Torque and Servo Motor Stall: How Angular Acceleration and Payload Affect Your System
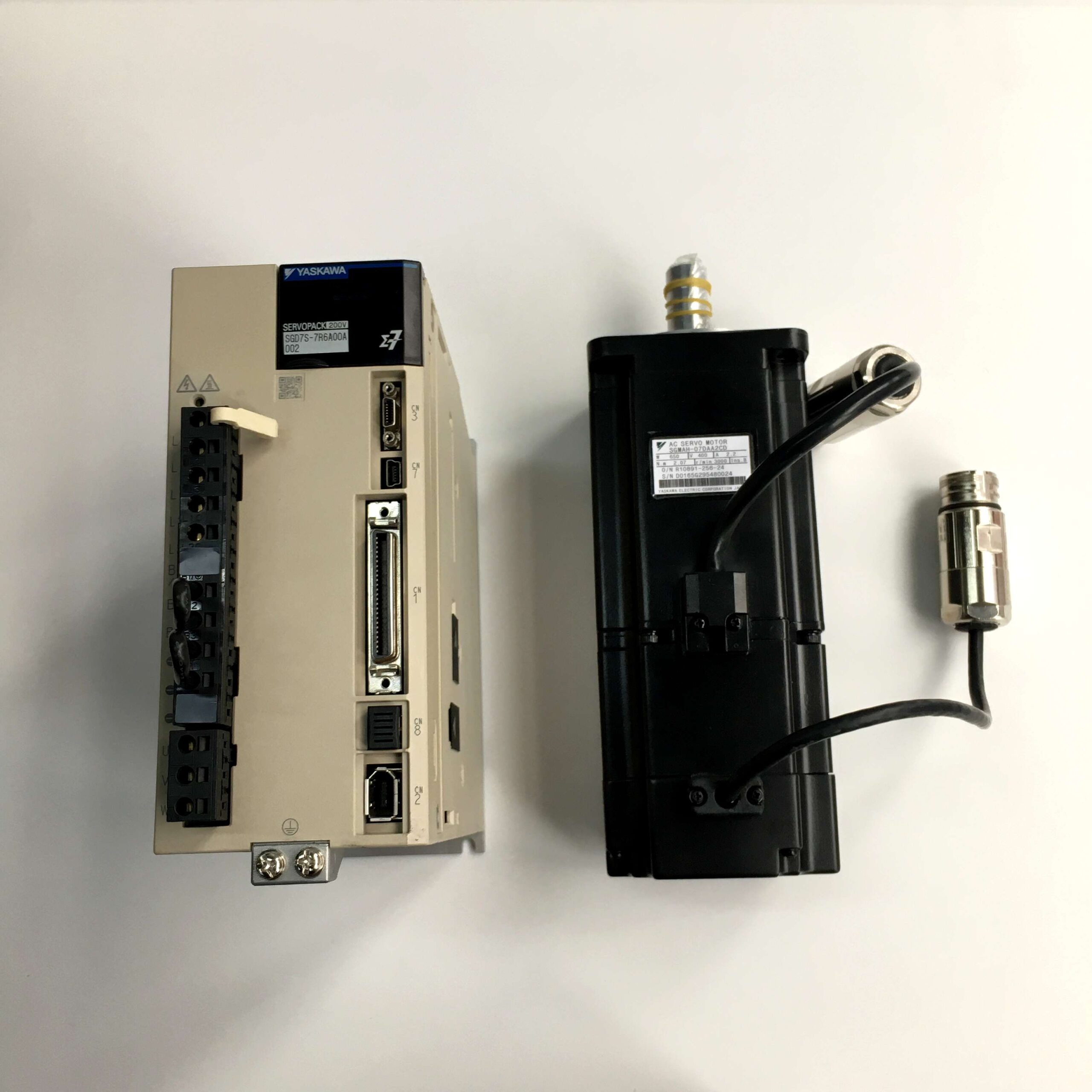
Short Summary
Hello and welcome to this comprehensive exploration of torque, servo, and stall torque within the fascinating world of motion control. If you’ve ever wondered why a motor might stall or how a servo motor can produce the servo torque you need for your automation projects, then this article is just what you’re looking for. We’ll discuss how we, as servo motor manufacturing plants for products, aim to help Automation equipment manufacturers and system integrators leverage advanced servo systems. By the time you finish reading, you’ll understand the fundamentals of stall torque, motor stall, and the key elements of angular acceleration and payload for servo solutions—and see why it matters. We wrote this for you, to help you master essential torque knowledge. Let’s dive in.
