Unleashing the Potential of the Servo Motor for Precise Control in Industrial Applications
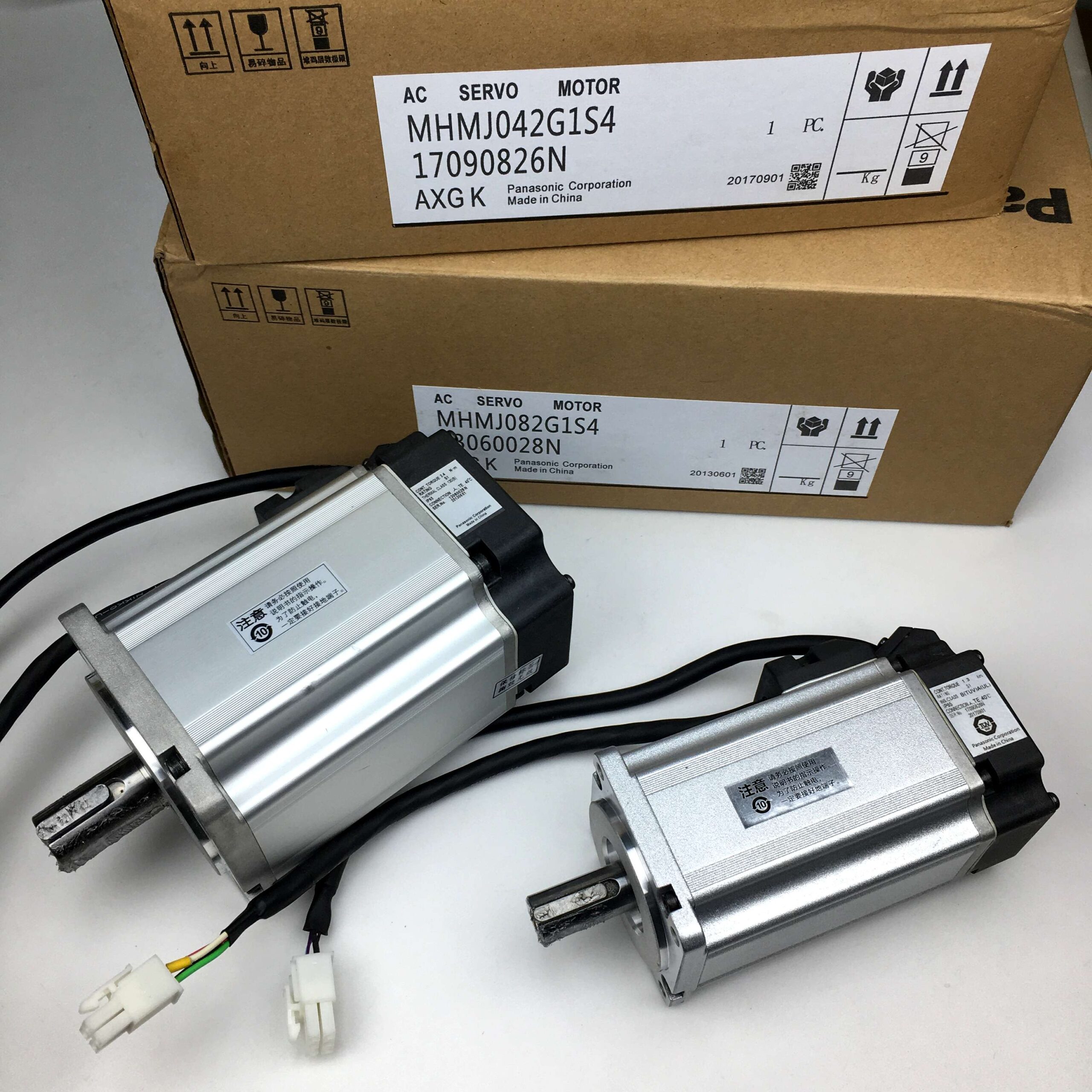
Are you curious about the servo motor, its capabilities, and motor and how it works? In this comprehensive guide, I’ll explain the essential aspects of servo motors, focusing on servo system optimization and precise control for industrial applications. This article is worth reading if you want to understand used in industrial settings, used to operate advanced machinery, and power numerous automation systems for maximum efficiency.
As a servo motor manufacturing specialist with Yaskawa Servo Motor and Panasonic Servo Motor product lines, I aim to share my expertise in motion control and highlight how these motors can upgrade your entire automation workflow. Whether you’re an automation equipment manufacturer, a system integrator, or an industrial robot developer, you’ll discover how the right servo drive can transform your processes.
