How to Tune a Servo Motor?
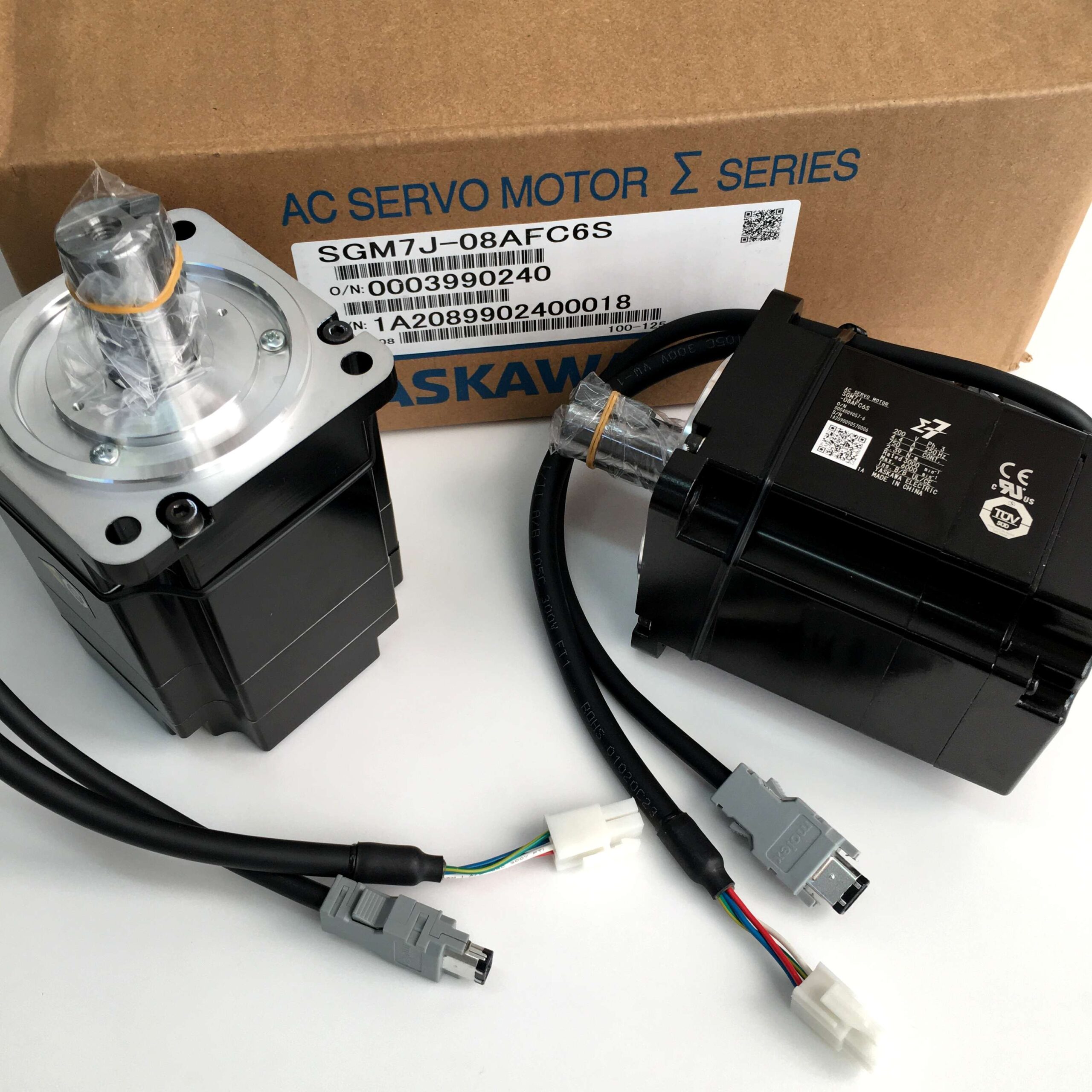
Servo motor tuning is a crucial aspect of ensuring that your servo system operates smoothly and efficiently. Whether you’re working on robotics, CNC machines, or industrial automation, properly tuning your servo motor helps to achieve the desired precision and response time. In this guide, we’ll break down the steps to tune a servo motor, discuss various tuning parameters, and help you understand what makes a servo system perform at its best.
Key Tuning Parameters Explained
Proportional Gain (Kp)
Proportional Gain adjusts the motor response relative to the position error. A higher proportional gain means the motor reacts more quickly to any deviation from the desired position.
- Too High Kp: Causes the system to become too reactive, leading to oscillations.
- Too Low Kp: Makes the system unresponsive, with slow error correction.
For instance, if a robotic arm overshoots while reaching an object, the Kp might be too high.
Integral Gain (Ki)
Integral Gain helps eliminate steady-state errors by summing up past errors and applying corrections based on accumulated discrepancies.
- Too High Ki: Leads to increasing oscillations and potentially makes the system unstable.
- Too Low Ki: Causes the motor to have a residual error after reaching its position.
Derivative Gain (Kd)
Derivative Gain provides a dampening effect by predicting future errors based on the current rate of change of error. It is often used to counteract the tendencies of high Kp or Ki values.
- Too High Kd: Slows the motor response excessively, resulting in sluggish movements.
- Too Low Kd: Results in insufficient dampening, causing overshoot or oscillations.
Steps to Tune a Servo Motor Manually
Step 1: Set Initial Values
Start by setting Kp, Ki, and Kd to low values. This ensures that you begin with a stable, albeit slow, system.
Step 2: Adjust Proportional Gain (Kp)
Increase Kp gradually until the motor starts to respond adequately to input commands. Stop increasing Kp when the motor begins to oscillate around the target position.