1. What Is Torque?
Torque is the rotational force that can cause an object to rotate about an axis. It’s defined as the mechanical work generated by a force acting on an object that leads to a turning effect produced when force is applied to a rotational axis. In other words, torque is the amount of twist you apply, measured in units like N·m (newton-meters), oz-in, or kg-cm.
Quote: “Torque is the newton-meter of rotational motion, describing the work generated by the turning effect on an axis.”
When you have a servo motor, you’re dealing with different types of torque such as stall torque (the maximum torque at zero speed), peak torque, and rated torque. In practical automation, torque is essential because it tells you how much force acting on an object can produce the rotational movement you need. If your payload is heavy or your robotics arm’s load is large, you’ll need the appropriate torque.
But how do you interpret a value like “kg-cm” or “oz-in”? “kg-cm means how many kilograms of kg weight can be lifted at a 1-centimeter radius.” Meanwhile, “oz-in” is a measure where you see how many ounces can be lifted 1 inch from the pivot or fulcrum.
Key Stats:
- 1 kg-cm ≈ 13.888 oz-in.
- 1 N·m ≈ 100 kg-cm (actually 1 N·m = 10.197 kg-cm but often approximated).
Why does torque matter for us—servo motor manufacturing plants for products—especially for Automation equipment manufacturers and system integrators? The more torque you can produce, the heavier payload you can handle without losing performance. But as torque rises, so does the power needed and thus the overall complexity of your system design.
2. How Servo Motors Generate Torque
A servo motor is a closed-loop control device that uses feedback signals to determine how much rotational motion is needed to meet a target position or speed. The torque the motor generates depends on factors like the winding, supply voltage, and the demands placed upon it.
When you control a servo, you essentially issue a command that tries to move the rotational axis from one angle to another. The servo’s internal driver applies current to the spindle, producing a rotational force. If the load (or payload) opposes that motion, the servo has to produce a higher torque to overcome the downward force or radial load.
Interesting Fact: We manufacture advanced servos with power supplies that regulate the voltage seamlessly, thereby allowing automation device manufacturers to enjoy stable performance. This is crucial for ensuring that things like speed and maximum continuous torque remain within safe limits.
Case Study: One of our clients, an automation integrator, faced a challenge with a high-moment of inertia system. We provided a servo with a higher voltage rating, which gave them higher torque output so they could handle faster moves without stalling.
3. Understanding Stall Torque in a Servo Motor
The concept of stall torque is fundamental. In the simplest terms, stall torque is the torque a servo motor can deliver when the output rotational speed is zero. In other words, it’s the maximum torque a motor can produce before it cannot rotate further. This often happens when the force acting on an object is so high that it causes the output rotational speed to become zero, effectively jamming or stalling the motor.
Stall torque is particularly relevant for applications like cnc machines or rc servos where you might hold a heavy arm or a tool in a fixed position. If your system demands a certain amount of torque at zero speed—for instance, a robotic arm holding a load parallel to the ground—you need to ensure the servo’s stall torque meets or exceeds that requirement.
Stall torque is a measure that shows you the torque load that causes the servo to cease rotating. Once you exceed it, the servo stalls and your system can be compromised. So if you’re reading datasheets for servo motors, pay attention to the stall torque specification.
4. What Happens When a Motor Stalls?
A motor stall event occurs when the torque required to move the load surpasses the servo’s ability to generate torque, or if friction is too high. As soon as the motor stalls, it draws higher current, which can overheat the windings, cause damage to the internal electronics, and risk mechanical failure.
This is important to ensure a servo doesn’t remain in stall for extended periods. If it does, it can draw large currents, degrade, or fail. Sometimes, small, thin wire connections can overheat due to the high current. The servo motor’s controller tries to maintain position, but if it’s beyond the torque rating, it’s not going to hold. This scenario is a major concern for automation device manufacturers and system integrators who rely on consistent reliability.
Insight: Many servo manufacturers (like ourselves) will note an expected stall current rating in the datasheet. This rating indicates how much current flows at stall. If your system lacks robust power supplies, you can run into reliability issues.
5. How to Determine the Torque Rating of Your Servo?
Determining the torque rating is about bridging system demands with servo motor performance. When you read a datasheet, you might see nominal torque, stall torque, and peak torque. Typically, the difference is:
- Nominal or Rated Torque: The amount of torque the motor can sustain for indefinite periods.
- Peak Torque: A short-term burst capacity above nominal.
- Stall Torque: The torque at zero speed, often near or above nominal torque but with additional heat and current demands.