1. What Is a Servo Motor and How Does It Work?
A servo motor is a self-contained power unit used for motion control. Unlike ordinary motors, a servo motor is designed to offer precise control over its speed and position. Essentially, it’s a motor is a self-contained electrical device that moves to a desired position using a closed-loop system. The term “closed loop” means it constantly compares its actual position to the target point and makes corrections accordingly.
Inside the motor, you’ll often find a gear system for torque conversion, a sensor, and an encoder to track position of the motor. The output shaft couples to your machinery, so the servo motor can move or rotate parts as needed. Because the servo motor is designed for motor and how it works in a variety of control tasks, these motors are widely applied in robotics, CNC machinery, packaging lines, and more.
Fun Fact: A servo motor can handle tasks where even a small error in angle of the motor shaft matters, making them ideal for applications that demand high precision.
By design, the servo motor is a self-contained power solution for controlling rotational or linear motion, guaranteeing you get the exact motor operates velocity that a regular motor cannot deliver with such accuracy. This is one of the reasons servo motors excel in advanced industrial applications.
2. Why Are Servo Motor Applications Crucial in Automation?
Modern automation demands quick responsiveness, control of position, and reliability. This is where servo motors are used in large numbers. Our servo motor manufacturing plants (specializing in Yaskawa Servo Motor and Panasonic Servo Motor) produce high-quality solutions that integrate seamlessly into:
- Automated assembly lines
- Pick-and-place robotics
- Collaborative robots
- Packaging machines
- Laboratory equipment
Servo motor applications focus on controlling the output shaft with precise control, ensuring the motor used can achieve complex movements or hold desired position under load. Thanks to efficient design, servo motors also reduce motor failure, saving on downtime costs. As automation equipment manufacturers and system integrators, you benefit from their small form factor and robust design.
Lastly, servo motors provide consistent performance even in harsh industrial settings. They do so using a feedback device like an encoder or sensor, plus a robust control circuit, making them ideal for applications in high-speed or heavy-load tasks.
3. Which Types of Servo Motors Dominate the Market?
Over the years, the types of servo motors have evolved. Servo motors are classified in part by their internal structure and control method. Several types of motors are relevant, but in a servo context, we typically see three broad categories:
- DC Servo Motor
A dc servo motor relies on direct current for power. They’re often chosen for smaller-scale tasks requiring lighter torque. Because they run on direct current, a dc motor typically needs more maintenance than an ac servo motor but provides simpler control. - AC Servo Motor
An ac servo motor (including the synchronous ac servo motor) offers more torque at higher speeds. These devices are popular in heavy-duty industrial applications. They are more durable, handle larger loads, and require less upkeep. - Brushless Servo Motors
A more advanced type of servo: brushless servo motors typically feature less wear, generating smoother operation and greater reliability. Because they’re brushless, these motors handle repeated cycles under stressful conditions.
As an example, you can explore our Yaskawa Servo Motor and Panasonic Servo Motor categories at the Servo Motor Store to see motor used with advanced features. We also function as a Servo Motors Distributor offering wide-range solutions for different applications.
4. How Does a Servo System Enable Position Control?
A servo system revolves around the principle of continuous feedback. It uses a feedback system to sense the position of the motor, comparing it to the reference command from the controller. This concept allows servo control to maintain a stable speed, angle, or linear movement at all times.
Closed-Loop System & Feedback Device
Within a servo system, a closed-loop system ensures the motor receives signals from the feedback device—for instance, an encoder. The motor controller (or motion controller) processes this data and sends corrections back to the controller circuit. Because of that closed loop, the servo can move swiftly or gently, halting instantly at the correct desired position.
Control Circuit for Precise Positioning
A control circuit in the servo system interprets input signals from your PLC or automation environment. It then calibrates how much power is sent to the motor. This fast interplay between the servo driver or servo controller ensures servo motors operate effectively, delivering consistent rotation or translation in even the most demanding tasks. The process is so refined that minor differences in speed of the motor or load can be quickly corrected, guaranteeing stable motion.
5. What Are the Advantages of Servo Motors Versus Other Motor Types?
The advantages of servo motors revolve around precise control, speed, and reliability. Although a stepper motor is commonly used for mid-range tasks, it lacks the dynamic correction ability found in servo motors. In fact, servo motors and stepper motors differ significantly in that servos track speed and position via feedback.
Servo motors provide precise control through:
- Faster Response
Because the servo drive can instantly correct error, the motor adjusts swiftly. - Higher Torque
Many servo motors handle higher torque loads, maintaining consistent force even under abrupt speed changes. - Smoother Rotation
A servo motor is a self-contained device with advanced electronics, so it avoids “stepping” vibrations that might occur with stepper motors.
