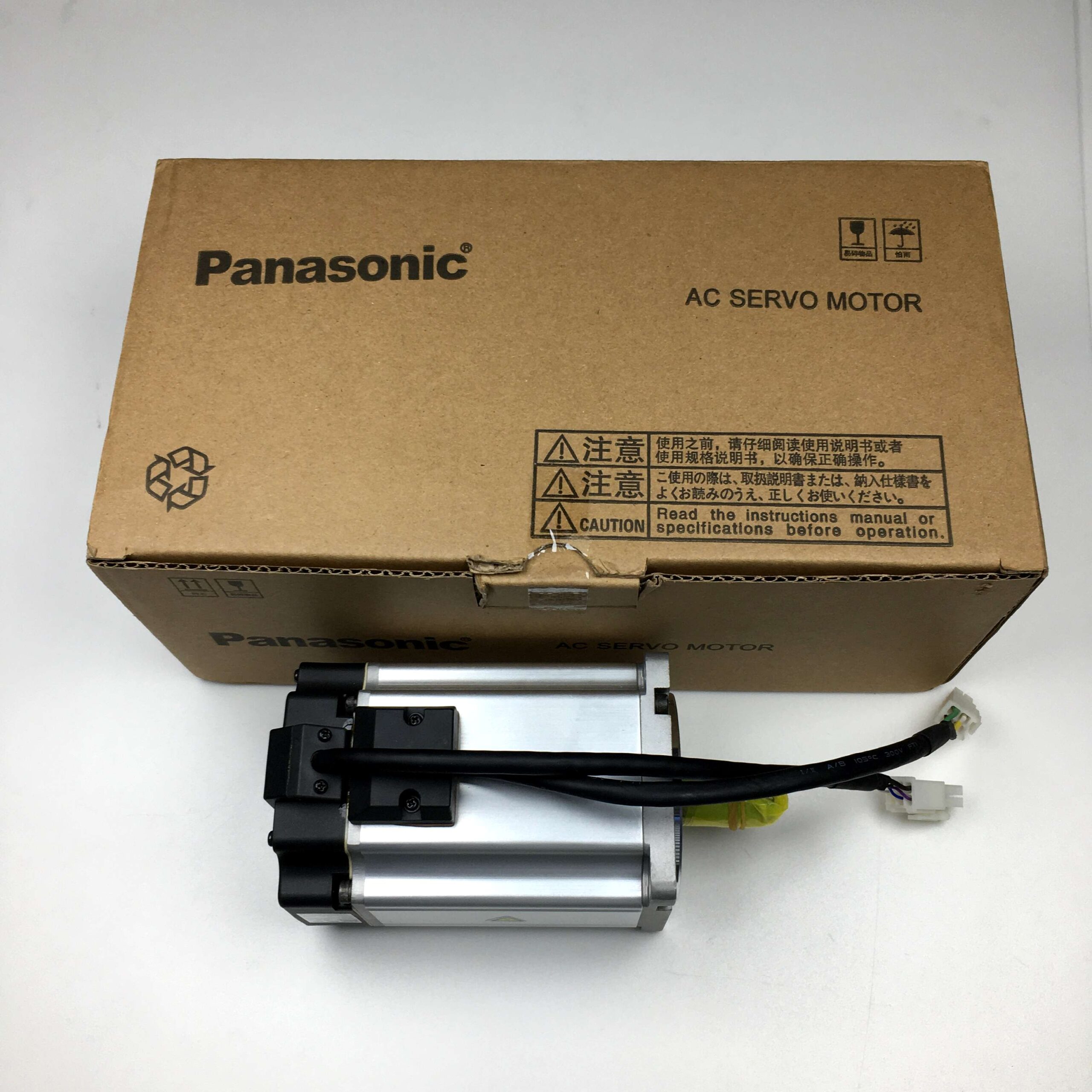
Servo motors are essential components in modern industrial automation, known for their precision, control, and versatility. However, like all machinery, they can face issues from time to time. This guide will walk you through troubleshooting a servo motor effectively. You’ll learn to identify and address common problems, ensuring your system’s smooth and reliable operation. Whether you’re dealing with motor failure, electronic component fatigue, or mechanical faults, understanding how to diagnose and correct these issues is crucial.
Common Issues in Servo Motors
Servo motors, like any machine, can experience a range of problems, often due to component wear, setup issues, or environmental conditions. Here are some common problems that users may encounter:
- Motor Overheating: Overheating can occur due to insufficient cooling or excessive loading. When the motor operates above its rated temperature, it can lead to damage of bearings, windings, and other components.
- Faulty Feedback Systems: The encoder or resolver provides critical positioning information. If these components fail, the motor may operate incorrectly, leading to erratic motor behavior.
- Bearing Failures: Bearings are crucial in reducing friction and enabling smooth operation. Excessive wear and tear can lead to vibrations, noise, and even complete motor failure.
- Voltage Drops or Electrical Problems: Voltage fluctuations or bad capacitors can disrupt motor operation, potentially triggering alarms or causing the system to shut down unexpectedly.