Step 3: Tune Integral Gain (Ki)
After setting Kp, start increasing Ki to eliminate any steady-state error. Watch closely, as increasing Ki too much can lead to instability.
Step 4: Set Derivative Gain (Kd)
If oscillations are observed after tuning Kp and Ki, adjust Kd to dampen the movement. Increase Kd incrementally until the system moves smoothly to the desired position without oscillations.
Tip: Always tune one parameter at a time and observe the impact on the servo system before moving on to the next.
Step 5: Test the System
Perform multiple movements with the servo motor to ensure it reaches the desired position consistently. A properly tuned servo motor should have a minimal position error, quick response, and no overshoot.
Common Servo Tuning Techniques
1. Ziegler-Nichols Method
The Ziegler-Nichols Method is a popular approach to tuning PID controllers. Start by increasing the proportional gain until the system oscillates at a constant amplitude. From here, set Ki and Kd based on predefined ratios.
2. Manual Trial and Error
In simple systems, tuning by manual trial and error can be an effective method. This involves adjusting each parameter while observing the response of the motor until the desired behavior is achieved.
3. Software-Assisted Tuning
Many servo drives come with tuning software that simplifies the tuning process. These tools automatically adjust the gains for optimal performance based on the motor’s response to test commands.
Factors Affecting Servo Tuning
Load Conditions
The load attached to the servo motor directly impacts how well it can be tuned. Heavy or variable loads require specific adjustments to the gains to maintain performance without causing oscillations or delay.
Control System Type
- Closed-loop control systems provide feedback from an encoder or position sensor to correct errors, making tuning more reliable and responsive.
- Open-loop systems rely on predetermined commands without feedback, making accurate tuning more challenging.
For more detailed information on control systems, visit our Servo Motor Store Control System section.
Environmental Factors
Temperature, humidity, and external vibrations can affect how a servo motor performs. These environmental conditions must be considered during tuning to ensure consistent performance.
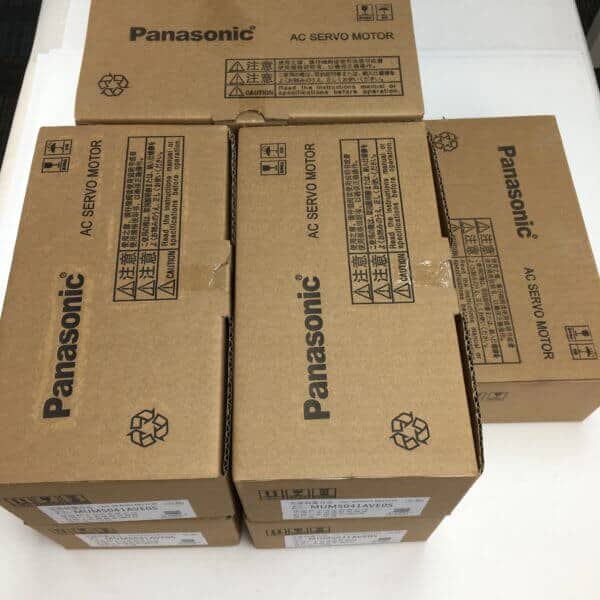
Tools and Software for Servo Tuning
Tuning Software
Modern servo systems often include specialized software that can perform automatic tuning. This software measures the response and adjusts the gains accordingly, providing an optimized setup without extensive manual work.
Oscilloscopes and Signal Analyzers
Oscilloscopes are useful tools for viewing the motor’s response signal in real-time, helping you visualize issues like overshoot, oscillations, or position error.
Manual Tuning vs. Auto Tuning
- Manual Tuning: Provides the highest level of customization, ideal for applications that need precise control and specific performance characteristics.
- Auto Tuning: Offers a more straightforward setup, useful for users without extensive tuning knowledge or for applications where speed is more critical than highly optimized control.
Fine-Tuning for Critically Damped Response
A critically damped system reaches the desired position in the shortest time without overshooting. Achieving this requires careful balance of proportional, integral, and derivative gains.
- Increase Kp until the system begins to oscillate.
- Adjust Kd to dampen the oscillations without significantly reducing speed.
- Set Ki to eliminate any steady-state error.
Properly tuning for a critically damped response is crucial in precision tasks like robotic surgery or industrial pick-and-place operations.
FAQs
1. What are the main parameters involved in servo motor tuning?
The main parameters are Proportional Gain (Kp), Integral Gain (Ki), and Derivative Gain (Kd). These gains affect how the motor responds to control signals and corrects errors.
2. How do environmental factors affect servo tuning?
Environmental conditions like temperature and vibration can change motor dynamics, leading to shifts in optimal gain values. It’s essential to consider these factors when tuning for long-term stability.
3. Should I use manual or auto-tuning?
If you need precise control and specific performance, manual tuning is preferable. If you want a quick setup without deep knowledge of the system, auto-tuning is effective.
4. How do I reduce oscillations during tuning?
To reduce oscillations, lower proportional gain (Kp) or increase derivative gain (Kd). Too high Ki can also cause oscillations, so adjust it accordingly.
5. What is the best method for achieving critically damped performance?
For a critically damped response, use a balance of high Kp and moderate Kd to reduce overshoot, while ensuring Ki is just enough to remove steady-state errors.
Conclusion
Servo motor tuning is both an art and a science, requiring an understanding of control parameters, load conditions, and environmental factors. Whether you’re tuning a motor manually or using advanced software, the goal is to minimize position error, reduce oscillations, and ensure reliable performance for your application.
If you’re looking for servo motors and tuning tools to ensure optimal performance, visit our Servo Motor Store for high-quality industrial servo motors.