This is why servo motors also shine in tasks like CNC milling, 3D printing, robotic arms, and beyond. They’re making them ideal for applications where minuscule errors cannot be tolerated. Moreover, servo motors offer energy savings due to efficient motion profiles.
6. Why Do Servo Motors in Robotics Require Sensor Feedback?
Servo motors in robotics rely on real-time data from sensors to assure accurate position control. Because you want the output shaft or motor shaft to match your automation commands, you need constant updates on the servo’s orientation and velocity. This is typically managed by an encoder or sensor.
When combined with a servo drive, the sensor feedback quickly calculates if the servo is reaching the correct orientation or if there’s a load mismatch. If the robot arm is deviating or the manipulator is jammed, the servo motor can be promptly powered down to prevent motor failure or damage to other components.
Quote: “Sensor feedback ensures continuous alignment between the robot’s commanded position and actual motion, guaranteeing safety and performance.”
Robotics is a prime example of high-level automation. With servo motors, you gain the advantage of stable, precise movements. Also, many servo motors can be integrated with advanced control circuits to easily interface with your motion control system.
7. How to Select the Right Servo Motor for Your Needs?
Choosing the right servo motor can be challenging given all the specifications. Here are some guidelines:
1. Motor Sizing
Consider both speed and torque requirements. If the application demands high torque, look to an ac servo motor or a brushless servo motors design. For simpler tasks, a smaller dc servo motor might suffice.
2. Control Circuit & Feedback Device
Make sure the servo controller or drive is compatible with your PLC or CNC system. The feedback device must match the precision level you expect, especially if you require sub-degree accuracy or advanced position control.
3. Environment & Conditions
Will the servo motor run in high heat or dusty environments? Always check IP ratings and cooling methods. Some servo motors also come with specialized housings for extreme contexts, preventing dust infiltration inside the motor.
4. Continuous Rotation Servo & Motion System
If you need indefinite rotation or want the servo can move 360 degrees, a continuous rotation servo type is suitable. Keep in mind the size of the servo and motor sizing to handle mechanical loads.
You can browse our SGD7S-3R8A00A Original Yaskawa Single axis servo driver for an example of a robust servo drive well-suited to advanced motion tasks.
8. Understanding DC Motor Versus AC Servo Motor in Control Circuit
Comparing a simple dc motor to an ac servo motor reveals many differences in how the motor is controlled. Typically, a DC system might rely on brushes for commutation and simpler electronics. Conversely, AC servo solutions revolve around advanced electronics for stable performance under dynamic loads. Both rely on a control circuit for motion.
DC Motor Based vs. AC Motor Based Systems
- DC Motor Based: Often smaller or used for low-torque tasks. Good for cost-sensitive projects. Might generate more heat.
- AC Motor Based: Capable of high torque and consistent speed. Usually found in heavier, more industrial roles. Less brush maintenance.
Meanwhile, servo drives offer improved performance by adjusting power based on instantaneous load changes, yielding a stable motion system for tasks like packaging, printing, or robotic assembly.
9. How Servo Controller and Servo Driver Systems Enhance Performance?
A servo controller or drive orchestrates the motor’s operation by receiving signals from your PLC or CNC. Then, it precisely regulates voltage and current sent by the controller or motion CPU to the motor. This real-time coordination ensures the motor rotates with minimal overshoot or vibration.
Coordinating the Motion Control System
Your motion controller orchestrates multiple axes in sync. The servo driver communicates with each servo motor to ensure consistent moves. For multi-axis robots or printing machines, perfect synchronization is crucial.
Motor driven by a servo driver eliminates guesswork. The driver calculates the difference between the actual position and the commanded position, adjusting the power supply accordingly. The result: consistent, smooth operation with minimal risk of stalling. This synergy powers advanced automation for industrial tasks.
Stat: According to industry reports, servo-driven solutions can increase throughput by up to 30% compared to open-loop motors, while also trimming energy usage.
10. Ways to Use a Servo for Better Motion Control in Industrial Applications
Implementing servo motors are widely used in your manufacturing or robotics environment offers numerous benefits. For instance:
- Used to deliver consistent torque through broad speed ranges.
- Motors are used to power conveyors, pick-and-place arms, or feeders in a wide array of industries.
- Integrating a servo motor is typically straightforward when you match the correct servo drive and control circuit.
In-Depth Look: Motor and How It Works
When discussing motor and how it works in detail, remember that an ac servo motor or dc servo motor:
- Receives control signals from the servo controller
- Interprets them to produce the desired position
- Maintains stable orientation or angle by continuous feedback
Used in industrial machines, servo motors also pair well with modular automation cells. They help you scale production quickly without sacrificing precise control.
