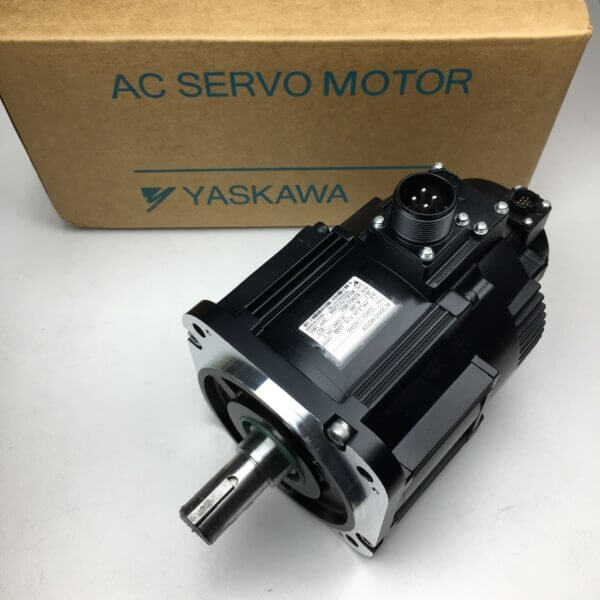
SGMGH-09A2B3S Original Yaskawa servo motor SGMGH-09A2B3S
Introducing the Yaskawa SGMGH-09A2B3S Servo Motor
The Yaskawa SGMGH-09A2B3S is a state-of-the-art servo motor designed for precision and efficiency in various industrial applications. With advanced features and robust performance, this servo motor exemplifies Yaskawa’s commitment to innovation and reliability. Whether you’re in manufacturing, robotics, or any sector requiring high-performance motion control, the SGMGH-09A2B3S stands out as a superior choice.
Key Specifications and Features
Parameter | Specification |
---|---|
Brand | Yaskawa |
Model | SGMGH-09A2B3S |
Type | Servo Motor |
Rated Speed | 1000 r/min |
Power | 0.9 kW |
Power Supply Voltage | Three phase AC 200V |
Encoder | 17-bit absolute value |
Design Sequence | B |
Shaft End | Taper 1/10 with parallel key |
Optional Parts | With oil seal |
Advanced Control and Communication Capabilities
The SGMGH-09A2B3S servo motor excels in functionality, featuring a complete separation between the main circuit and the control circuit, which simplifies maintenance and enhances safety. The intuitive parameter setting device allows for direct input of settings via the servo drive body, streamlining setup processes. With innovative wiring savings through a serial encoder, the motor reduces wiring complexity by 50%, reflecting Yaskawa’s dedication to efficiency.
DeviceNet Communication Support
This model is also equipped with DeviceNet communication capabilities, allowing seamless integration into existing systems. The external power supply drive type supports motors up to 7.5 kW and simplifies motion control implementation. Integration with city-wide DeviceNet software furthers its usability, enabling upper controllers to easily manage servo information and monitor operation statuses for enhanced maintenance efficiency.
Performance Features That Stand Out
Experience outstanding stability and precision with the SGMGH-09A2B3S, featuring advanced vibration suppression and friction compensation functions. These technologies work in tandem to ensure minimal overshoot and enhanced control stability, even amid load fluctuations. Furthermore, the motor excels in tracking control, effectively adjusting to mechanical properties to optimize performance and reduce setup time.