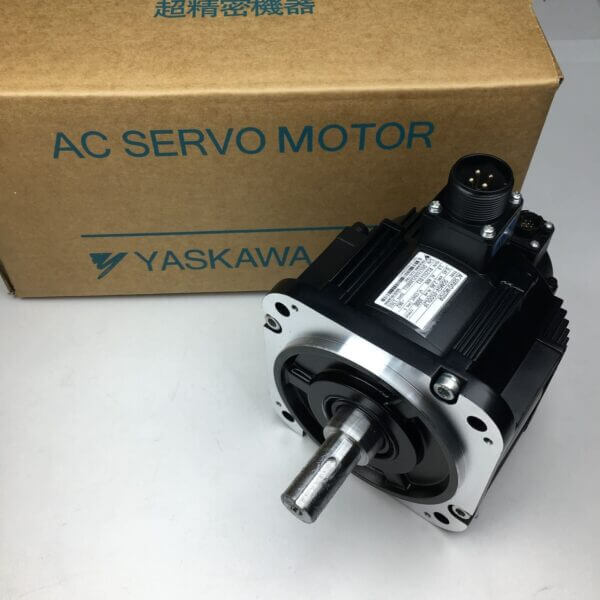
SGMGH-03ACD6B Original Yaskawa Motor for high precision machine tool SGMGH-03ACD6B
Introducing the Yaskawa SGMGH-03ACD6B Servo Motor
In the world of precision engineering, the Yaskawa SGMGH-03ACD6B stands out as a paragon of reliability and exceptional performance. Engineered for high precision machine tools, this servo motor combines advanced technology with robust design to meet the evolving demands of modern applications. Whether utilized in semiconductor manufacturing or food processing machinery, the SGMGH-03ACD6B delivers unparalleled functionality, making it an ideal choice for professionals who prioritize efficiency without compromising precision.
Key Specifications
Feature | Details |
---|---|
Brand | Yaskawa |
Model | SGMGH-03ACD6B |
Rated Speed | 1000 r/min |
Power | 0.3 kW |
Power Supply Voltage | Three Phase AC 200V |
Serial Encoder | 17 Bit Relative Value |
Shaft End Design | Straight Shaft with Screw Key |
Optional Parts | DC 90V Brake |
Max Speed | 6000 r/min |
Protection Mode | Fully Enclosed Self Cooling Type IP65 |
Heat Resistance Grade | B |
Innovative Features
The Yaskawa SGMGH-03ACD6B employs a cutting-edge serial encoder that enhances efficiency by reducing wiring complexity by 50%. This sophisticated motor is optimized for high-speed feeds, providing superior performance even in non-loaded conditions. Notably, the complete separation of the main circuit and control circuit simplifies maintenance, allowing for quick troubleshooting and minimal downtime. The parameter settings can be easily input directly via the servo drive body, further streamlining operations.
Applications
From robotics to food processing, the SGMGH-03ACD6B is a versatile solution capable of addressing the challenges of various industries:
- Semiconductor Manufacturing Equipment
- Placement Machines
- Punch Printed Circuit Boards
- Handling Machinery
Conclusion
With a commitment to excellence, the Yaskawa SGMGH-03ACD6B servo motor exemplifies top-tier engineering, robustness, and adaptability. Its ability to perform complex mechanical actions through multiple control modes enhances workflow efficiency and synchronization, making it an indispensable asset for today’s precision-driven applications.