Equation: Torque (N·m) = Force (N) × radius (m)
Or you might see Torque (kg-cm) = Force (kg) × radius (cm)
But in practice, you’ll see how torque is the newton-meter or how many kg-cm of torque is produced. If you see “maximum continuous torque” in a spec, that aligns with a safe limit for indefinite operation.
Why it matters: Suppose you’re building an arm’s robotic joint to move a certain mass. The servo needs the torque capacity to handle that mass plus acceleration and safety margins.
6. Why Does Voltage Impact Servo Motor Performance?
Higher voltage typically allows a motor to deliver higher torque because the servo can draw more current and maintain stronger electromagnetic fields. Conversely, dropping the voltage can reduce the servo’s capacity to produce torque, hamper speed, or cause the servo stalls earlier.
Take Note: If you are using an arduino or some microcontroller, you might have limited voltage or be forced to adapt to constraints. It’s wise to check the servo datasheet to see the recommended operating voltage range. If you exceed it, you may burn the servo. If you’re too low, you can’t increase the torque to levels you need.
Personal Experience: As a servo motor manufacturing company, we often advise system integrators on custom voltage solutions. Many of them are looking for that sweet spot between motor stall margin and minimal power consumption. We design servo solutions so you’re not forced to overcompensate, but you still get the power you need.
7. How to Calculate the Torque You Need for Your Servo?
One crucial question for any engineer is: “How do I calculate the torque you need for my servo?” Let’s break it down. Suppose you have a mechanical arm rotating around an axis of rotation. The load weighs X kilograms, the distance from the pivot is Y centimeter or meter, and you have a desired angular acceleration or a change in its velocity in a given time.
Step-by-Step:
- Determine the Force: The mass times gravity factor (9.8 m/s^2) gives you the force. If mass is in kg, you get force in newtons.
- Multiply by the lever arm: The distance from pivot to load. That yields a torque in N·m or kg-cm or oz-in.
- Account for Acceleration: The moment of inertia plus the desired rotational speed might require extra torque for dynamic moves.
- Safety Margin: Add 20–30% buffer to ensure reliability.
Example: If your mass is 2 kg, at 10 cm from the pivot, the torque is about 2 kg × 10 cm = 20 kg-cm. That’s about 277.76 oz-in. If you want faster acceleration or you have friction, you’ll add more margin. This is how you calculate the torque you need. And don’t forget about peak torque vs. continuous torque. You also might factor in how the object has to any change in velocity can cause spikes in required torque.
In short: 1) Evaluate load. 2) Evaluate lever arm. 3) Evaluate speed/acceleration. 4) Compare with servo specs.
8. Reading a Servo Motor Datasheet: Key Factors
When browsing datasheets for servo motors, keep a close eye on key parameters:
- Rated Torque: The torque you can rely on for continuous operation.
- Stall Torque: The torque load that causes the servo to cease rotating. If you exceed this, the servo may burn out.
- Peak Torque: The highest short-term torque.
- Voltage Range: Operating window to ensure normal function.
- Current: Pay attention to stall current, which can be significantly higher than running current.
Real-World Example: You might see a spec that says “stall torque is the torque at 1.2 A current draw” or “maximum torque = 20 kg-cm at 7.4 V.” Those statements tell you exactly the limit your servo can sustain.
When you look at a servo motor’s datasheet, also check for servo motor performance graphs that plot torque and speed. Notice how torque can drop off at higher speeds. Meanwhile, if your load is heavy at low speed, you risk stall.
Pro Tip: Watch out for temperature ratings. When the servo overheats, performance can degrade. That’s one reason we have advanced thermal designs in our manufacturing processes, ensuring durability in demanding automation environments.
9. FAQ on Servo Torque and Motor Stall
1. How do I know if a servo is stalling?
If your servo is trying to move but can’t advance, and you notice a rise in current or temperature, your servo is likely in stall. This scenario might show up as a whirring sound or no motion.
2. What is the difference between rated torque and stall torque?
Rated torque is a safe continuous output. Stall torque is the peak torque at zero speed—the torque required for a joint to hold position without rotation. Exceed stall torque, and the servo stalls or overheats.
3. Does higher voltage always give me higher torque?
Generally, yes. A higher voltage can push more current into the servo, boosting torque. But there’s a limit—exceed the recommended voltage, and you risk burning out the electronics.
4. How does torque relate to radial loads or offset loads?
Torque and radial loads connect via your lever arm. If your load is parallel to the ground, you have to overcome gravity plus friction. The servo calculates net torque from the offset distance (the radius) times the weight.
5. Is the servo torque all I need to consider for system design?
Torque is crucial, but you should also factor things like speed, moment of inertia, motor stall current, and thermal capacity. A servo’s capability depends on all those factors combined.