Highlight: Synchronous Motor for Accuracy
A synchronous motor can serve as an ac servo motor variant that locks rotor speed to the frequency of the supply. This design means stable positioning is easier to sustain. A synchronous ac servo motor can reach high speed swiftly, useful in packaging or injection molding lines.
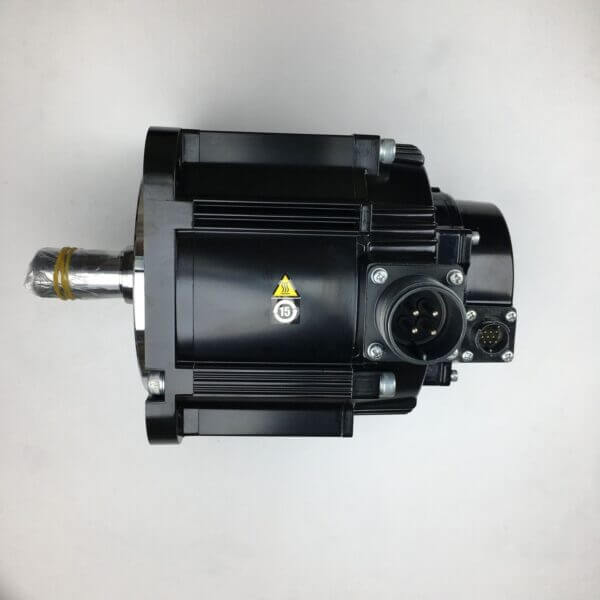
Frequently Asked Questions
1. What is the difference between servo motors and stepper motors?
Although both servo motors and stepper motors deal with controlling position, servo motors excel at maintaining accuracy under load changes. Stepper motor drives can skip steps under heavy load, whereas servo motors use feedback for constant correction.
2. Why do we need an encoder for servo motors?
An encoder acts as the feedback device letting the servo controller know exactly how the servo is positioned. It helps achieve precise control and prevents overshooting the desired position.
3. Can servo motors handle high torque at low speeds?
Yes. Servo motors operate effectively across a wide speed range. Their closed-loop design ensures the motor can handle substantial torque at both slow and fast speeds, preventing unexpected oscillations or stalling.
4. How do I handle motor failure or overload conditions?
Most servo motors incorporate protective circuits to detect overload. The servo drive will typically shut down the motor if it senses abnormal conditions, safeguarding the system from serious damage.
5. What’s the role of a servo driver in my motion control system?
A servo driver translates control signals from your motion controller or PLC into power for the motor based on load conditions. This ensures a stable, precision servo experience.
6. Are servo motors also used to power large industrial equipment?
Absolutely. AC servo solutions are widely used in heavy machinery. Meanwhile, a small dc servo motor might power more modest equipment. Either way, servo motors handle complex tasks, from small-scale lab devices to big robotic arms.
Final Thoughts & Key Takeaways
- Servo motors are classified into DC, AC, and brushless types, each offering unique performance benefits.
- The servo motor is designed for precision servo tasks through a feedback system of encoders and sensors.
- Servo motors also rely on a servo controller or drive to enable continuous adjustments in closed-loop system operation.
- High torque, motor speed accuracy, and advanced correction technology make servo motors offer a strong advantage in manufacturing.
- A robust gear system and real-time feedback keep the position of the motor stable, preventing errors and increasing throughput.
- Motor designed solutions from Yaskawa or Panasonic can integrate seamlessly into your automation environment, used to operate robotic arms, CNC machines, or pick-and-place systems.
If you want to learn more about these high-efficiency servos or have specific questions about customizing a system, I encourage you to reach out. We at our servo motor manufacturing facilities (Yaskawa Servo Motor, Panasonic Servo Motor) are here to support your used in industrial progress.
Bullet Point Summary
- Servo motors in robotics need sensor feedback to ensure control of position and avoid mechanical errors.
- Servo drives offer real-time corrections, making each motor driven axis accurate under dynamic load changes.
- Pairing a servo with a control circuit that supports advanced features leads to stable motion across your entire motion control system.
- Always evaluate motor sizing, environment conditions, and control demands when adopting servo motors.
- Servo motors are widely used in industries requiring complex or repetitive tasks with near-zero error margin.
- Properly matched servo motors minimize motor failure and maintain longevity.
Feel free to contact us for in-depth consultation, or check out our internal links:
- Servo Motors Distributor
- Industrial Servo Motors
- SGD7S-3R8A00A Original Yaskawa Single axis servo driver
- Yaskawa Servo Motor
- Panasonic Servo Motor
We can customize a solution for your business, ensuring your servo motors seamlessly integrate with your automation architecture. Let’s work together on reliable, cost-effective motion solutions that transform your facility!