- Drive Issues: The servo drive controls power to the motor. Problems with the drive can manifest as sudden stops or improper motor response.
For advanced servo motor drives, consider using the SGD7S Yaskawa Servo Driver, which offers robust feedback mechanisms to ensure smooth motor operations.
Step-by-Step Troubleshooting Guide
Step 1: Visual and Physical Inspection
The first step in troubleshooting any servo motor problem is a visual inspection. Look for any visible signs of wear or damage on the motor casing, connections, and cabling.
- Check Connections: Ensure that all cables are securely connected. Loose connections can result in poor signal transmission, leading to performance issues.
- Look for Physical Damage: Check for broken components, wear in bearings, or burn marks on the motor casing, indicating overheating.
- Inspect the Environment: Make sure there are no signs of oil leaks, which could cause contamination of motor parts.
Pictured below is the SGD7S Yaskawa Servo Driver used for troubleshooting high-speed applications:
Step 2: Check the Power Supply
Power supply issues are common in servo motors, particularly in environments with frequent fluctuations or unreliable power sources. Ensure that the voltage supplied matches the motor’s specifications.
- Voltage Levels: Use a multimeter to measure the voltage at the motor terminals. If the voltage is too low, the motor may stall or fail to start.
- Capacitor Health: Faulty capacitors in the power supply can also lead to erratic behavior or reduced motor performance. Replace any capacitor that shows signs of wear or damage.
Step 3: Feedback System Testing
The feedback system is one of the most critical parts of a servo motor. Issues in the encoder can lead to positioning errors and incorrect feedback to the control system.
- Encoder Testing: Use a diagnostic tool to ensure the encoder is working properly. Replace or recalibrate if the readings show discrepancies.
- Check the Feedback Wiring: If the motor’s response is erratic, inspect the wiring for potential short circuits or damaged insulation.
Step 4: Servo Drive Diagnosis
Servo drives are responsible for controlling the motor’s speed, direction, and torque. When troubleshooting:
- Drive Alarms: Check for any alarms indicated on the servo drive. Alarms are often related to overvoltage, overcurrent, or feedback errors.
- Firmware and Parameters: Ensure the drive’s firmware is up to date, and check the parameters are correctly set for the specific motor being used.
For a reliable servo motor and drive package, consider the Original Panasonic Servo Motor MINAS A5 400W, which comes with a compatible drive for seamless integration.
Step 5: Testing for Mechanical Faults
Many issues arise from mechanical wear in the motor bearings or other rotating components.
- Listen for Noise: Excessive noise can indicate bearing problems or imbalance in the rotor.
- Check Bearing Health: Use a vibration analyzer to detect any issues with the bearings. High levels of vibration usually mean the bearings are worn and need replacing.
Step 6: Overheating Solutions
Overheating is one of the primary reasons for servo motor failure. If overheating is detected:
- Cooling System: Ensure the motor has adequate cooling—this could involve adding fans or improving ventilation.
- Reduce Load: Overloading the motor increases temperature. Ensure that the motor is not undersized for its application.
Overheating Cause | Potential Solution |
---|---|
Blocked Ventilation | Clear any obstacles |
Overload | Reassess motor application |
High Ambient Temperature | Add external cooling fans |
Maintaining Your Servo Motor
Proper maintenance can prevent most of the problems mentioned above. Here are some key maintenance tips:
- Regular Inspections: Conduct regular inspections, focusing on connections, motor housing, and cooling components.
- Clean Environment: Keep the motor and its surroundings free of dust and contaminants.
- Parameter Backups: Always keep a backup of the servo motor’s parameter settings. In the case of controller replacement or parameter loss, having these backups will save a lot of time and effort.
FAQs
1. Why is my servo motor overheating?
Overheating can be due to overloading, blocked cooling, or high ambient temperatures. Reduce load or improve cooling to fix this issue.
2. What causes erratic servo motor behavior?
Erratic behavior is often due to faulty encoders, voltage drops, or loose connections. Check these components to identify the issue.
3. How do I reset a servo drive alarm?
Refer to the drive manual for resetting procedures. Most drives will require either a manual reset button or power cycling to clear alarms.
4. What is the best way to maintain servo motor efficiency?
Regular maintenance, proper load management, and ensuring clean operating conditions are essential for maintaining efficiency.
5. How can I detect bearing wear?
Listen for unusual noises or use a vibration analyzer to determine the health of the bearings.
6. Can servo motor parameters be lost?
Yes, servo motor parameters can be lost due to power interruptions or control faults. Keep a backup to ensure you can quickly restore them.
Conclusion
Troubleshooting a servo motor can be complex, but a systematic approach makes it manageable. By conducting regular visual inspections, ensuring stable power supply, and keeping the feedback system in good shape, many issues can be prevented before they cause significant downtime. Properly maintaining the motor’s environment and using reliable components, such as those offered by Servo Motor Store, can help extend the life of your equipment and reduce unexpected failures.
If you’re dealing with servo motor issues and need guidance or parts, don’t hesitate to reach out for expert assistance. Reliable parts and experienced support are key to ensuring your system stays operational and efficient.