10. How to Apply These Principles in Real Automation Systems
When implementing servo solutions in industrial or robotics scenarios, it’s not just about the motor. You need to consider stuff like the mechanical arrangement, the feedback control, and how you’ll handle peak torque demands. We, as a servo motor manufacturing company, have worked on numerous projects where the user needed to optimize for quick moves or hold heavy loads. Here’s how:
- Select the Right Model
- Evaluate your payload and your desired speed.
- Compare that to the servo’s stall torque and rated torque.
- Review or Provide a High-Quality Power Source
- Ensure your power supplies can deliver stable current. If the servo needs, e.g., 2.5 A at 7.2 V for peak torque, plan accordingly.
- Test for Thermal Management
- If you’re pushing near the servo’s limit, keep an eye on temperature. Add coolers or heat sinks if necessary.
- Adapt the Drive System
- Sometimes a gearbox or belt drive can reduce the required torque, or help with rotational precision. Evaluate these mechanical solutions in tandem with servo specs.
Case in Point: A system integrator needed a servo to drive a heavy CNC table. We recommended a servo with 30% margin on stall torque. They also upgraded from a 24 V to 48 V supply for higher voltage benefits, which gave them the reliability and answer you’re looking for.
Who We Are and Why Contact Us
We’re a servo motor manufacturing plant for advanced industrial applications. Over the years, we’ve partnered with Automation equipment manufacturers and system integrators worldwide, delivering servo systems for cnc machines, robotic arms, and more. Our depth of experience ensures we can guide you to the perfect servo solution that balances your torque required, rotational demands, and system constraints. Let’s look at some of the solutions we’ve recently provided:
- High-Efficiency Yaskawa Servo Motor – Perfect for mid-range automation with quick acceleration and superior stall torque.
- Panasonic Servo Motor – Great for smaller, agile systems requiring accuracy in rotational speed adjustments.
- Custom Datasheets for Servo Motors – We produce detailed data so you can see exactly how to handle your application.
If you’re interested in seeing some of the best servo motors on the market, check out these valuable links:
- Explore Yaskawa Servo Motor Solutions
- Browse Panasonic Servo Motor Range
- Find More at Servo Motor Store
- Original Yaskawa Single Axis Servo Driver SGD7S-3R8A20A
- Discover High-Performance Motor Options
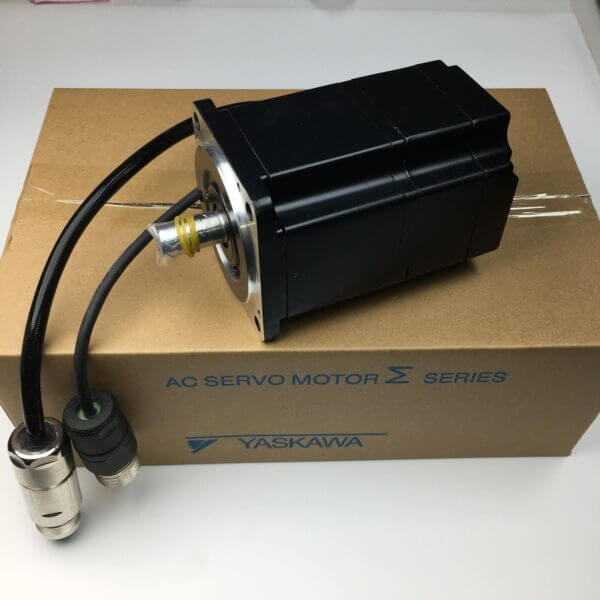
Bullet-Point Summary (Key Takeaways)
- Torque is crucial: It’s the rotational force measure, typically in newton-meters or kg-cm or oz-in.
- Stall torque indicates the maximum torque at zero speed—exceed it, and the servo stalls.
- Voltage also affects torque output. Using higher voltage can yield higher torque, but watch out for limits.
- Check your datasheet thoroughly for servo motor performance specs such as peak torque and maximum continuous torque.
- Thoroughly calculate the torque you need for your servo by factoring your load, lever arm, friction, and angular acceleration.
- We are a servo motor manufacturing plant, helping Automation equipment manufacturers and system integrators find the torque rating to suit demanding industrial systems.
- Important to ensure you manage motor stall to avoid damaging the servo.
This is your one-stop resource for everything you need to know about torque and stall torque in servo motors. We trust this information will serve you well in your automation designs and system integrations. If you’re looking for high-quality servo solutions that can handle your next big project, we’re here to help you experience the power of well-engineered servo systems. Reach out today!